What Are Cnc Machined Parts
CNC machined parts represent a cornerstone in modern manufacturing, embodying precision and efficiency through the use of computer numerical control (CNC) technology. These components are crucial across various sectors, enabling the production of intricately designed parts that meet stringent specifications with remarkable consistency. The process involves converting CAD drawings into numerical instructions, which guide machine tools to sculpt raw materials into final products. As industries continually push the boundaries of innovation and design complexity, the role of CNC machining grows increasingly indispensable. Exploring the nuances of this technology further reveals its potential impact on future manufacturing trends and capabilities.
Key Takeaways
- CNC machined parts are components produced using CNC (Computer Numerical Control) machining technology.
- These parts are characterized by their high precision and consistency, thanks to automated control.
- Common materials used for CNC machined parts include metals like aluminum and stainless steel, as well as plastics.
- CNC parts are essential in industries such as aerospace, automotive, and medical devices due to their reliability and precision.
- The process allows for complex custom designs and rapid prototyping, enhancing product personalization and efficiency.
Understanding CNC Machining
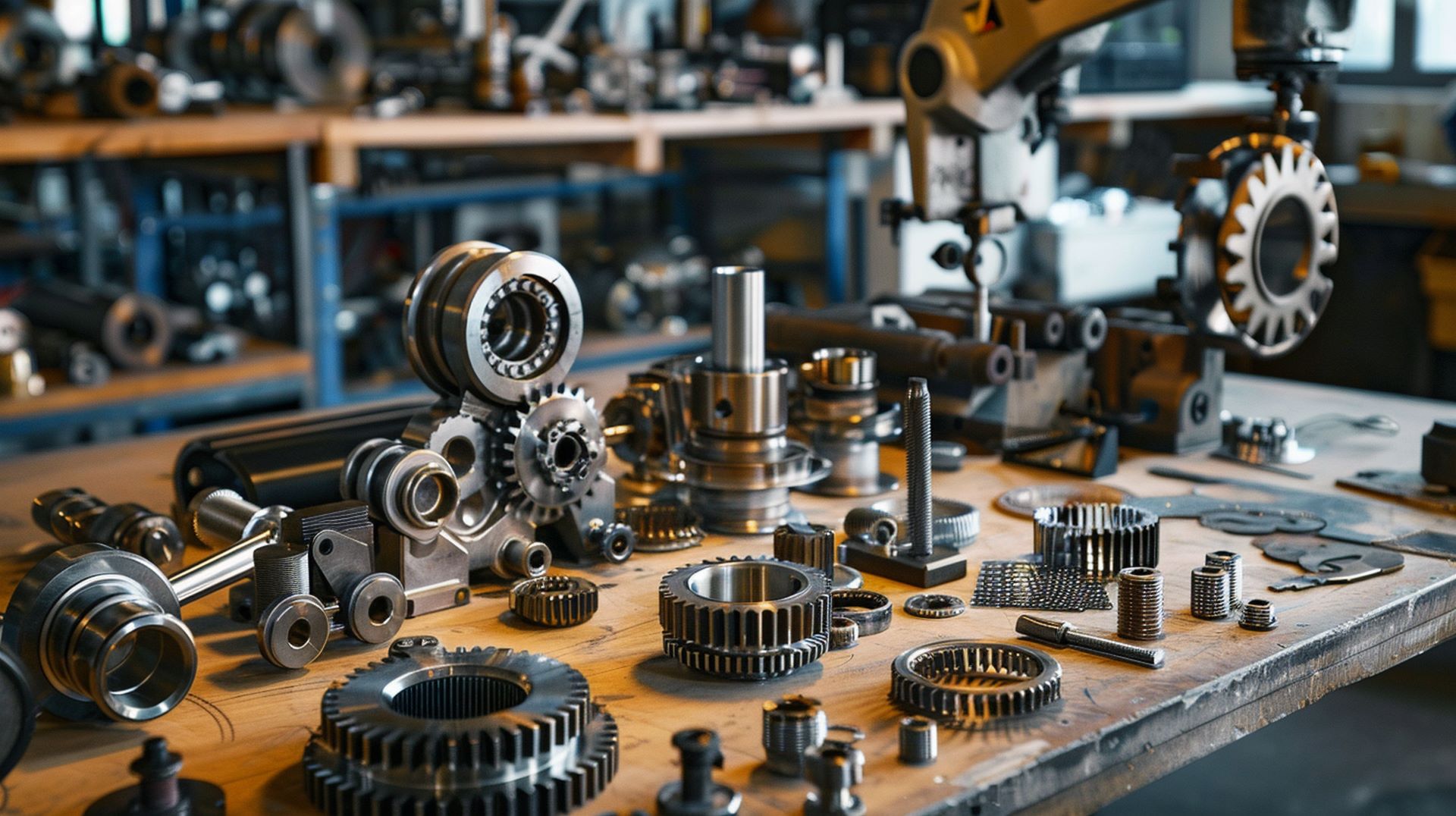
CNC machining is a precision manufacturing process that utilizes computer-controlled machine tools to create intricate parts from a variety of materials. Central to this method is the role of precision engineering, which ensures that every cut, drill, or shave meets stringent specifications with exacting accuracy. This process not only reduces the margin of error to near zero but also consistently reproduces parts that are faithful to the original design specifications.
The advantages of CNC machining extend into production efficiency as well. By automating the control of machine tools through software that dictates movement and operation, manufacturers can significantly reduce setup times and increase the speed of production. This automation allows for continuous operation without human intervention, minimizing labor costs and enhancing productivity.
Furthermore, the ability to quickly switch from producing one part to another without extensive downtime for reconfiguration underscores the flexibility and efficiency of CNC machining.
For industries that demand both precision and efficiency, CNC machining provides a reliable solution. Its capability to handle complex designs and perform consistent, rapid production cycles makes it an invaluable asset in the high-stakes environments of aerospace, automotive, and medical device manufacturing.
Types of CNC Machines
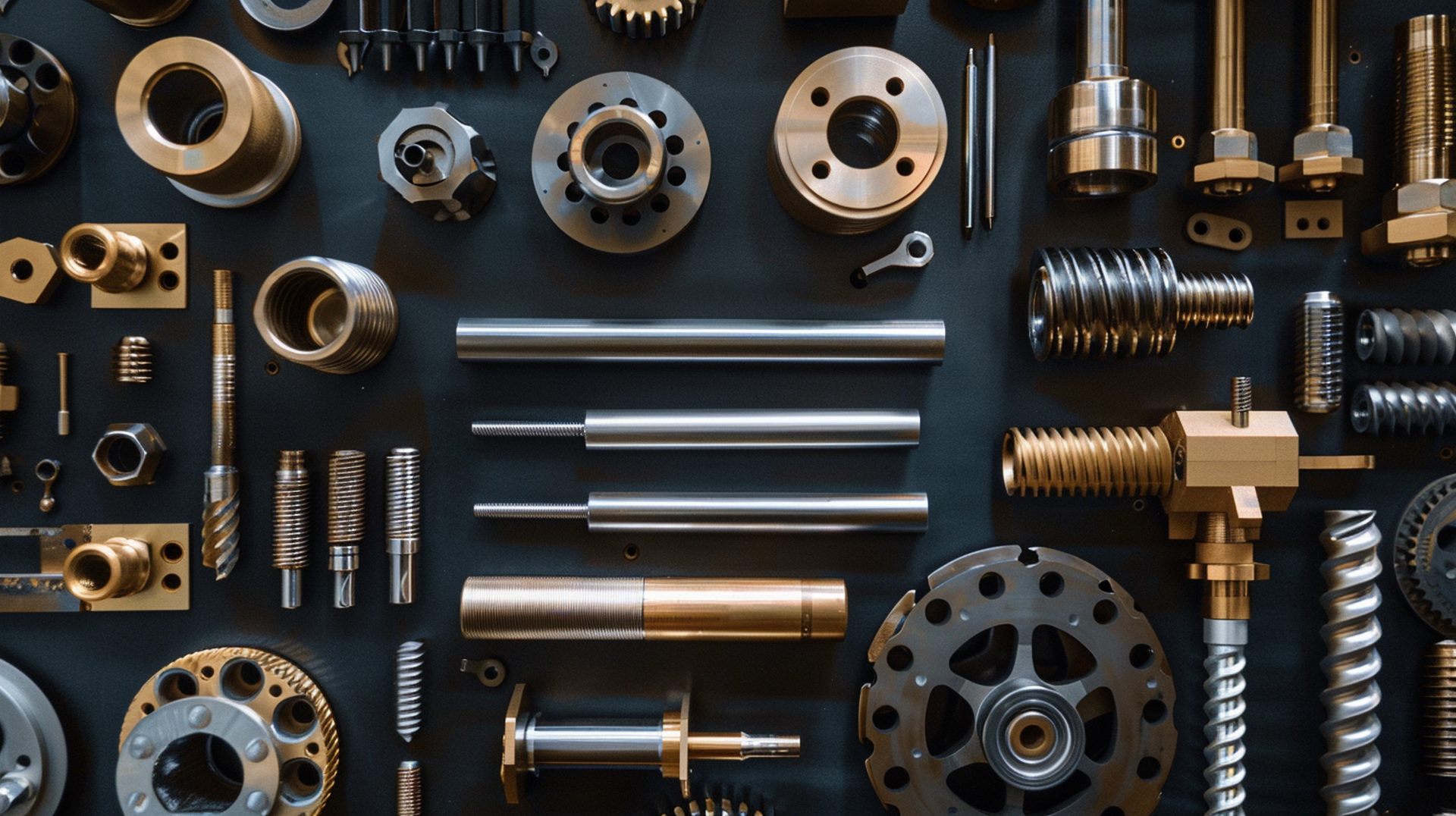
Understanding the various types of CNC machines is key to appreciating their role in modern manufacturing processes. Among the diverse array of equipment, CNC lathes and CNC routers stand out for their specialized capabilities and broad applications.
A CNC lathe is imperative for producing precise, circular or cylindrical shapes including tubes, bushings, and shafts. Its design allows for the workpiece to rotate in a chuck while various tools perform the cutting. What sets CNC lathes apart is their ability to achieve high precision and repeatability, which are vital for industries requiring uniformity across large production runs. Operators can have direct control over production details, optimizing the process for efficiency and quality.
On the other hand, a CNC router, primarily used for cutting harder materials, provides versatility in handling wood, composites, and some types of metals. It employs a spindle that moves along multiple axes, offering expansive possibilities in shaping, engraving, and hollowing out materials. This type of machine is essential for tasks requiring intricate designs and patterns, allowing manufacturers to execute complex projects with precision.
Both types of machines enhance operational control, ensuring that production is not only efficient but also meets exacting standards. These technologies empower manufacturers to push the boundaries of what can be achieved in CNC machining.
Materials Used in CNC Machining
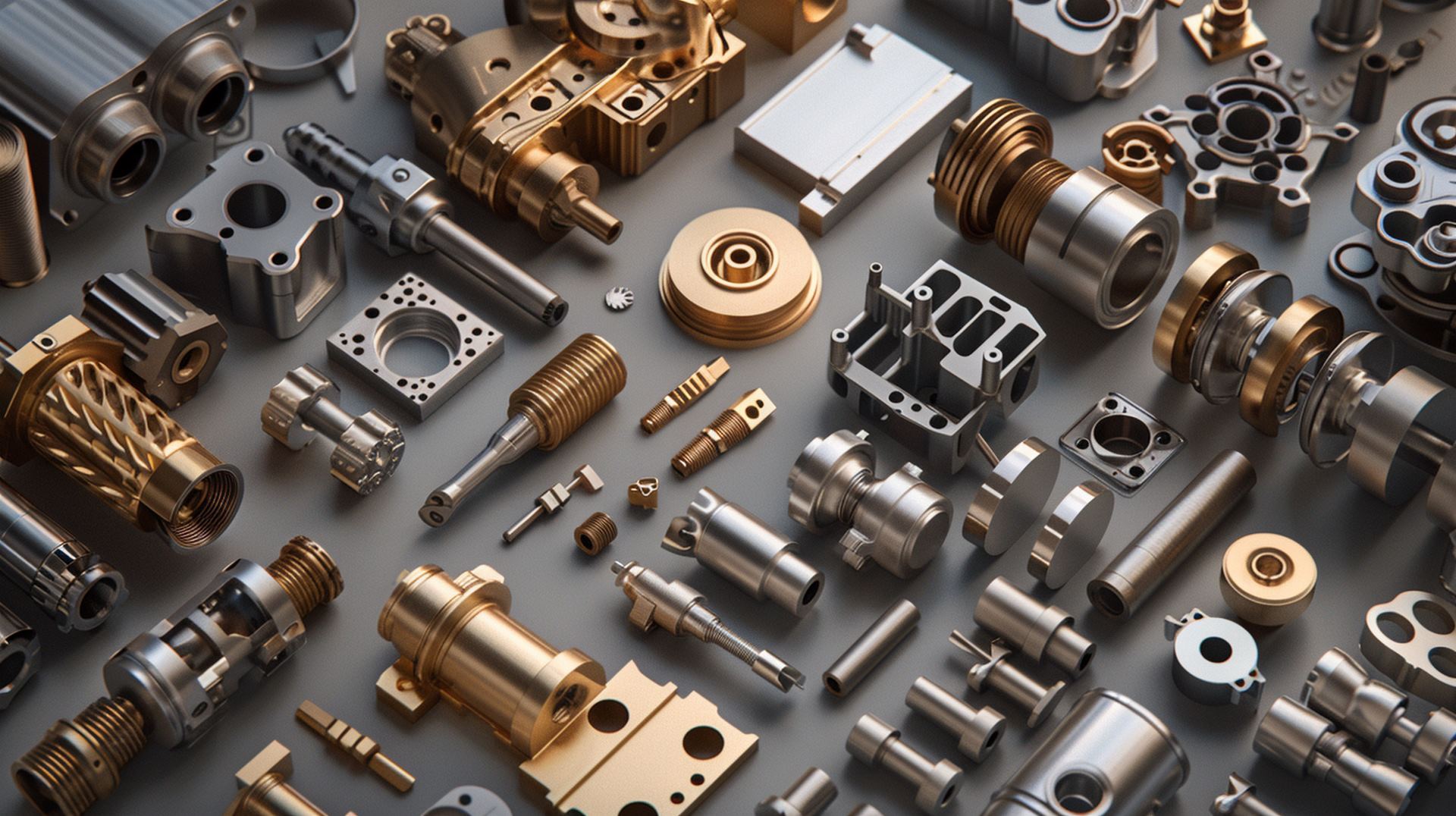
The selection of materials for CNC machining is crucial, as it directly influences the quality, functionality, and durability of the finished parts. Selecting the appropriate material depends on the specific requirements of the machining processes and the intended use of the machined components.
Metal fabrication, a core aspect of CNC machining, involves various metals and alloys, each offering distinct properties and benefits. Commonly used materials include aluminum, known for its lightweight and corrosion resistance, making it ideal for aerospace and automotive applications. Stainless steel is favored for its strength and resistance to corrosion, suitable for medical devices and food processing equipment. For applications requiring high thermal conductivity and electrical insulation, copper and its alloys are preferred.
Additionally, plastics like polycarbonate and acrylic are used for their versatility and lower cost in less demanding environments. Each material choice must align with the machining capabilities, as some materials are more challenging to machine than others, influencing the overall cost and feasibility of the project.
Applications of CNC Parts
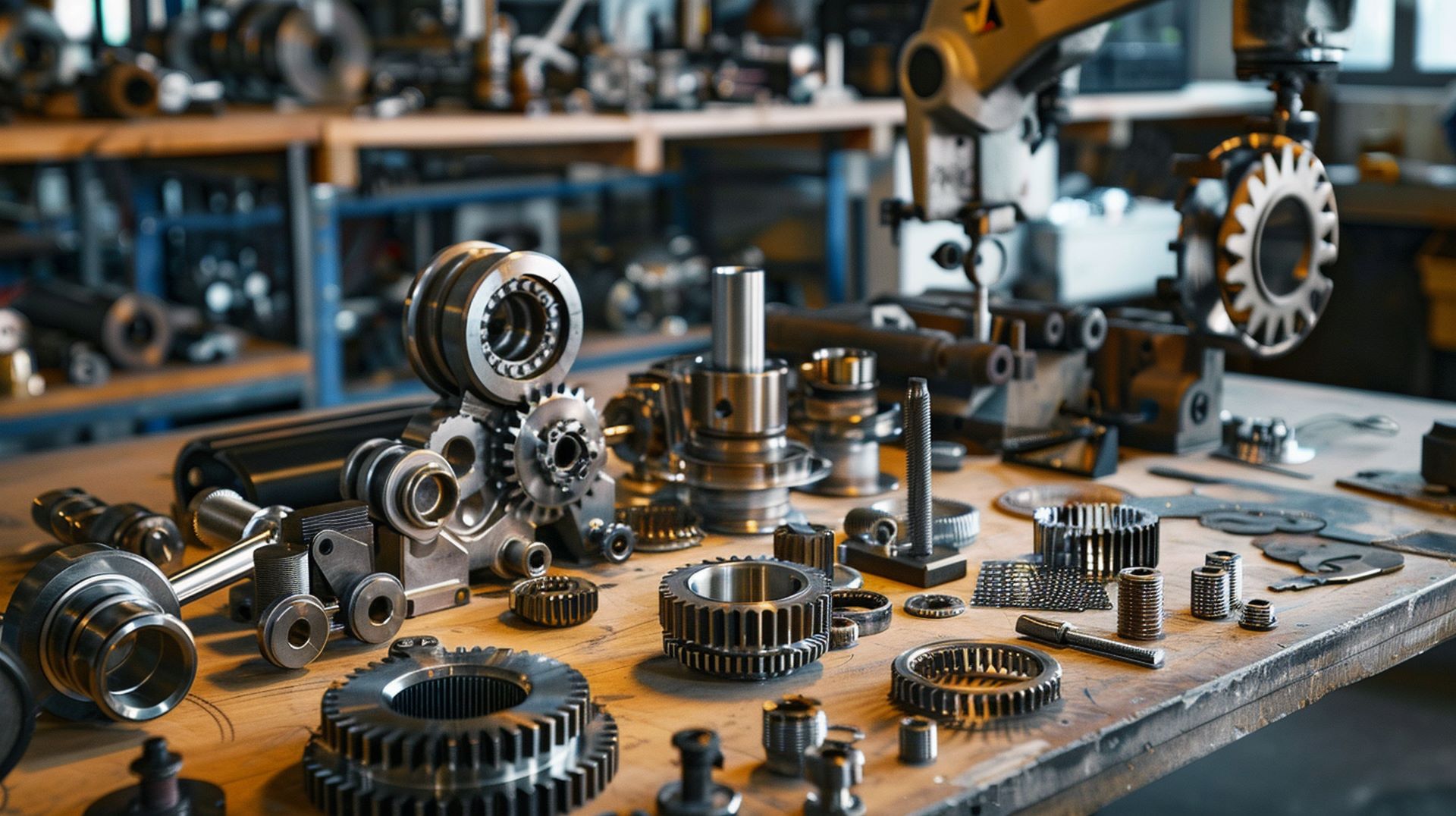
CNC machined parts are integral to numerous industries. They play essential roles in aerospace component manufacturing and automotive assembly lines.
In aerospace, precision and reliability are paramount. CNC technology facilitates the production of highly accurate and durable parts critical for aircraft.
Similarly, the automotive sector relies on CNC machining for the efficient production of complex components. These components must meet stringent safety and performance standards.
Aerospace Component Manufacturing
In aerospace component manufacturing, CNC machining plays a pivotal role in producing high-precision parts essential for aircraft performance and safety. This technology epitomizes precision engineering, which is crucial in an industry where every micrometer counts. Aerospace innovation continuously pushes the boundaries of what can be achieved, and CNC machining is at the heart of this progress, enabling the creation of complex components that meet stringent quality standards.
CNC machining offers unparalleled control over the production process, allowing manufacturers to produce parts with extreme accuracy and consistency. This capability is vital for the aerospace sector, where the reliability and durability of each component can be the difference between success and failure. The table below provides an insight into the key applications of CNC machining in aerospace component manufacturing:
Component | Material Used | Importance |
---|---|---|
Engine parts | Titanium, Aluminum | Heat resistance, lightweight |
Landing gear | Steel, Titanium | Durability, strength |
Airframe structures | Aluminum, Composites | Rigidity, corrosion resistance |
These applications highlight how CNC machining is integral to maintaining the high standards required in aerospace engineering, ensuring that every flight is safe and efficient.
Automotive Assembly Lines
Automotive assembly lines extensively utilize CNC machined parts to ensure high precision and efficiency in vehicle manufacturing. These components are integral in areas where accuracy and durability are paramount, ranging from engine parts to transmission gears.
The integration of CNC technology in manufacturing processes allows for the creation of intricate and complex parts that meet exacting standards, thereby enhancing the overall quality of the automobiles.
Robotic automation, empowered by CNC machined parts, plays a significant role in streamlining production processes. Robots equipped with CNC parts operate with a level of precision that manual processes cannot match, significantly reducing the margin for error and increasing the speed of assembly.
This automation not only optimizes productivity but also enables a more consistent assembly of vehicles, ensuring each unit conforms to stringent specifications.
Quality control is another critical aspect deeply woven into the fabric of automotive assembly lines using CNC machined parts. The precision inherent in CNC machining ensures that each part is manufactured within tight tolerances, which is crucial for the high-performance standards expected in the automotive industry.
This level of precision guarantees that all parts fit perfectly, reducing the likelihood of recalls and maintaining the manufacturer's reputation for reliability.
Advantages of CNC Machining
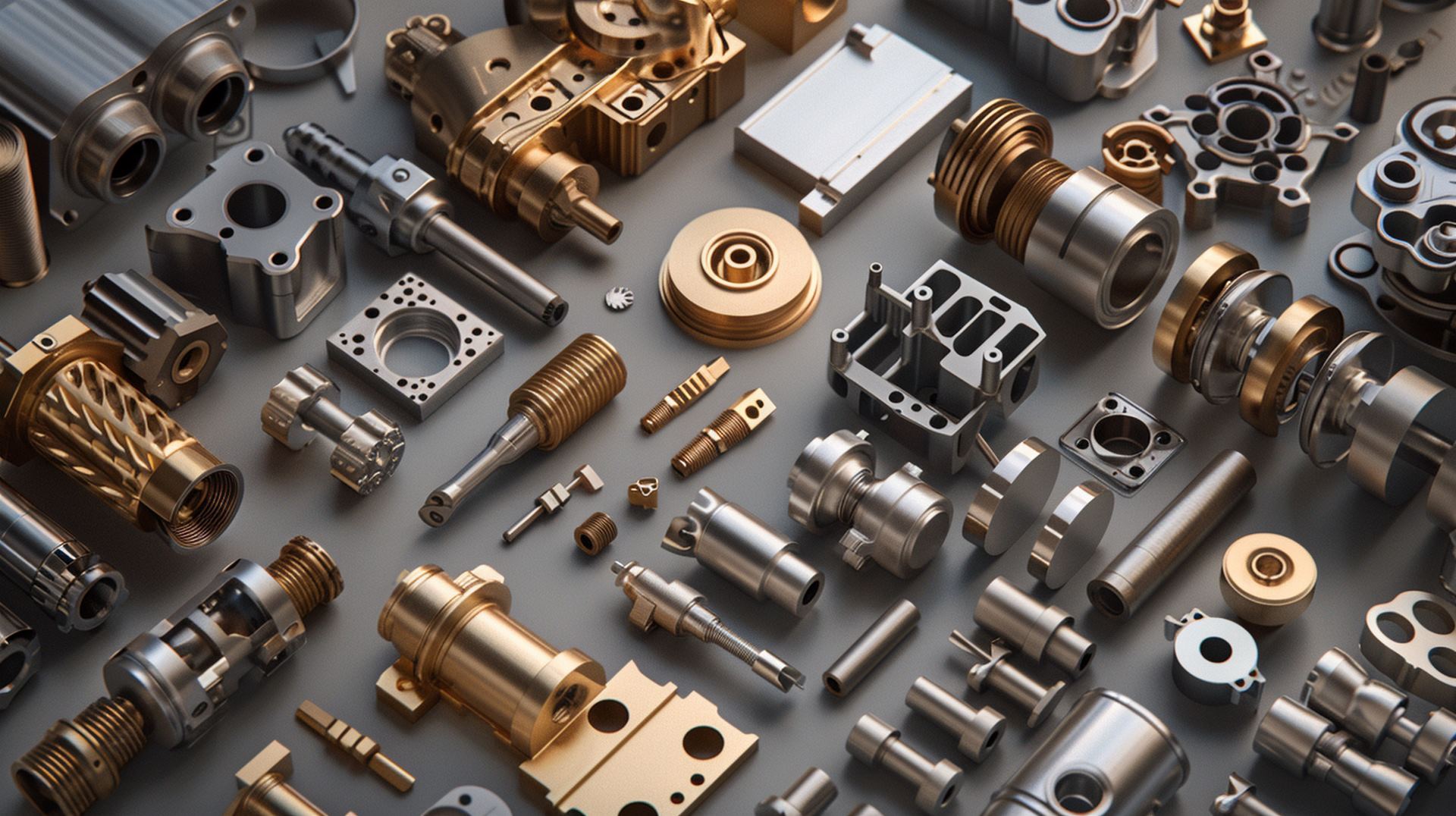
Precision, speed, and efficiency are among the key advantages of CNC machining. This advanced manufacturing technology allows for cost efficiency and precision manufacturing, which are crucial in maintaining competitiveness in various industries. CNC machines automate the control of machine tools with high accuracy using computer programming, which minimizes human error and enhances the quality of the output.
Increased productivity is another significant benefit. CNC machines operate faster than manual counterparts and can produce large quantities of complex parts quickly and continuously without compromising the design's integrity. This capability is especially beneficial for industries requiring the rapid production of custom designs, as modifications to machine instructions can be made swiftly without halting production.
The following table highlights key aspects of CNC machining advantages:
Advantage | Description |
---|---|
Cost Efficiency | Reduces labor costs and material wastage. |
Precision | Achieves high accuracy in parts production. |
Customization | Facilitates the creation of complex custom designs easily. |
For organizations aiming to dominate their market segments, leveraging the control and capabilities of CNC machining offers a strategic advantage, ensuring both quality and innovation in product development.
Future Trends in CNC Technology
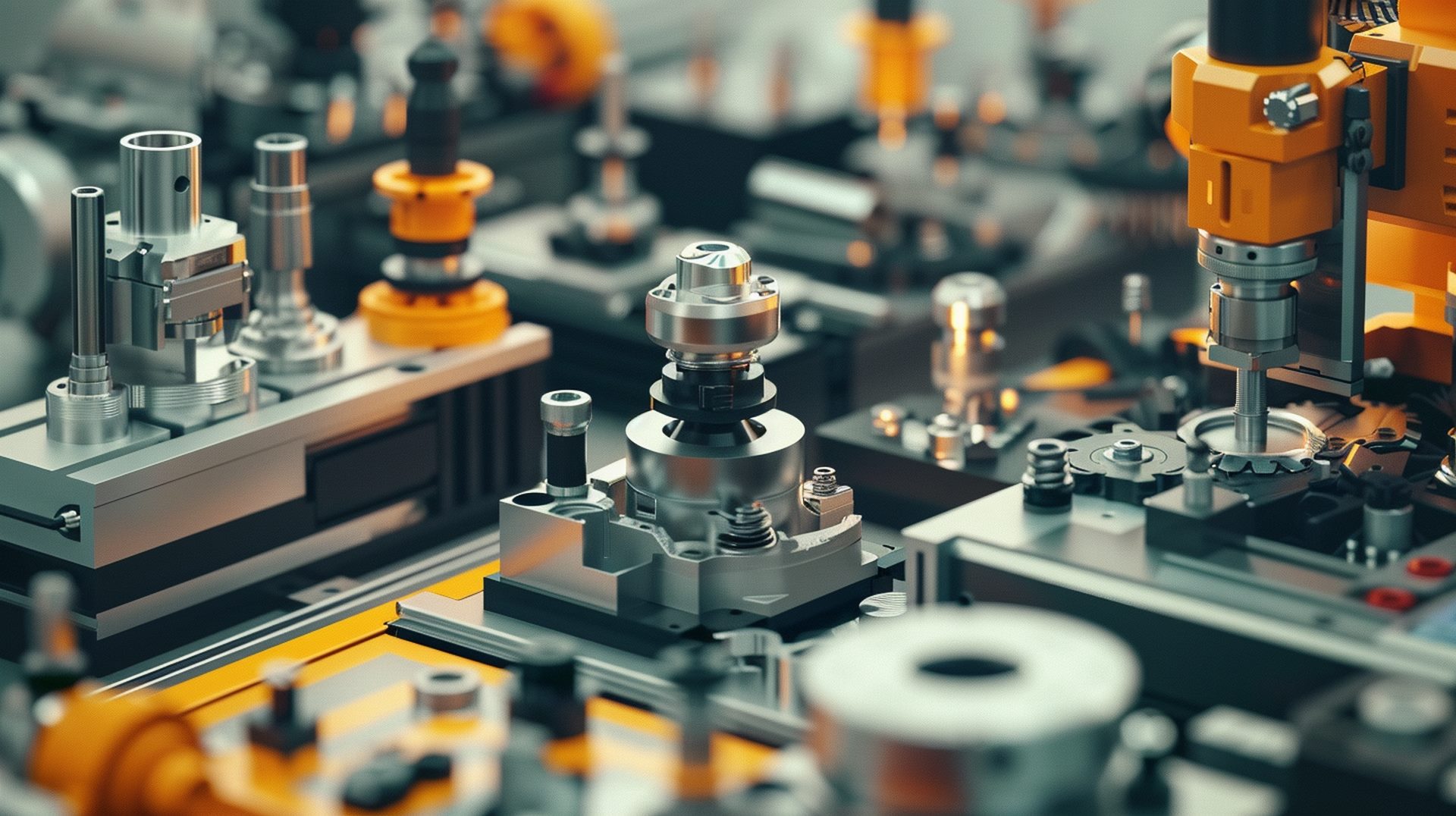
As we look towards the future of CNC technology, two significant trends are poised to reshape the industry.
The integration of advanced materials promises to enhance the capabilities and applications of CNC machined parts, enabling more complex and durable products.
Concurrently, the evolution towards smart factories underscores a shift towards automation and data-driven manufacturing, optimizing efficiency and reducing human error.
Advanced Materials Integration
The integration of advanced materials in CNC technology is setting the stage for transformative enhancements in manufacturing capabilities. Embracing Industry 4.0 strategies, manufacturers are leveraging the potential of precision engineering to not only optimize the performance of machined parts but also redefine the paradigms of what these materials can achieve. This evolution is pivotal as it aligns with the increasing demand for components that offer superior properties such as enhanced strength, lightweight, and high temperature resistance.
Innovative design approaches are being synchronized with advanced manufacturing processes to push the boundaries of CNC machining. The introduction of materials like ultra-high-performance polymers, advanced ceramics, and composite materials allows for the development of components that were once deemed impossible to create. This integration is not merely about adopting new materials but also involves rethinking the entire manufacturing workflow to enhance efficiency and output quality.
The strategic infusion of these sophisticated materials into CNC processes empowers businesses to maintain a competitive edge by increasing the durability and functionality of parts. This not only meets the high standards required by evolving industries but also reduces waste and optimizes resource utilization, thereby streamlining production costs and boosting economic efficiency.
Smart Factory Evolution
CNC technology's evolution into smart factory systems represents a significant leap forward in digital manufacturing capabilities. This transformation is deeply rooted in Industry 4.0 advancements and is exemplified by enhanced smart manufacturing processes and digital transformation. As CNC machines integrate more seamlessly with interconnected systems, the factory floor is no longer just about mechanical execution but also about intelligent analysis and decision-making.
The implementation of robotic automation in CNC systems notiates unprecedented efficiency and precision. These smart factories are equipped to anticipate maintenance needs, optimize production processes in real time, and adapt to new production demands without human intervention, ensuring a higher level of control and productivity.
To better understand the impact of these trends, consider the following table highlighting key elements of smart factory evolution:
Feature | Impact |
---|---|
Robotic Automation | Reduces human error, increases production speed and operational safety |
Digital Connectivity | Enhances real-time data collection and processing for better decision-making |
Predictive Maintenance | Minimizes downtime by predicting equipment failures before they occur |
This shift not only empowers manufacturers to have greater control over the production environment but also sets a new standard for efficiency and quality in the production of CNC machined parts.
Frequently Asked Questions
How Do Environmental Factors Affect CNC Machining Precision?
Environmental factors such as temperature fluctuations and humidity levels significantly impact CNC machining precision by causing material expansion, contraction, and tool wear, thus challenging the control over the dimensional accuracy of the final product.
What Are the Safety Protocols for Operating CNC Machines?
Safety protocols for operating CNC machines include rigorous training requirements, adherence to emergency procedures, and proper use of safety equipment during machine operation to ensure control and minimize risks in the workplace.
Can CNC Machines Be Used for Artistic Purposes?
Yes, CNC machines can be utilized for artistic purposes, enabling the creation of intricate designs and sculptures. This highlights the machine's versatility in creative applications beyond traditional industrial uses.
How Does CNC Machining Impact Workforce Employment?
CNC machining has transformed the manufacturing landscape, increasing efficiency but also reshaping workforce dynamics. It creates specialized job opportunities, yet impacts traditional roles, necessitating skill adaptation to leverage economic benefits and maintain industry control.
What Are Common Maintenance Issues With CNC Machines?
Common maintenance issues with CNC machines include alignment problems, tool wear, and software malfunctions. Preventative measures and troubleshooting techniques are crucial for ensuring operational efficiency and extending the lifespan of the equipment.
Mikehardware-your trusted custom Cnc Machined Parts manufacturer
In conclusion, CNC machining stands as a cornerstone of modern manufacturing, revered for its precision and flexibility.
The integration of CNC technology has revolutionized production across various sectors, notably increasing productivity.
A compelling statistic highlights this impact: studies indicate that CNC technology can enhance production efficiency by up to 50% compared to traditional machining methods.
As advancements continue, the potential for further efficiency gains and innovation in CNC machining remains significant, promising to reshape future manufacturing landscapes.
At Dongguan Mike Hardware Co., Ltd., precision engineering meets innovation, delivering impeccable CNC product manufacturing solutions. Explore our array of customized fasteners, screws, and coatings, ensuring your projects excel in performance, precision, and quality.
Contact us for a free quote of your ideal custom Cnc Machined Parts.