What Are Fastener Types and Applications
Fasteners play a vital role in various industries, serving as essential components for joining and securing objects together. This article aims to provide an objective and impersonal exploration of fastener types and applications, shedding light on their diverse functions in different contexts.
By understanding the characteristics of bolts, screws, rivets, pins, nuts, washers, and their respective uses, readers will gain valuable insights into the intricate world of fasteners.
Delving into this subject matter will allow individuals to appreciate the significance of these seemingly small but crucial elements in everyday life.
Key Takeaways
- There are various types of fasteners, including screws, bolts, rivets, nails, and clips, each with their own specific applications.
- Bolt and screw fasteners are commonly used for joining purposes and it is important to understand their appropriate size, dimensions, thread type, head type, material strength, corrosion resistance, and proper tightening torque for installation.
- Rivets and pins provide exceptional strength and are commonly used in construction, automotive, and aerospace industries for reliable connections between components.
- Nuts and washers are essential for proper bolted joint assembly, with nuts used in conjunction with bolts to secure objects together and washers used to distribute load and prevent damage to surfaces. They have various types and are used in different industries such as automotive, construction, machinery, plumbing, piping, aerospace, manufacturing, and furniture.
1. Different Types of Fasteners
Various types of fasteners, such as screws, bolts, and rivets, are commonly used in a wide range of applications. Each type has its unique characteristics and is designed to fulfill specific requirements.
Screws are threaded fasteners with a helical ridge that allows them to be rotated into materials for joining purposes. They come in various head shapes, including flathead, roundhead, and panhead.
Bolts, on the other hand, are externally threaded fasteners that require a nut to secure two or more objects together. They also come in different configurations such as hex bolts, carriage bolts, and eye bolts.
Rivets are permanent mechanical fasteners that consist of a cylindrical shaft with a head at one end. They are commonly used when welding or screwing is not feasible or desired. Rivets work by deforming the shaft to create a secondary head on the opposite side of the material being joined.
Other types of fasteners include nails for woodwork applications and clips for securing objects temporarily without permanent attachment. These fasteners can be made from various materials like steel, stainless steel, aluminum alloy, or plastic depending on the application requirements.
Understanding the different types of fasteners is essential in selecting the appropriate one for specific applications based on factors such as load-bearing capacity, corrosion resistance, ease of installation/removal and aesthetics.
2. Common Applications for Fasteners
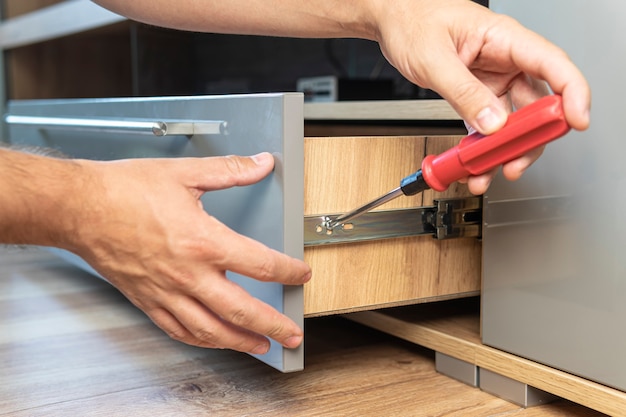
Common uses of fasteners can be observed in construction, automotive manufacturing, and appliance assembly.
Fasteners are essential components used to join or secure two or more objects together. In the construction industry, fasteners such as bolts, screws, and nails are widely utilized to connect structural elements like beams and columns, ensuring stability and strength of the overall structure.
Similarly, in automotive manufacturing, fasteners play a crucial role in assembling various parts of vehicles, including engines, chassis components, and body panels. Fasteners used in this sector must meet stringent requirements for strength and reliability due to the demanding operating conditions experienced by automobiles.
Appliance assembly is another area where fasteners find extensive application. These small yet vital components are used to assemble household appliances such as refrigerators, washing machines, and air conditioners. Fasteners ensure that all parts of these appliances are securely held together during operation while withstanding vibrations and other stresses.
Understanding bolt and screw fasteners is important as they are among the most commonly used types in various applications. By comprehending their design principles, materials selection criteria, installation techniques, and performance characteristics under different loading conditions one can effectively utilize them for joining purposes across industries without compromising safety or efficiency.
3. What are Bolt and Screw Fasteners
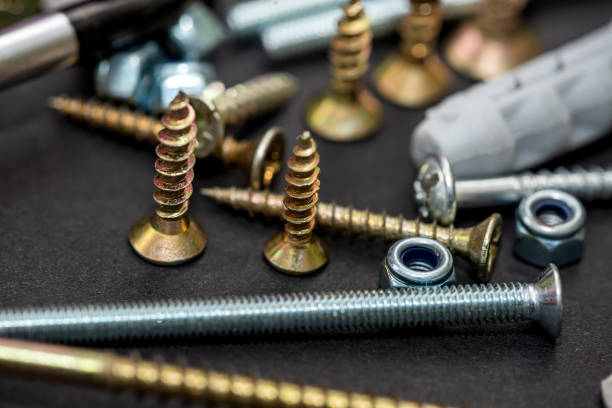
Bolt and screw fasteners play a significant role in joining various components together across industries, requiring an understanding of their design principles, materials selection criteria, installation techniques, and performance characteristics.
Design Principles:
- Fastener size and dimensions must be appropriate for the application to ensure proper fit and strength.
- Thread type (such as coarse or fine) affects the ease of assembly and resistance to loosening.
- Head type (e.g., hexagon, flat) determines the tool required for installation and aesthetic considerations.
Materials Selection Criteria:
- Fastener materials must have sufficient strength, corrosion resistance, temperature resistance, and compatibility with joined components.
- Common materials include carbon steel, stainless steel, aluminum alloy, brass, and titanium.
Installation Techniques:
- Proper tightening torque is crucial to prevent fastener failure due to overloading or loosening.
- Various methods such as hand tools (wrenches), power tools (impact wrenches), or torque measuring devices are used for installation.
Performance Characteristics:
- Fasteners should withstand static loads without permanent deformation or failure.
- Factors like fatigue strength under cyclic loading conditions need consideration for long-term performance.
Understanding the principles of bolt and screw fasteners provides a solid foundation for exploring other types of mechanical fasteners such as rivets and pins.
4. Exploring Rivets and Pins
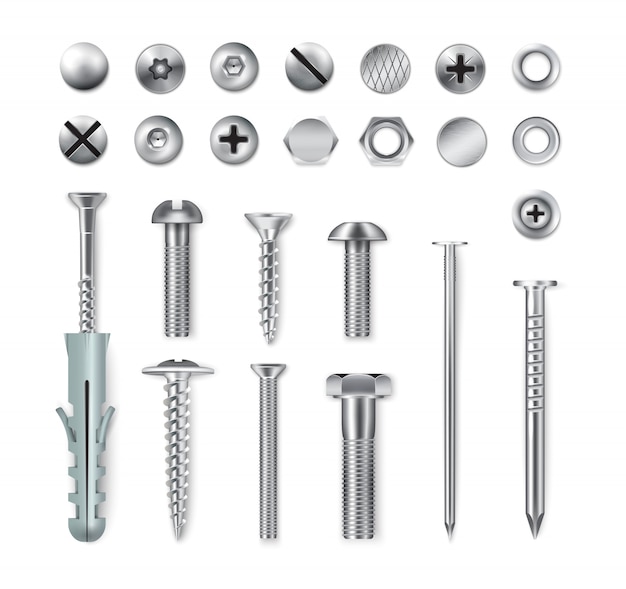
Rivets and pins are alternative mechanical fasteners that offer unique joining capabilities and have distinct design features.
Rivets are cylindrical metal shafts with a head on one end and a tail on the other, which is deformed during installation to secure two or more materials together. They provide exceptional strength and resistance to vibration due to their permanent nature. Rivets are commonly used in applications where disassembly is not required or desired, such as in construction, automotive, and aerospace industries.
Pins, on the other hand, are slender cylindrical objects that can be inserted into holes or grooves of mating components for alignment or retention purposes. They come in various shapes and sizes, including dowel pins, taper pins, and split pins. Pins can be easily installed and removed when necessary without damaging the joined materials.
Both rivets and pins play crucial roles in mechanical assemblies by providing reliable connections between components. Their versatility allows for efficient assembly processes while ensuring structural integrity.
Moving forward to nuts, washers, and their uses...
5. Nuts, Washers, and Their Uses
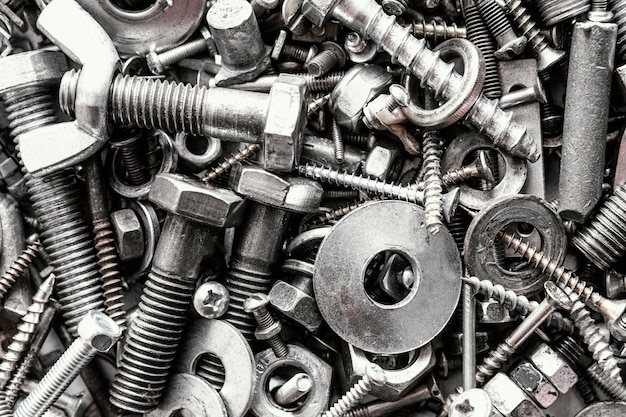
Nuts and washers are essential components in mechanical assemblies, serving to secure bolts and provide additional support and stability to the joint. Nuts are threaded fasteners that are typically hexagonal in shape, designed to be used with bolts or screws. They come in various sizes and materials, such as steel, stainless steel, or brass. Washers, on the other hand, are flat metal discs with a hole in the center. They can be used alongside nuts or directly under bolt heads to distribute the load and prevent damage to the surface being fastened.
The uses of nuts and washers extend beyond their basic functions. Here are three sub-lists showcasing their diverse applications:
- Types of Nuts:
- Hex nuts: These common nuts have six sides and are widely used for general applications.
- Locknuts: Designed with a locking feature like nylon inserts or distorted threads, they prevent unintentional loosening.
- Wing nuts: With two large wings protruding from the head, they allow for easy hand-tightening without requiring tools.
- Washer Applications:
- Spring washers: These washers have a curved design that provides tension against loosening due to vibrations.
- Flat washers: Used to distribute loads over a larger area and protect surfaces from damage caused by tightening forces.
- Belleville washers: Also known as conical spring washers, they provide high spring force while occupying minimum space.
- Specialized Uses:
- Jam nuts: Thin hexagonal nuts used in conjunction with standard nuts to lock them into place.
- Acorn nuts: Dome-shaped decorative caps that cover exposed bolt ends for aesthetic purposes.
- T-nuts: Used primarily in woodworking applications where a flush surface is desired on one side of the assembly.
In conclusion, the vast array of fasteners available serve a crucial role in various applications. From bolts and screws to rivets and pins, each type plays a unique part in holding things together.
Nuts and washers add an extra layer of stability. Although seemingly small and insignificant, these fasteners are the unsung heroes that keep our world intact.
So next time you come across a fastener, take a moment to appreciate its understated importance in maintaining the structural integrity of our surroundings.
Mikehardware- Ten years of professional CNC product customization