Custom Fasteners: Your Comprehensive Guide to Materials, Types, and Applications
In the realm of mechanical and industrial engineering, the selection and application of fasteners, particularly custom ones, is a pivotal factor that can decisively impact the functionality and efficiency of the final product. From airplanes to automobiles, buildings to bridges, the structural integrity of these vast creations often hinges upon these seemingly insignificant components.
This comprehensive guide will offer an in-depth exploration into the diverse world of custom fasteners, examining the different materials, types and their respective applications. With this knowledge, you will gain the proficiency needed to make informed decisions about which custom fasteners best suit your specific requirements and the potential impact on your projects.
Let us embark on this informative journey to unravel the complexities of these essential elements.
Key Takeaways
- Custom fasteners offer tailored solutions for specific project requirements, enhancing functionality, longevity, and potential cost savings.
- Materials for custom fasteners range from alloy steel to plastic, providing options for factors like corrosion resistance, strength properties, and cost considerations.
- Machining capabilities and custom fastener design are crucial for meeting industry-specific needs and ensuring efficient production.
- Selection of custom fasteners involves considering material strength, compatibility, corrosion resistance, cost-effectiveness, and security requirements for specific applications.
1. What are Custom Fasteners?
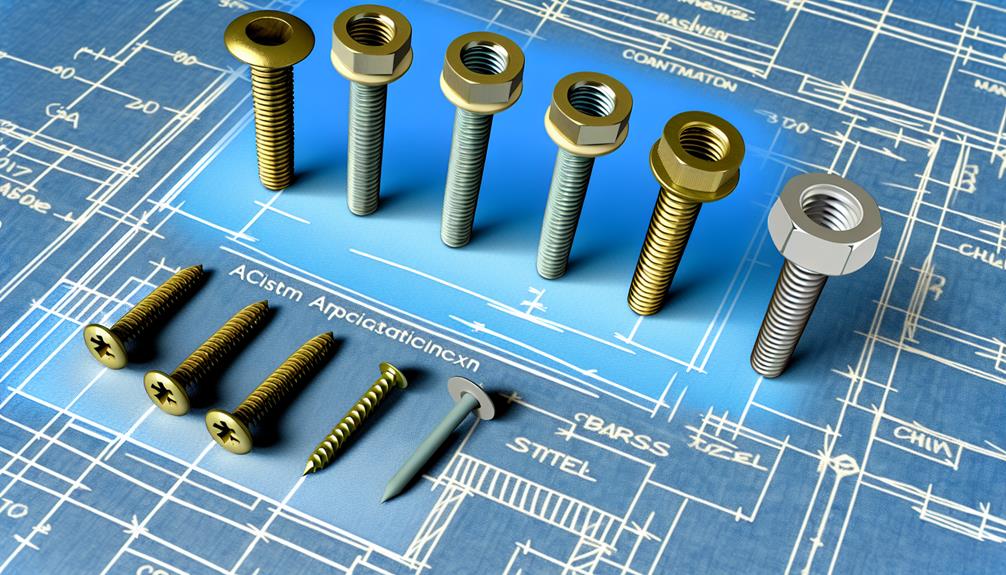
Custom fasteners, a critical component in various industries, are specialized hardware devices specifically designed and manufactured according to a customer's particular specifications and needs. These fasteners, marked by their durability, can withstand various physical conditions, ensuring longevity and reliability of the fastened products. The customization process allows clients to take charge of the design, material, shape, and size, aligning the fasteners with the specific requirements of their project.
Fastener efficiency is a crucial element; custom fasteners are designed to perform specific functions optimally, enhancing overall operational efficiency. They are also known for their aesthetics; being customized, they can be designed to blend seamlessly with the product, contributing to an improved visual appeal.
However, the customization of fasteners comes with cost implications. Although they might be relatively more expensive than standard fasteners, their benefits—durability, efficiency, aesthetics—justify the cost. They can lead to cost savings in the long run by reducing the frequency of replacements and repairs. In sum, custom fasteners offer a balance of functionality, appearance, and cost-effectiveness that standard fasteners often can't match.
2. What are Standard Fasteners?
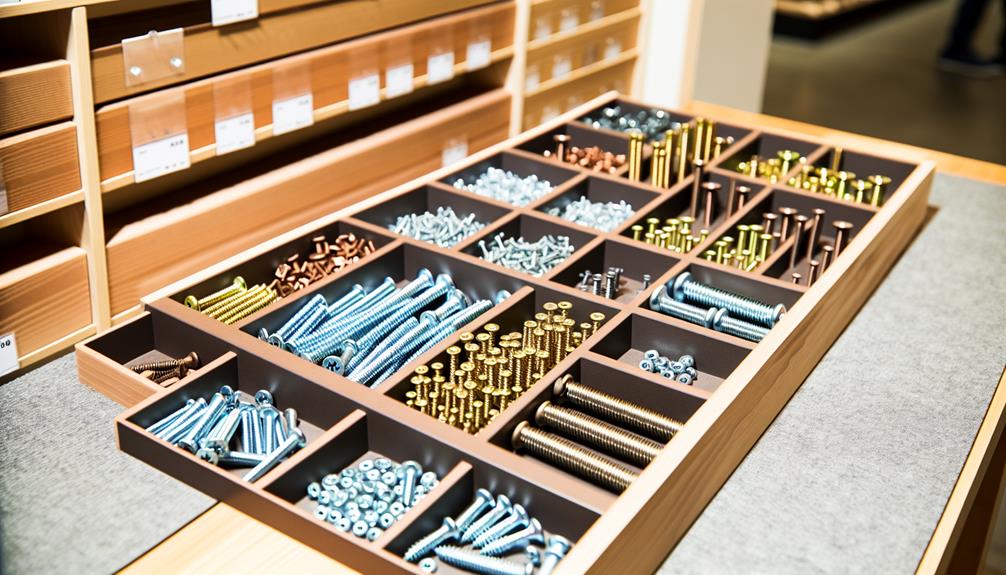
In contrast to custom fasteners, standard fasteners are mass-produced hardware devices that are readily available in various shapes, sizes, and materials, designed to meet general rather than specific requirements. They offer a multitude of options for users seeking a cost-effective solution, while also delivering commendable fastener durability.
Standard fasteners simplify the installation process due to their uniformity, thus offering efficient installation techniques. This uniformity also eases fastener maintenance as replacements can be swiftly sourced and installed without the need for custom ordering.
When considering a cost comparison, standard fasteners often edge out their custom counterparts due to economies of scale in production. However, it's crucial to evaluate the trade-off between cost and the need for specialized performance or fit.
Lastly, the environmental impact of standard fasteners is typically lower than that of custom ones. Production processes are optimized for efficiency and waste reduction, while the ability to recycle or reuse standard fasteners due to their commonality further reduces their environmental footprint.
3. Applications of Custom Fasteners
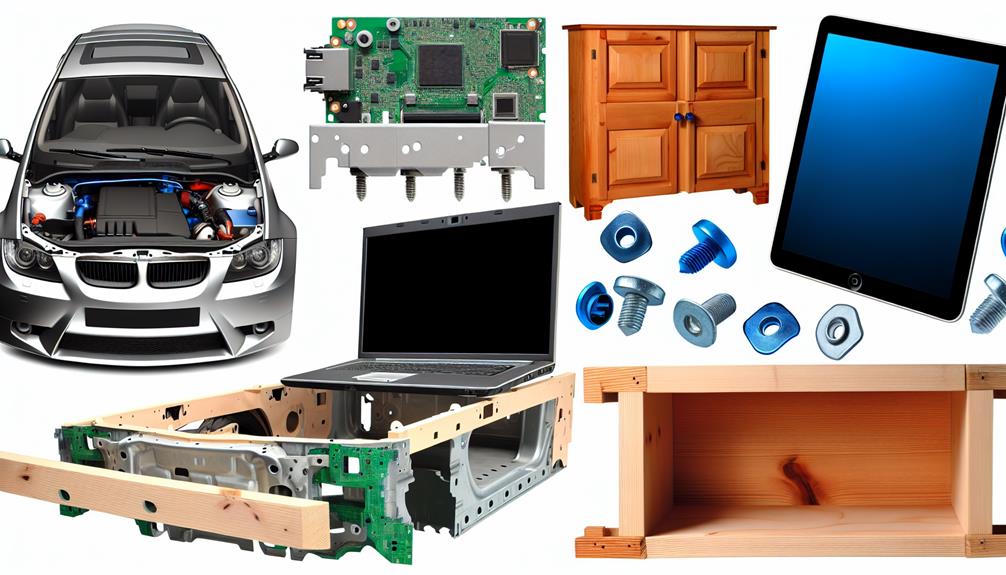
Custom fasteners offer unique advantages in a wide range of applications thanks to their specialized designs and precise specifications. Tapping screws, for example, are commonly used in light metals and plastics due to their excellent fit and durable performance. Automotive assemblies and low-volume engineered projects also benefit from custom fasteners tailored to meet their exact needs.
These fasteners play a crucial role in ensuring the integrity and efficiency of various structures and components, making them an indispensable part of many industries.
Tapping Screws for Light Metals and Plastics
What roles do tapping screws play when interacting with light metals and plastics in various applications?
First and foremost, screw strength matters. The screw must be durable enough to penetrate these materials without deformation or breakage.
Secondly, plastic compatibility is crucial. The screw must not compromise the structural integrity of the plastic it's penetrating.
Third on the list are light metal considerations. The screw should be designed in a way that it does not corrode or damage the light metal.
Lastly, screw head types and installation techniques come into play. Different head types suit different applications, and the chosen installation technique must ensure a secure fit without damaging the material.
These aspects make tapping screws an integral part of many applications.
Fasteners for Automotive Assemblies
Building on the principles of screw compatibility and fastener installation techniques, let's consider the specific applications of custom fasteners in the realm of automotive assemblies. Automotive fastener durability is paramount in ensuring the longevity of any vehicle.
The use of corrosion resistant materials in fasteners not only extends their lifespan but also supports sustainable manufacturing processes. These fasteners play a critical role in vehicle safety, providing secure connections that withstand the rigors of daily use and extreme conditions.
It's this emphasis on durability and safety that underscores the importance of precise installation techniques. The right fastener, correctly installed, can significantly contribute to the vehicle's overall performance and safety features, making them indispensable in automotive assemblies.
Low Volume Engineered Fasteners
In the realm of specialized manufacturing, low volume engineered fasteners offer a unique combination of flexibility, precision, and performance, tailored to meet specific application requirements.
- Fastener Durability: These fasteners are designed with durability at the forefront, ensuring longevity even in demanding conditions.
- Production Process: The manufacturing processes are controlled to produce high-quality, precise components, reducing the likelihood of failure.
- Cost Analysis: Although initial costs may be higher, the long-term savings through reduced maintenance and replacement costs make them a smart investment.
- Quality Control & Maintenance Tips: Rigorous quality control measures are implemented throughout the production process. Regular maintenance, aided by provided tips, ensures optimal performance and lifespan.
Therefore, low volume engineered fasteners offer a controlled, effective solution for specialized applications.
4. Custom Fasteners Specifications
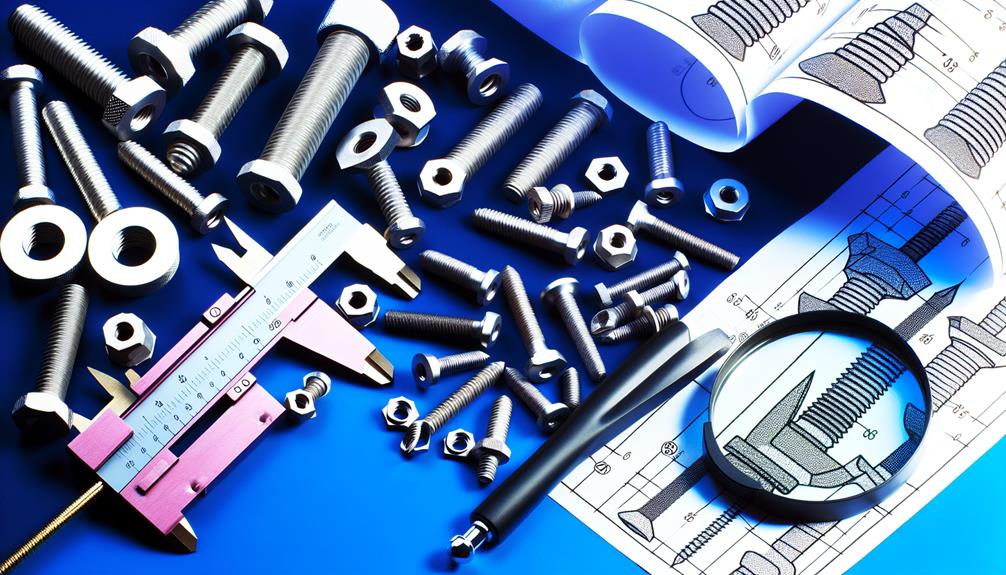
Understanding the specifications of custom fasteners is crucial for optimal performance and safe application. This section will focus on the available materials, types, and sizes of custom fasteners.
Additionally, it will cover typical lead times and finishing services offered. Comprehensive knowledge of these factors will aid in the selection of the most suitable custom fasteners for any given project or task.
4.1 Materials Available
Given the diversity of applications for custom fasteners, a variety of materials such as alloy steel, aluminum, brass, carbon steel, copper alloys, nickel alloys, and specialty materials are available to cater to specific project needs.
Material selection is a critical process that considers several factors:
- Corrosion Resistance: Some materials like brass and nickel alloys provide excellent resistance to corrosion, ensuring durability of the fasteners.
- Strength Properties: Alloy steel and carbon steel are chosen for their high strength and toughness.
- Cost Considerations: Materials like aluminum offer a balance between cost and performance.
- Machining Capabilities: Specialty materials may offer improved machining capabilities, which can enhance production efficiency.
Proper material selection allows for control over the functionality, longevity, and cost-effectiveness of your custom fasteners.
4.2 Custom Fastener Types & Sizes
Custom fasteners come in a wide variety of types and sizes, each designed to meet specific requirements and applications. Understanding the different types available can help you select the right fastener for your project. Here, we delve into the various custom fasteners we offer:
Bolts & Custom Bolts
Bolts are essential for securing components in many industries. Custom bolts are tailored to your specifications, including unique thread patterns, lengths, and head shapes to meet the exact needs of your application.
Bushings
Bushings are used to reduce friction and wear between moving parts. Custom bushings can be fabricated in various materials and dimensions to suit specific applications, ensuring optimal performance and longevity.
Screws
Custom screws are available in a myriad of sizes, thread types, and head designs. Whether you need screws for light metals, plastics, or heavy-duty applications, we can provide the exact specifications required.
Spacers
Spacers are used to create precise distances between components. Custom spacers can be manufactured in various lengths, diameters, and materials to ensure proper fit and function in your assemblies.
Standoffs
Standoffs provide a secure separation between two parts, often used in electronics and construction. Custom standoffs can be designed to your specific requirements, including length, diameter, and threading.
Washers
Washers distribute the load of a fastener and prevent damage to surfaces. Custom washers can be produced in various shapes, sizes, and materials to suit your application needs.
Chassis Fasteners
Chassis fasteners are critical in automotive and machinery applications. We offer custom chassis fasteners designed to withstand high stresses and provide reliable performance in demanding environments.
Hand Screws
Hand screws are fastened by hand and are often used in applications where frequent adjustments are needed. Custom hand screws can be tailored to provide the exact grip and ease of use required.
Handles
Custom handles are designed for ease of use and durability. Whether you need handles for industrial equipment or consumer products, we can create handles that meet your specific needs in terms of size, shape, and material.
Nuts
Nuts secure bolts and screws, providing a tight and reliable fastening solution. Custom nuts can be produced in various shapes, sizes, and materials to match the specific requirements of your bolts and screws.
Threaded Inserts
Threaded inserts are used to add a threaded hole into a softer material. Custom threaded inserts ensure a secure fit and reliable performance in applications requiring strong, durable threads.
Studs
Studs are headless fasteners used in various applications. Custom studs can be manufactured to precise specifications, including threading, length, and material, to meet the exact needs of your project.
Pins
Pins are used to align or secure components. Custom pins can be produced in various diameters, lengths, and materials, ensuring they meet the precise requirements of your application.
Locking Fasteners
Locking fasteners prevent loosening under vibration and stress. Custom locking fasteners can be designed with unique features to ensure they stay secure in challenging environments.
Retainers
Retainers hold components in place and are critical in assemblies. Custom retainers can be fabricated to fit specific shapes and sizes, ensuring they perform effectively in your application.
By offering a wide range of custom fasteners, we can meet the unique demands of various industries and applications. Our ability to produce fasteners to your exact specifications ensures that you get the perfect fit and function for your projects.
4.3 Typical Lead Times
While the types, sizes, and materials of custom fasteners are crucial for optimal application fit, equally significant is the consideration of production lead times for these bespoke specifications.
- Lead Time Reduction - Shorter lead times can increase productivity and reduce idle time, thus boosting production efficiency. This is achieved by streamlining processes and optimizing supply chains.
- Production Efficiency - Efficient production management helps in overcoming scheduling challenges, ensuring timely delivery of custom fasteners.
- Scheduling Challenges - These can be mitigated through accurate demand forecasting, which projects future needs based on historical data and market trends.
- Supplier Communication - Open and prompt communication with suppliers provides clarity on expected lead times and potential disruptions, enabling better planning and control.
Balancing these elements ensures a smooth supply of custom fasteners, in alignment with business needs and timelines.
Related Article: A Guide to Bespoke Fasteners for Your Project
4.4 Available Finishing Services
The finishing services available for custom fasteners are numerous, each providing specific benefits to the product's functionality and aesthetics. Among these services are Cleaning & Polishing, CNC Machining, Coating, Grinding, and Heat Treatments.
Each of these processes plays a crucial role in ensuring the durability, performance, and overall quality of the final product.
Cleaning & Polishing
In the realm of custom fasteners, cleaning and polishing services play a pivotal role in ensuring the final product not only meets aesthetic requirements, but also offers a robust defense against corrosion. These services primarily comprise:
- Rust prevention - reducing the risk of damage.
- Surface finishing - enhancing the fastener's appearance.
- Metal cleaning - ensuring a smooth surface.
- Corrosion protection - prolonging the lifespan of the fastener.
CNC Machining
Harnessing the power of computer-aided software, CNC machining plays a critical role in milling, turning, stamping, and forming custom fasteners. The advanced technology offers precision engineering, quality control, and customized solutions. The benefits of CNC machining are manifold.
Coating
To ensure longevity and durability of custom fasteners, measures such as electroplating or powder coating can be employed to prevent corrosion and abrasion.
- Coating Techniques, Benefits: Enhances durability and appearance.
- Electroplating vs Powder Coating: Electroplating offers gloss, powder coating offers thickness.
- Corrosion Prevention Methods: Both techniques provide effective protection.
- Abrasion Resistance Options: Electroplating offers better resistance.
- Custom Coating Solutions: Tailored to specific requirements.
Grinding
Precision in grinding is paramount when it comes to tailoring custom fasteners to specific end-configuration needs for various design and application purposes.
Precision grinding ensures optimal surface finishing, while tool sharpening and metal shaping techniques aid in precise material removal.
This meticulous process delivers custom-designed fasteners with exact features, providing control over your project's final outcome.
Heat Treatments
In the realm of custom fasteners specifications, heat treatments serve as a critical finishing service, enhancing the durability and lifespan of the fasteners.
- Heat treatment benefits include increased strength and wear-resistance.
- The heat treatment process involves controlled heating and cooling.
- Various heat treatment techniques exist tailored to specific applications.
- Heat treatment applications span industries from automotive to construction.
- Heat treatment considerations should include material type, desired properties, and usage conditions.
Hot Forging
Hot forging is a vital process in custom fastener specifications. It involves the use of heat to modify metal through pressing, hammering, or other forming techniques. This heat treatment process offers numerous benefits such as improved strength and reduced material waste.
Key to this process is temperature control in forging. It enhances hot forming advantages and ensures a superior, tailor-made fastener.
Drilling
While temperature control is crucial during the hot forging process, equally important is the precision and technique used in the drilling stage of custom fastener production - a key aspect of available finishing services.
Key points to consider include:
- Drill maintenance for long-lasting operation.
- Choice of drill types to suit the material.
- Implementing drilling safety protocols.
- Employing efficient drilling techniques for optimal results.
Cross Drilling
How does cross drilling factor into the production of custom fasteners and what makes it a crucial aspect of available finishing services?
Precision in cross drilling is key to ensuring the integrity of custom fasteners. This technique offers numerous cross drilling benefits, but also presents certain challenges. Modern industrial drilling advancements mitigate these challenges, making cross drilling an essential part of optimal fastener production.
Cut & Chamfer
Just as cross drilling plays a pivotal role in the manufacturing of custom fasteners, the process of Cut & Chamfer is equally significant, providing a precise and clean finish to the fasteners.
This involves:
- Chamfering techniques for high-quality finishes
- Ensuring cut accuracy through appropriate tool selection
- Realizing chamfering benefits in durability and ease of installation
- Achieving cut speed optimization for cost-efficiency.
Milling
In the realm of custom fasteners manufacturing, milling stands as a crucial stage, offering a range of finishing services. With milling technology advancements, precision in milling has increased, demanding meticulous milling machine selection.
Adherence to milling safety protocols is paramount, but equally significant is understanding the environmental impact of milling. This control over the process ensures enhanced product quality and performance.
Grooving
Offering an additional layer of customization, grooving is a critical finishing service in custom fasteners manufacturing that demands precision and expertise.
- Grooving techniques enhance product reliability.
- Specialized grooving tools ensure high precision.
- Grooving efficiency contributes to faster production times.
- Various grooving applications enable flexible design possibilities.
Harness the power of grooving precision for superior custom fasteners today.
5. How Do I Choose the Right Fastener for My Application?
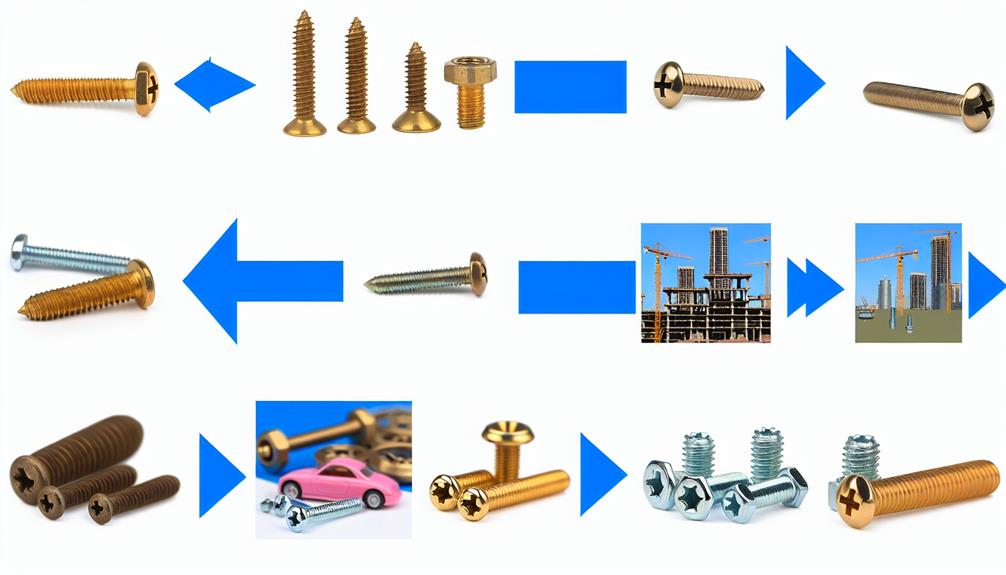
To select the most suitable fastener for your specific application, key considerations should include the material of the fastener, its life cycle, the environment in which it will be used, and any associated security requirements.
Material selection is crucial as it determines the strength and durability of the fastener. A higher-grade material generally provides greater strength and longevity, ensuring the fastener can withstand rigorous application requirements. Size is another critical factor. The fastener must be compatible with the components it is meant to hold together.
In terms of environmental factors, the fastener should have corrosion resistance to withstand varying conditions. The cost and efficiency of a fastener are equally important: a high-quality fastener that is cost-effective and efficient ensures a better return on investment.
Consider the following table to help you make a more informed decision:
Consideration | Importance | Example |
---|---|---|
Material Selection | Determines strength and durability | Stainless Steel for high strength |
Size and Compatibility | Must fit with the components | Size should match the material thickness |
Corrosion Resistance | Determines life cycle in different environments | Galvanized steel for outdoor use |
Cost and Efficiency | Impacts the return on investment | Bulk purchasing for cost-efficiency |
Security Requirements | Ensures the fastener serves its purpose | Tamper-resistant for high-security applications |
6. Why Choose Us for Custom & Specialty Fasteners?
Choosing us for your custom and specialty fasteners needs ensures access to our extensive range of materials and manufacturing capabilities, promising high-quality products tailored to your specific requirements. Our expertise in precision engineering and vast assortment of specialty alloys allow us to create fasteners for unique applications with a high degree of accuracy and durability.
- Custom finishes: We offer a diverse range of finishes to meet the unique needs of your projects, ensuring your fasteners not only perform exceptionally but also aesthetically match their surroundings.
- Specialty alloys: Our extensive inventory includes a variety of specialty alloys, enabling us to produce fasteners that meet specific strength, corrosion resistance, and temperature requirements.
- Precision engineering: Advanced manufacturing techniques and rigorous quality control procedures ensure each fastener is crafted to exact specifications.
- Expert consultation: Our specialists are available to guide you through the selection process, ensuring the fasteners you choose meet your project's needs.
Frequently Asked Questions
What Is the Manufacturing Process for Custom Fasteners?
The manufacturing process for custom fasteners involves design considerations, tooling requirements, and quality control measures. It faces production challenges, but advancements in innovation continue to improve efficiency and precision in the production process.
What Industries Commonly Use Custom Fasteners?
Custom fasteners, with their versatility, are extensively used in various industries. Predominantly, these include aerospace applications, the automotive industry, meeting diverse construction demands, and the electronics sector, providing indispensable solutions for secure and reliable connections.
Are Custom Fasteners More Expensive Than Standard Ones?
While cost comparison reveals custom fasteners may initially seem more expensive, the quality investment and customization value often outweigh the initial price factors. Budget considerations must include long-term value, making custom fasteners a wise choice.
Can Custom Fasteners Increase the Durability or Lifespan of My Project?
Yes, custom fasteners can enhance your project's durability and lifespan. Material selection and fastener maintenance significantly impact these factors. Through a lifespan comparison, custom fasteners often outperform standard ones, positively affecting your project's longevity.
How Long Does It Take to Produce and Deliver Custom Fasteners?
The production timeline for custom fasteners depends on complexity and quantity. Delivery methods vary, but tracking is provided. Rush orders are accommodated, though production delays may occur. Detailed timeline will be shared upon order confirmation.
Mikehardware-your trusted Custom Fasteners manufacturer
In conclusion, when seeking the ideal solution for fastening needs, custom fasteners offer a versatile and adaptable choice. They cater to a wide range of applications and industries, offering unique specifications that standard fasteners may not fulfill.
As the adage goes, 'the right tool for the right job,' choosing custom fasteners ensures a perfect fit for specific requirements, thereby enhancing the efficiency and durability of the project.
At Dongguan Mike Hardware Co., Ltd., precision engineering meets innovation, delivering impeccable CNC product manufacturing solutions. Explore our array of customized fasteners, screws, and coatings, ensuring your projects excel in performance, precision, and quality.