Rolled Screw Threads VS Cut Screw Threads
When it comes to screw threads, there are two methods commonly used: rolling and cutting.
Rolled screw threads involve the process of forming the threads by displacing the material, while cut screw threads are created by removing the material through cutting.
Both methods have their advantages and disadvantages, raising the question of which is better.
In this discussion, we will explore the differences between rolled and cut screw threads, their respective applications, and the factors to consider when choosing between them.
By the end, you will have a clearer understanding of the topic and be equipped with the knowledge to make informed decisions in the realm of screw threads.
Key Takeaways
- Rolled threads are formed by displacing the material, while cut threads are created by removing the material through cutting.
- Rolled threads have higher strength compared to those with cut threads, especially in non-heat-treated bolts.
- Rolled threads with a rounded root radius improve fatigue resistance, while cut threads can be made with a rounded root equivalent to a rolled thread.
- Rolled threads offer cost-effectiveness, shorter labor times, and better fatigue life, and are commonly used in the automotive industry for head bolts.
1. What Is the Difference Between a Screw with Rolled Threads and One with Cut Threads?
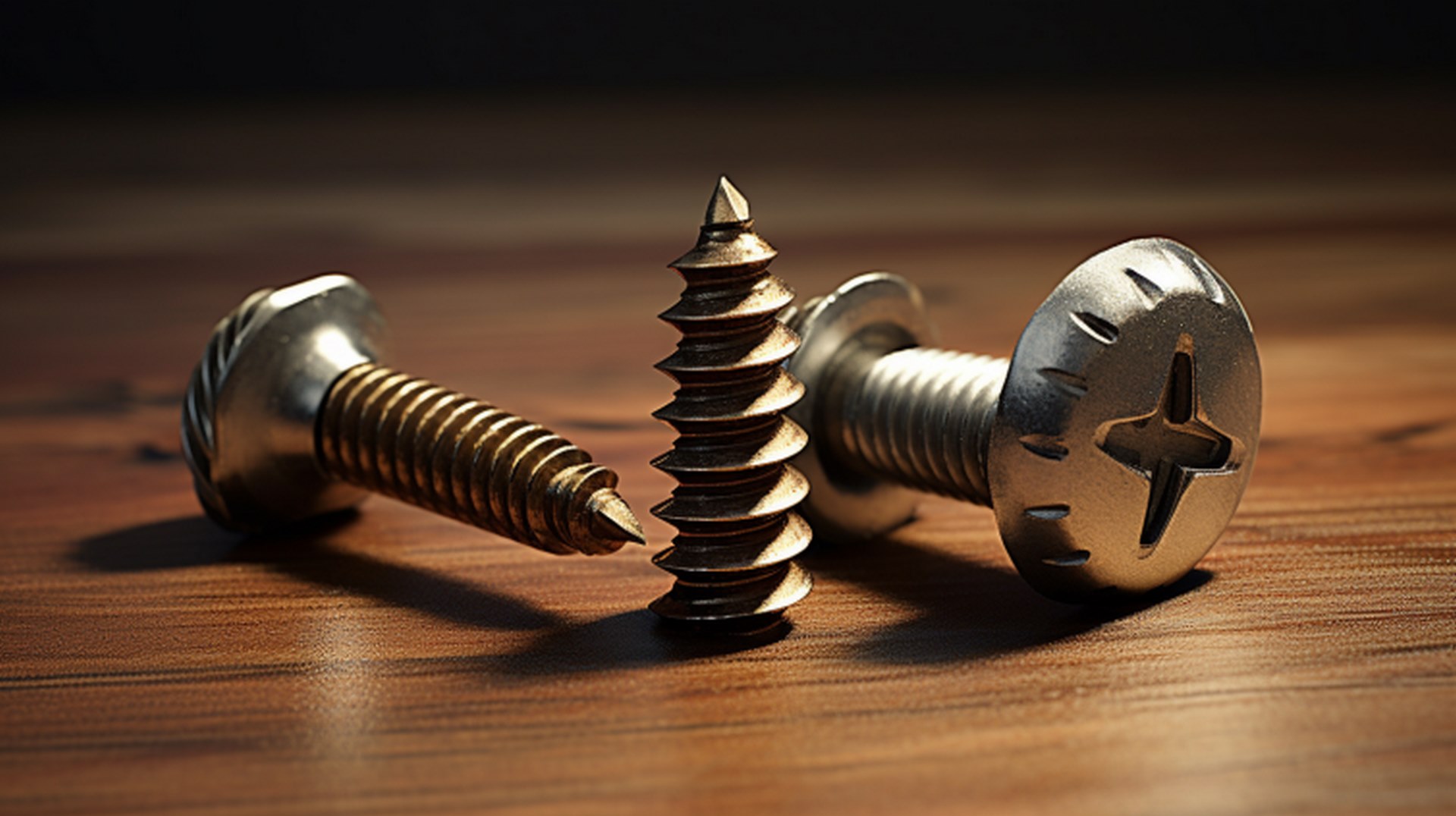
The difference between a screw with rolled threads and one with cut threads lies in the method used to form the threads on the steel. When it comes to strength comparison, non-heat-treated bolts with rolled threads have higher strength than those with cut threads. However, heat-treated bolts with cut or rolled threads have the same strength based on the hardness of the part.
In terms of fatigue resistance, the form at the bottom (root) of the thread plays a role. Rolled threads with a rounded root radius improve fatigue resistance. Cut threads, on the other hand, can be made with a rounded root equivalent to a rolled thread.
When it comes to cost-effectiveness, rolling threads are more cost-effective for high-volume operations, while cutting threads are more cost-effective for low-volume applications. Earnest standard products have rolled threads before heat treatment, while special products have cut threads with rounded root forms for fatigue resistance.
The best thread form, however, is rolling threads after heat treatment with a large root radius.
2. Does a Fastener with a Reduced Body and Rolled Threads Meet Astm Specifications?

A fastener with a reduced body and rolled threads can meet ASTM specifications, except for A325 and A490 structural bolts. The method of roll threading provides several advantages in terms of cost-effectiveness and strength. Rolled threads offer shorter labor times, resulting in lower costs. The reduced weight of roll-threaded bolts leads to cost savings for material, galvanizing, heat-treating, plating, and freight. The cold working process during roll threading also makes the threads more resistant to damage during handling.
Moreover, rolled threads have documented fatigue life that is better than cut threads, making them stronger and more durable. Rolled threads are commonly used in the automotive industry for head bolts due to their superior fatigue life in tension applications. Roll threading work hardens the threads, resulting in a slightly stronger thread compared to cut threads that cut into the grain of the material. However, it is important to note that rolled threads do not provide any additional strength for bolt shear or bending.
3. What Is a Thread Rolling Screw?

A thread-rolling screw is a type of self-tapping screw that does not require a pre-tapped hole. It forms its threads by displacing the material, utilizing a coarse pitch and a standard machine screw thread form.
In the upcoming discussion, we will provide an overview of rolled threads, dispel any misconceptions, highlight the key characteristics of thread rolling screws, and explore the pros and cons of using this type of screw.
3.1 Overview of Rolled Threads
Rolled threads, also known as thread rolling screws, are a highly efficient and cost-effective method of creating threads in metal or plastic materials. They offer several benefits in manufacturing, including:
- Enhanced strength: Rolled threads have greater tensile strength compared to cut threads, making them ideal for applications that require high load-bearing capacity.
- Improved thread quality: The rolling process produces threads with precise dimensions, smooth surfaces, and reduced stress concentrations, ensuring better fit and functionality.
- Increased production speed: Thread rolling screws can be produced at a faster rate compared to other threading methods, resulting in higher productivity and reduced manufacturing costs.
These advantages have led to the widespread application of rolled threads in various industries, such as automotive, aerospace, and construction. They are commonly used in fasteners, threaded inserts, and components requiring secure and durable threading.
When comparing rolled threads with other threading methods like cutting or grinding, the rolling process offers superior thread integrity, increased fatigue resistance, and improved thread finish. Additionally, the material savings achieved through the rolling process further contribute to its cost-effectiveness.
3.2 Roll Threading Misconceptions
Thread rolling screws, also known as thread-forming screws, are commonly misunderstood in terms of their purpose and function. There are several common misconceptions about roll threading that need to be addressed.
One misconception is that roll threading is weaker than cut threading. However, this is not true as roll threading work hardens the threads, making them slightly stronger than their cut-thread counterparts.
Another misconception is that roll threading is not suitable for all applications. While it is true that there are factors to consider when choosing between rolled and cut threads, such as thread length and diameter limitations, roll threading can still provide significant cost savings and has been proven to have better fatigue life in tension applications.
It is important to understand the impact of thread type on the performance of threaded fasteners and not rely on misconceptions when making decisions.
3.3 Key Characteristics of Thread Rolling Screws
Thread rolling screws possess specific characteristics that make them indispensable in certain applications. Here are some key characteristics of thread-rolling screws:
- Thread rolling does not affect screw strength. In fact, it can improve the strength of the screw by increasing its fatigue resistance.
- Thread rolling screws are suitable for a wide range of materials, including ductile metals like steel and aluminum. However, they are not ideal for brittle materials such as cast iron.
- The main applications of thread rolling screws include the automotive, aerospace, and electronics industries. They are commonly used in assembly lines, where high torque and reliability are required.
With their ability to create strong and precise threads, thread rolling screws offer numerous advantages in various industries. Their durability, versatility, and efficiency make them a popular choice for many applications.
3.4 Pros and Cons of Rolled Threads
When considering the pros and cons of rolled threads, it is important to examine the advantages and disadvantages of this threading method.
The advantages of roll threading include shorter labor times, reduced weight, increased resistance to damage, and smoother threads.
However, there are also limitations to roll threading, such as size restrictions and material strength requirements.
Advantages of Roll Threading
Roll threading offers several advantages over other methods of creating screw threads. These advantages include:
- Increased strength and durability of the thread due to the compression and work hardening of the material.
- Improved resistance to fatigue and wear, making roll-threaded screws ideal for high-stress applications.
- Cost-effectiveness in comparison to cut threading, as roll threading can be performed at a faster rate and with less material waste.
Disadvantages of Roll Threading
One drawback of roll threading is that it may result in a slightly higher initial cost compared to other methods of creating screw threads.
Additionally, roll threading has a limited thread size range, which means that it may not be suitable for all applications.
Another disadvantage is that roll threading can lead to reduced strength in the threaded area compared to other methods.
Lastly, there is a potential for thread damage during the roll threading process.
4. What Is a Screw with Cut Threads?

A screw with cut threads refers to a type of screw that has threads that are formed by cutting or removing material from the screw. This method involves using a cutting tool to create the threads on the screw's surface.
In the upcoming discussion, we will provide an overview of cut threads, explore their pros and cons, discuss the advantages they offer, and also highlight any disadvantages associated with cut threading.
4.1 Overview of Cut Threads
Cut threads are a common type of screw threads that are produced through a machining process. They are widely used in various applications due to their strength and durability.
Here are some key points to consider about cut threads:
- Applications of cut threads:
- Cut threads are commonly used in industries such as automotive, aerospace, and construction.
- They are suitable for heavy-duty applications that require high load-bearing capacity.
- Cut threads are also used in precision instruments and machinery where accuracy is crucial.
- Common materials used for cut threads:
- Cut threads can be made from a wide range of materials including steel, stainless steel, brass, and aluminum.
- The choice of material depends on the specific application and the desired properties such as strength, corrosion resistance, and conductivity.
- Factors affecting the quality of cut threads:
- The quality of cut threads is influenced by factors such as the cutting tool geometry, cutting speed, feed rate, and the type of material being threaded.
- Proper lubrication and cooling during the cutting process also play a significant role in achieving high-quality cut threads.
4.2 Pros and Cons of Cut Threads
Screw threads produced through a machining process, known as cut threads, offer a variety of advantages and disadvantages in different applications.
One of the advantages of cut threading is the ability to create threads with high precision and accuracy. Cut threads also have a higher tensile strength compared to rolled threads, making them more suitable for applications that require heavy loads or strong connections. Additionally, cut threads allow for better control over thread depth and pitch, resulting in a tighter fit and improved thread engagement.
However, there are also challenges with cut threading. It requires specialized equipment and skilled operators, making the process more time-consuming and expensive. In comparison, thread rolling is a faster and more cost-effective method, but it may not achieve the same level of precision as cut threading.
Ultimately, the choice between cut threads and rolled threads depends on the specific requirements and constraints of the application.
4.3 Advantages of Cut Threading
The process of cut threading offers several advantages for screw threads in various applications. These advantages include:
- Improved strength: Cut threading results in a stronger screw thread compared to rolled threading. The cutting process removes material from the workpiece, creating a more robust and durable thread that can withstand higher loads and stresses.
- Better thread accuracy: Cut threading provides superior thread accuracy compared to rolled threading. The cutting tool can create threads with precise dimensions, ensuring a perfect fit between the screw and the mating part. This accuracy is crucial in industries where precision is essential, such as aerospace and automotive.
- Increased durability: Cut threads are known for their increased durability. The cutting process removes any imperfections or inconsistencies in the thread, resulting in a smoother and more reliable surface. This enhanced durability makes cut threading suitable for applications that require long-lasting and high-performance screw threads.
These advantages make cut threading a preferred choice in many industries where strength, accuracy, and durability are critical factors in screw thread applications.
4.4 Disadvantages of Cut Threading
One potential drawback of utilizing cut threading for screw threads is its inherent limitations. There are several reasons to avoid cut threading and opt for other methods like rolled threading.
One of the main drawbacks of cut threading is the reduced strength of the screw. When threads are cut into the material, it weakens the overall structure, making it more susceptible to breaking or stripping.
Additionally, cut threading can result in a rougher surface finish compared to rolled threading, which can negatively impact the performance of the screw.
Cut threading also requires more time and effort, as it involves the use of specialized tools and machinery.
Lastly, cut threading is not suitable for certain materials that are prone to deformation or warping.
5. Rolled Screw Threads VS Cut Screw Threads - Which Is Better?
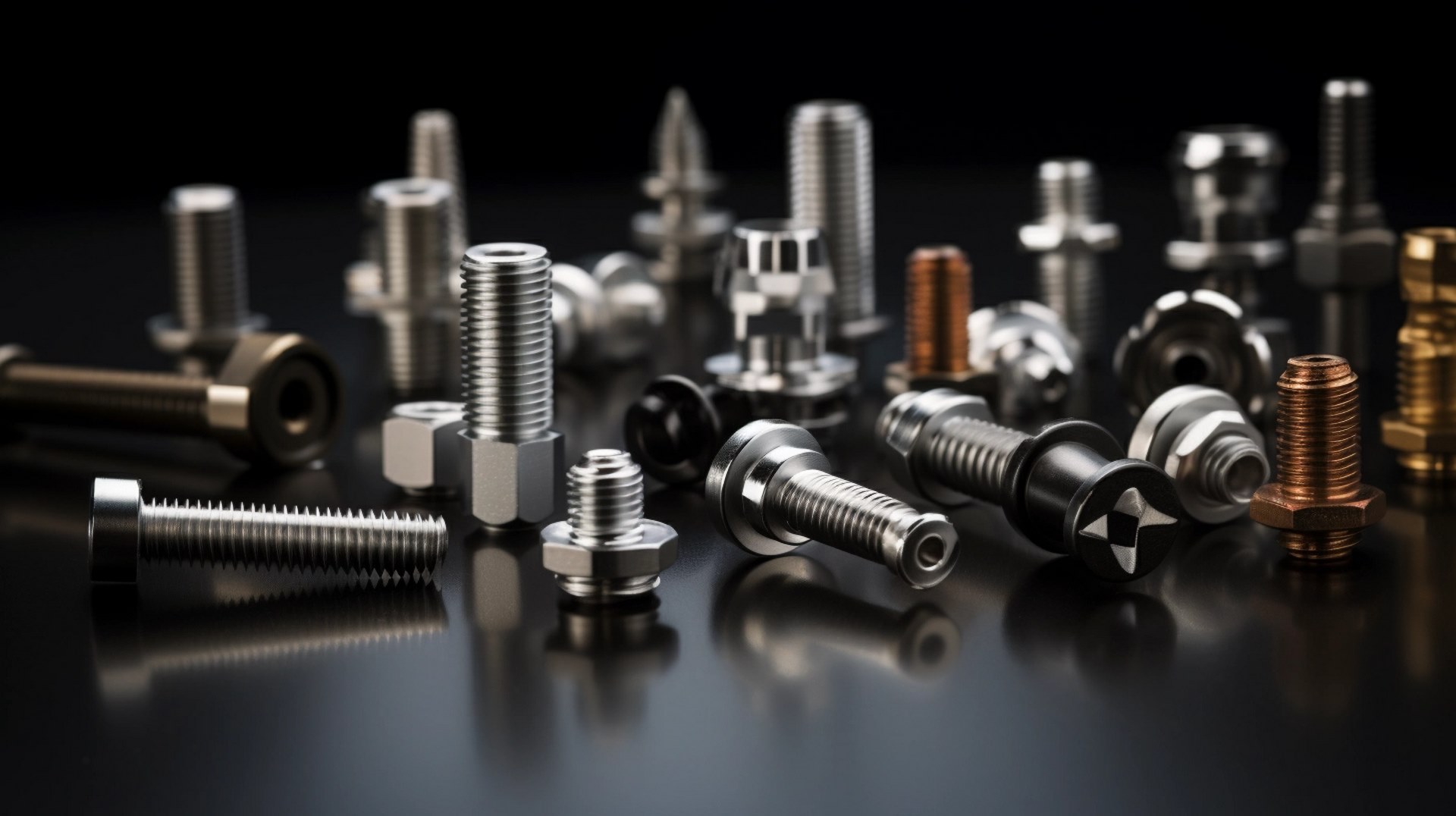
When it comes to comparing rolled screw threads and cut screw threads, the question of which is better arises.
There are several factors to consider, such as strength, installation process, resistance to damage, and cost advantages.
5.1 Why Rolled Threads?
Rolled threads offer numerous advantages over cut threads, making them the preferred choice in various industries.
The difference between rolled and cut threads lies in their strength, durability, and production efficiency.
A comparison reveals that rolled threads have a finer surface finish, higher rates of production, and lower material costs.
Additionally, the grain structure in rolled threads is not severed, leading to increased resistance to stripping failures and fatigue failure.
The fatigue strength of rolled threads is improved by 50-75% due to factors such as burnished roots and flanks, minimized surface imperfections, and compressive stresses in the thread.
Industries such as automotive, aerospace, and construction greatly benefit from the use of rolled threads due to their superior strength and durability.
Frequently Asked Questions
How Are Rolled Screw Threads and Cut Screw Threads Manufactured?
The manufacturing process comparison between rolled screw threads and cut screw threads involves distinct methods. Rolled threads are formed by compressing and shaping the material, resulting in higher quality and strength. Cut threads, on the other hand, are produced by removing material, making them less durable. Additionally, rolled threads tend to be more cost-effective compared to cut threads.
What Are the Advantages of Using a Screw With Rolled Threads Over One With Cut Threads?
The advantages of using a screw with rolled threads over one with cut threads include increased strength, improved thread quality, and enhanced resistance to fatigue. This manufacturing difference makes rolled threads suitable for applications requiring high precision and durability.
Are There Any Disadvantages to Using a Screw With Rolled Threads Instead of Cut Threads?
When comparing rolled and cut screw threads, it is important to consider the potential disadvantages of using rolled threads. Factors such as reduced thread strength and limited application suitability should be taken into account when choosing the appropriate screw thread type.
Can a Screw With Rolled Threads Be Used in Applications Where a Screw With Cut Threads Is Typically Used?
When considering the compatibility and interchangeability of rolled and cut threads in various applications, it is important to assess the performance and durability comparison, as well as the cost-effectiveness and efficiency of each option.
Are There Any Specific Industries or Applications Where One Type of Screw Thread Is Preferred Over the Other?
In various industries and applications, the preference for either rolled or cut screw threads depends on factors such as comparative performance in the automotive industry, cost-effectiveness in construction applications, and precision requirements in aerospace engineering.
Mikehardware-your trusted custom screws manufacturer
In conclusion, the difference between a screw with rolled threads and one with cut threads lies in their manufacturing processes. Rolled threads are formed by pressing the material, resulting in improved strength and durability. On the other hand, cut threads are created by removing material, which may weaken the screw.
While both types meet ASTM specifications, it is essential to consider the specific application and requirements when deciding between rolled and cut screw threads.
So, which type of screw thread would you choose for your project?
At Dongguan Mike Hardware Co., Ltd., precision engineering meets innovation, delivering impeccable CNC product manufacturing solutions. Explore our array of customized fasteners, screws, and coatings, ensuring your projects excel in performance, precision, and quality.
Elevate your engineering prowess with our tailored solutions—partner with us at Dongguan Mike Hardware Co., Ltd. for the pinnacle of custom screws excellence.