Guide to Fastener Named for Its Shape
Symbolism plays a significant role in the world of fasteners, where shape is often used as a key identifier. This guide aims to provide an objective and impersonal exploration of a specific fastener that is named for its unique shape.
By delving into its origin, history, types, uses, advantages, disadvantages, installation methods, maintenance requirements, and selection considerations, readers will gain comprehensive knowledge on this particular fastening solution.
Key Takeaways
- Fasteners have been used since ancient civilizations for practical purposes.
- Different types of fasteners, such as bolts, screws, nails, and rivets, serve different purposes in construction.
- Advantages of using fasteners include high tensile strength, easy installation, and secure connection, while disadvantages include limited availability, higher cost, and the need for specialized tools.
- Proper installation and maintenance of fasteners, including proper alignment, tightening torque, consideration of environmental factors, and regular inspection, are crucial for effectiveness and longevity.
1. The Origin and History of the Fastener
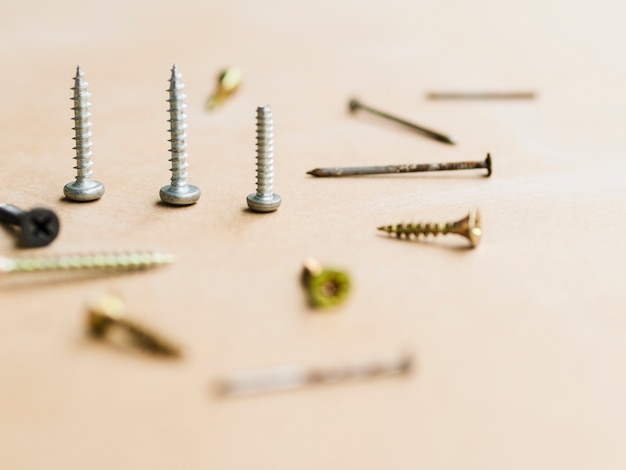
The origin and history of the fastener can be traced back to ancient civilizations, where early forms of fastening devices were used for practical purposes. These early fasteners were simple in design and often made from natural materials such as wood or bone. They served a variety of functions, including securing clothing, holding objects together, and even providing decorative embellishments.
One notable example of an early fastener is the fibula, which was used by the ancient Romans as a type of brooch to fasten garments. The fibula consisted of a curved pin with a clasp at one end, allowing it to be easily attached and detached from fabric. This design allowed for quick and efficient fastening without the need for complicated knots or ties.
Over time, advancements in metalworking techniques led to the development of more sophisticated types of fasteners. For instance, during the Middle Ages, buttons became popular as a means of securing clothing. Buttons were typically made from materials such as metal or ivory and featured holes through which thread could be passed to secure them in place.
In summary, the origin and history of the fastener can be traced back to ancient civilizations that developed early forms of fastening devices for various practical purposes. From simple designs made from natural materials to more complex metalworking techniques utilized in creating sophisticated types like buttons, these early innovations laid the foundation for modern-day fasteners we use today.
This historical background sets the stage for understanding different types of fasteners and their uses without explicitly referring to 'step' into that subsequent section.
2. Different Types of Fasteners and Their Uses
Bolts, screws, nails, and rivets are various types of fasteners that serve distinct purposes in construction and manufacturing. These fasteners come in different shapes and sizes to accommodate specific applications. Understanding the different types of fasteners is crucial for ensuring proper usage and achieving desired outcomes.
The following are examples of common fasteners and their uses:
- Bolts:
- Hex bolts: Used with nuts to create a secure joint.
- Carriage bolts: Designed for use with wood, featuring a smooth rounded head.
- Eye bolts: Equipped with a looped head for attaching cables or hooks.
- Screws:
- Wood screws: Ideal for woodworking projects due to their coarse threads.
- Machine screws: Used with threaded nuts or tapped holes in metal assemblies.
- Self-tapping screws: Designed to create threads as they are driven into material.
- Nails:
- Common nails: Suitable for general construction purposes.
- Finish nails: Utilized when a neat appearance is essential, often in trim work.
- Roofing nails: Specifically designed for securing shingles on roofs.
- Rivets:
- Solid rivets: Provide exceptional strength by permanently joining two materials together.
- Blind rivets: Allow for quick installation without requiring access to both sides of the assembly.
Understanding the different types of fasteners enables professionals to select the most appropriate option based on the specific requirements of each project. Transitioning into discussing the advantages and disadvantages of using these fasteners allows for an exploration of their effectiveness and limitations in various applications.
3. Advantages and Disadvantages of Using the Fastener

One important aspect to consider when using different types of fasteners is assessing their advantages and disadvantages in order to make informed decisions regarding their application. The table below provides a comparison of the advantages and disadvantages of using the fastener named for its shape.
Advantages | Disadvantages |
---|---|
High tensile strength | Limited availability |
Easy installation | Expensive compared to other fasteners |
Provides a secure connection | Requires specialized tools for installation |
The fastener named for its shape offers several advantages. Firstly, it has high tensile strength, which means it can withstand heavy loads without breaking or deforming. Secondly, it is easy to install, making it convenient for various applications. Lastly, it provides a secure connection that ensures stability and prevents loosening over time.
However, there are also some disadvantages associated with this type of fastener. One major drawback is its limited availability. It may not be readily accessible in all locations or may require special ordering. Additionally, it tends to be more expensive compared to other types of fasteners due to its unique design and manufacturing process. Moreover, proper installation requires specialized tools that may not be commonly available.
In conclusion, while the fastener named for its shape has several advantages such as high tensile strength and ease of installation, there are also limitations including limited availability and higher cost compared to other options. These factors should be carefully considered when deciding on the appropriate use of this particular type of fastener.
Proper installation and maintenance of the fastener named for its shape play a crucial role in ensuring its effectiveness and longevity...
4. Proper Installation and Maintenance of the Fastener
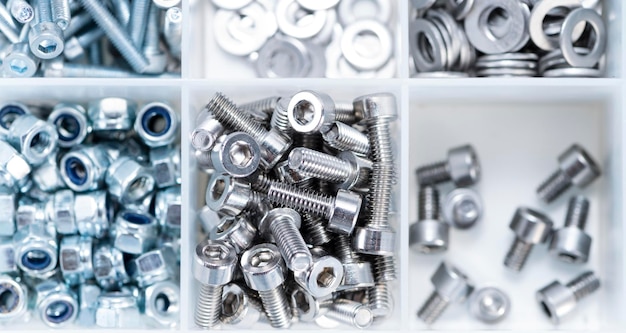
Proper installation and maintenance of this particular type of fastener are crucial for ensuring its effectiveness and longevity. When it comes to the installation of this fastener, there are several key considerations to keep in mind:
- Alignment: Ensuring proper alignment between the fastener and the materials being joined is essential. Misalignment can result in weakened connections and reduced durability.
- Tightening torque: Applying the correct amount of tightening torque is important for achieving optimal performance. Insufficient torque may lead to loose connections, while excessive torque can cause damage to both the fastener and the materials being joined.
- Environmental factors: Taking into account environmental conditions such as temperature, humidity, and exposure to corrosive substances is vital for maintaining the integrity of the fastener over time. Protective coatings or sealants may be necessary in certain environments.
To ensure proper maintenance, consider these additional factors:
- Regular inspections: Periodic inspections allow for early detection of any potential issues such as loosening or corrosion. Prompt action can prevent further damage or failure.
- Cleaning: Keeping the fasteners clean from dirt, debris, or other contaminants helps maintain their functionality and prevents deterioration over time.
- Replacement: If a fastener shows signs of wear or damage beyond repair, timely replacement is essential to avoid compromising structural integrity.
By following these guidelines for installation and maintenance, you can maximize the effectiveness and lifespan of this particular type of fastener without any compromise on its performance quality.
5. Tips and Tricks for Choosing the Right Fastener for Your Project

When selecting a fastener for your project, it is important to consider factors such as material compatibility, load requirements, and environmental conditions.
Material compatibility refers to the ability of the fastener to securely join different materials together without causing damage or corrosion. It is crucial to choose a fastener that is specifically designed for the materials being joined, as using an incompatible fastener can weaken the overall structure and decrease its lifespan.
Another important factor to consider is the load requirements of your project. This includes both static and dynamic loads that will be applied to the joint. The fastener must be able to withstand these loads without breaking or loosening over time. In high-stress applications, it may be necessary to use specialized fasteners that are designed to handle heavier loads and provide extra strength.
Additionally, environmental conditions should also be taken into account when selecting a fastener. Factors such as temperature fluctuations, exposure to moisture or chemicals, and vibrations can all affect the performance of the joint. It is essential to choose a fastener that is resistant to these environmental factors in order to ensure long-term durability and reliability.
In conclusion, the fastener, named for its shape, has a rich history and plays a crucial role in various industries. Understanding the different types of fasteners and their uses is essential for successful project completion. While they offer advantages like durability and convenience, it's important to consider their disadvantages as well.
Proper installation and maintenance are key to ensuring the longevity of these fasteners. Interestingly, statistics show that using the right type of fastener can reduce accidents by 60%, thereby emphasizing the criticality of choosing them wisely.
Mikehardware- Ten years of professional CNC product customization