CNC Machining Small Parts: Precision Engineering at Its Best
CNC machining of small parts represents a pinnacle in precision engineering, where the meticulous creation of diminutive, complex components is not just necessary but critical for modern technological applications. This process demands high levels of accuracy and repeatability, leveraging sophisticated equipment and skilled expertise to achieve dimensions and tolerances that are often beyond the capabilities of traditional machining. As industries such as aerospace, medical, and electronics increasingly rely on microcomponents, the techniques and tools employed in CNC machining small parts continue to evolve. Exploring these advancements offers a glimpse into the future of manufacturing, where the scale of precision continues to narrow.
Key Takeaways
- CNC machining provides high precision for complex, small-scale parts, meeting stringent industry tolerances.
- Advanced machines like CNC milling, turning, and laser cutting handle intricate geometries and delicate materials.
- Material selection, including metals like aluminum and plastics like nylon, is critical for achieving desired precision and functionality.
- Small part machining uses specialized tools and techniques to ensure efficiency, accuracy, and minimal tool wear.
- Quality control measures, including in-process and final inspections, guarantee that small parts adhere to rigorous standards.
1. What is CNC Machining Small Parts?
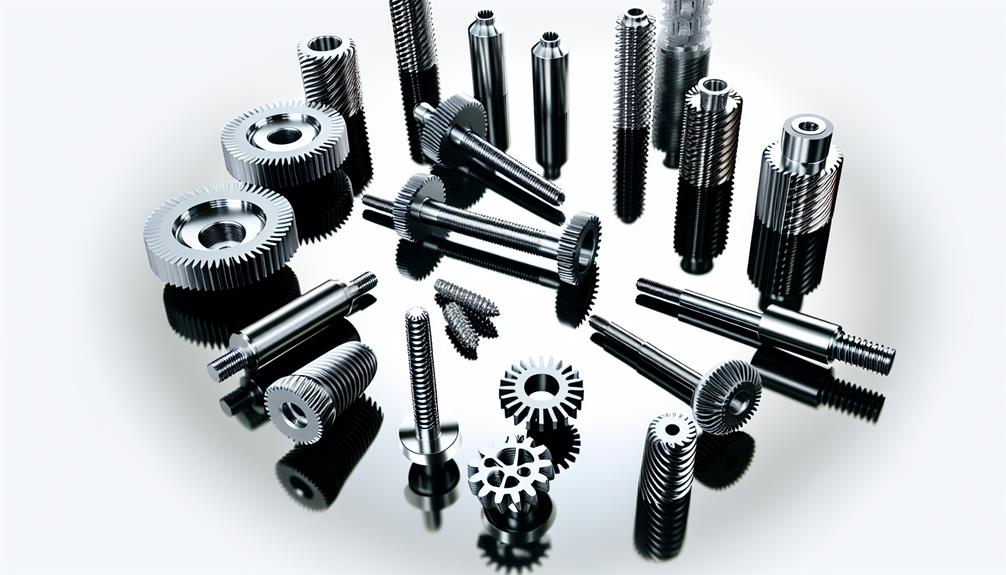
CNC machining of small parts involves the precise and automated control of machining tools like mills, lathes, or grinders to produce small, intricate components. This process is essential for creating precision components where high accuracy and tight tolerances are paramount. The capabilities of CNC machines to handle complex geometries with precision cater to sectors demanding stringent specifications and consistency.
The term 'micro machining' refers to the CNC operations tailored to manufacture microscale parts. These components often require working within tolerances that are only a few microns wide, highlighting the need for sophisticated equipment and skilled operation.
The precision in micro machining ensures that each part meets rigorous standards of quality and performance.
2. Applications and Products
Given their high precision and adaptability, CNC-machined small parts are integral to various industrial applications, including the production of brackets, adapters, knobs, and more. These precision components are essential in industries where minute tolerances and exact specifications are critical. Advanced technology in CNC machining allows for the creation of specialized products that meet the unique demands of sectors such as aerospace, medical devices, and robotics.
Custom applications benefit significantly from the versatility of CNC machining, enabling the production of unique designs that are tailored to specific functional requirements. The adaptability of CNC machines to work with a wide range of materials also enhances their suitability for producing high-quality, durable small parts for advanced technological applications.
The following table outlines some key small parts produced using CNC machining and their primary applications:
Part | Industry | Application |
---|---|---|
Heat sinks | Electronics | Thermal management |
Standoffs | Construction | Spacing and mounting components |
Bushings | Automotive | Reducing friction and wear |
Levers | Machinery | Control and adjustment |
Cranks | Bicycling | Power transfer mechanisms |
This precision engineering not only ensures reliability but also supports innovation across various fields by providing essential components that meet exacting standards.
3. Which Machines Are Used for Machining Small Parts?
Several types of machines are utilized for machining small parts, including CNC milling and turning machines, CNC wire EDM, and CNC laser cutting machines. These devices harness advanced technology to create precision components with intricate designs, exemplifying the pinnacle of micro machining.
CNC milling machines are pivotal in shaping miniature parts with complex geometries. They employ cutting tools that move along multiple axes to sculpt materials with high accuracy, adhering to ultra-precision standards and maintaining tight tolerances crucial for small-scale applications.
Similarly, CNC turning machines specialize in producing cylindrical components, rotating the workpiece against a cutting tool to achieve a desired form and finish.
CNC wire EDM stands out for its ability to cut thick and hard materials, achieving shapes that are otherwise challenging to produce. This method uses a thin wire and electrical discharges to erode material precisely, ideal for components requiring meticulous details and superior surface quality.
Lastly, CNC laser cutting machines offer a non-contact method of producing parts, which is beneficial for delicate or fragile materials. The laser beam provides a concentrated heat source, allowing for the cutting or engraving of extremely fine features and complex patterns. This capability is essential when working with diverse and sophisticated designs in small-part machining.
4. Common Materials Used in Small Part Machining
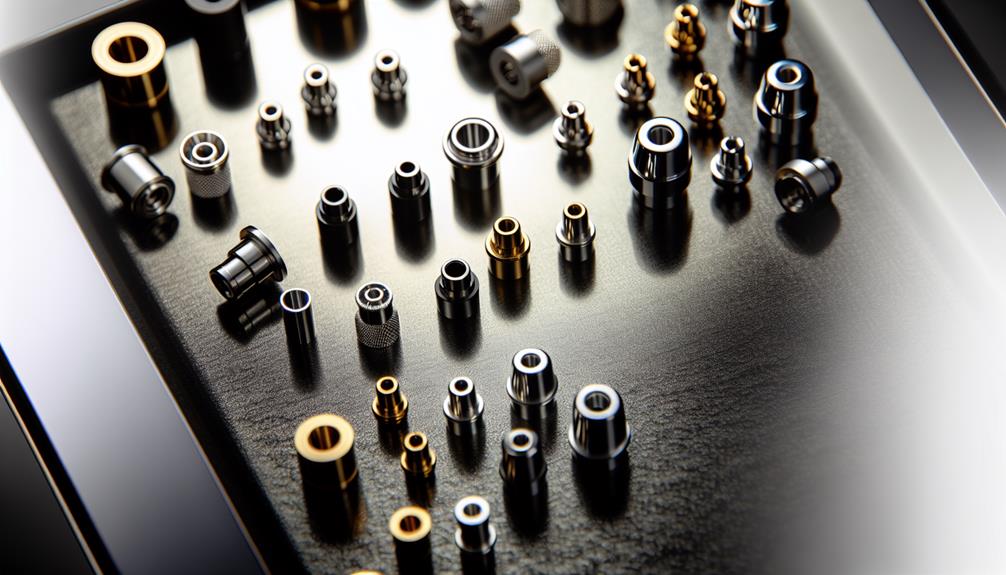
In the realm of CNC machining for small parts, both metals and plastics play pivotal roles due to their distinct characteristics. Metals such as stainless steel and aluminum are favored for their durability and strength, essential for high-stress applications in automotive and aerospace industries.
On the other hand, plastics are chosen for their versatility and lighter weight, which are advantageous in electronic and consumer goods.
Metals
Common metals used in small part CNC machining include aluminum, stainless steel, and brass. Each material is selected based on specific metal properties that meet the demands of strength, machinability, and corrosion resistance.
Aluminum, known for its lightweight and ductility, is favored in aerospace and automotive applications for its ease of machining and good thermal conductivity. Stainless steel is chosen for its robustness and exceptional resistance to corrosion and heat, making it ideal for medical devices and food processing equipment. Brass, with its low friction and spark resistance, is preferred for electrical components and decorative items.
Material selection is critical in achieving desired tolerances and precision. High-precision machining requires materials that can withstand rigorous machining processes without deforming. Surface finishes are also a vital consideration; smoother finishes can be achieved with certain metals, enhancing the aesthetic and functional qualities of the parts.
Heat treatment processes are applied to metals like stainless steel to enhance their mechanical properties, such as hardness and resistance to wear. Understanding these aspects ensures that engineers and machinists can control the outcome of the machining process, leading to parts that meet stringent industry-specific standards with high reliability and performance.
Plastics
Transitioning from metals, plastics like acrylic, nylon, and Delrin are also frequently employed in small part CNC machining due to their distinct advantages and applications. Understanding the specific plastic properties is crucial for optimizing the machining process and achieving the desired outcomes.
Acrylic offers excellent transparency and resistance to UV light, making it ideal for optical components, while nylon is valued for its strength and resistance to abrasion, useful in gears and bearings. Delrin, known for its high stiffness and low friction, is often chosen for precision parts requiring dimensional stability.
Material selection plays a pivotal role in meeting the stringent tolerance requirements of small part machining. Each plastic type presents unique machining considerations. For example, Delrin's low moisture absorption allows for tighter tolerances, whereas nylon's flexibility may require specific adjustments to avoid deformation during the machining process.
Additionally, surface finishing techniques must be carefully chosen to enhance the functionality and aesthetics of the machined parts. Acrylic might necessitate flame polishing to achieve a glass-like finish, whereas nylon and Delrin could need CNC milling for a smooth, precise surface that adheres to exact specifications. These strategic decisions ensure that each component meets the rigorous demands of specialized applications.
5. Tools and Techniques in Small Part Machining

In the realm of CNC machining small parts, selecting the appropriate tools and applying precise techniques are paramount. Each tool is specifically designed to accommodate the intricacies and scale of small components, enhancing both efficiency and accuracy.
Understanding these machining techniques is critical for achieving the desired outcomes in complex miniature productions.
Tools
Several cutting tools are essential for the precise and efficient machining of small parts. Cutting tools selection, tool maintenance, tool wear analysis, tool life optimization, and tooling strategies are critical aspects that demand meticulous attention from engineers and technicians.
Proper selection of cutting tools is paramount. Factors such as material hardness, machining type, and the complexity of the part dictate the choice of drills, end mills, turning tools, or milling cutters. Tool maintenance cannot be overstated; regular checks and timely repairs ensure consistent performance and prevent costly downtimes. Moreover, analyzing tool wear enables predictive maintenance, enhancing tool life and ensuring sustained quality.
Optimizing tool life is closely linked to understanding and implementing effective tooling strategies. This involves selecting the right tool material, coating, and geometry based on specific machining requirements and conditions.
Tool Type | Applications | Considerations |
---|---|---|
Drills | Hole making in varying depths | Drill design and material |
End Mills | Slotting, profiling, contouring | Cutter geometry and coating |
Turning Tools | Material removal from cylinders | Tool material and rigidity |
Understanding and applying these principles ensures control over the machining process, leading to high precision and efficiency in producing small parts.
Machining Techniques
How do machinists achieve the intricate details required in small part machining? Utilizing a combination of precision cutting and advanced methods ensures that even the most complex components meet exact specifications.
Turning, for instance, allows for the creation of parts with rotational symmetry by rotating the part against a cutting tool, achieving precise outer diameters.
Milling provides a versatile solution, where a rotating cutting tool moves along multiple axes to intricately carve out slots, pockets, and contours.
Drilling and tapping contribute to efficient operations by respectively creating and threading holes that are essential for component assembly.
Grinding, employing abrasive wheels, achieves finishes and dimensions with high precision, necessary for components requiring smooth surfaces and tight tolerances.
Incorporating innovative technology, machinists optimize these techniques for custom solutions tailored to specific project needs. Whether it's adapting milling operations to produce unique geometric forms or employing specialized grinding tools for superior surface quality, the focus remains on enhancing productivity and precision.
This continuous integration of new technologies and methods not only drives the industry forward but also ensures that machinists can respond effectively to the evolving demands of precision engineering.
6. Common Challenges in CNC Machining Small Parts

Machining small parts with CNC technology presents several challenges, including maintaining tight tolerances, managing material properties, and ensuring quality finishing processes.
One of the most significant precision challenges is the requirement for extremely tight tolerances, which are difficult to control due to the intricate nature of small components. This difficulty is compounded by the inherent properties of the materials being machined, which may react unpredictably under the stresses of high-speed machining.
Another critical issue is the challenge of drilling deep holes in small parts, which requires specialized tools and techniques to achieve the necessary precision without causing damage to the part or tool. The slow production speed often associated with these operations can lead to increased costs and extended lead times, which may not be acceptable in competitive market environments.
Additionally, effectively holding the job during the machining process is crucial to prevent errors and ensure consistent quality. The small size of the components often requires innovative fixtures and clamping systems designed to hold the parts securely without causing deformation or damage.
Addressing these challenges requires a combination of advanced CNC technology, skilled operators, and rigorous process control to achieve the desired outcomes in the manufacturing of small parts.
7. Quality Control Measures in CNC Machining Small Parts
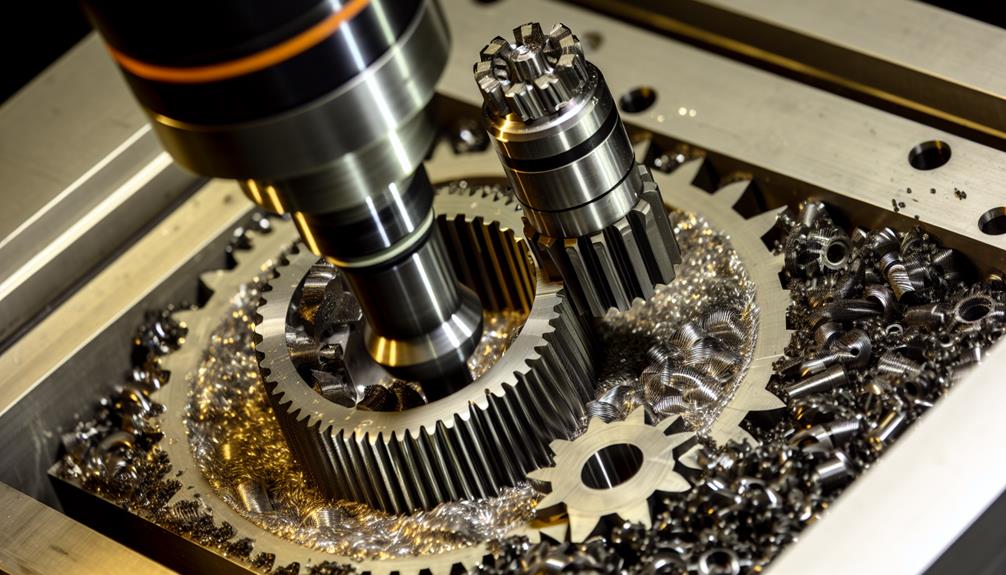
Addressing common challenges in CNC machining, quality control measures play a vital role in ensuring the production of small parts meets stringent standards. These measures encompass a range of methods, including advanced inspection techniques and rigorous process control, all aimed at achieving superior quality assurance.
The quality control process begins with in-process inspection, utilizing tools such as calipers and micrometers to monitor the accuracy of parts as they are machined. This real-time feedback allows for immediate corrections, ensuring each component adheres to precise specifications.
Following this, a final inspection is conducted using more sophisticated equipment like CMMs (Coordinate Measuring Machines) to verify that all finished parts meet the required tolerances and quality benchmarks.
Statistical Process Control (SPC) is another critical aspect, where data collected during machining processes is analyzed to maintain control limits and enhance the overall reliability of the production process. This statistical approach helps in preempting deviations before they lead to defects.
Furthermore, maintaining detailed documentation and meeting traceability requirements are essential for accountability and continuous improvement, which are integral to ISO 9001 certification. This standard provides a framework that reinforces a commitment to quality at every stage of the machining process, ensuring that each small part produced exemplifies the highest quality standards.
8. CNC Machining Small Parts Services
Avanti Engineering offers exceptional CNC machining services for small parts, leveraging their expertise to transform intricate designs into high-quality, precision-crafted components. With a focus on producing precision components that meet tight tolerances, Avanti utilizes advanced technology to ensure high accuracy in every project. Their commitment is not just to meet, but often to exceed the stringent requirements demanded by various industries.
Their facility is equipped with state-of-the-art machinery that allows for the production of custom solutions, catering to clients who require unique specifications and exceptional quality. The technical team at Avanti Engineering is proficient in handling complex challenges, translating detailed client requirements into tangible products that adhere to the highest standards of precision engineering.
For businesses seeking a partner that values precision and quality, Avanti Engineering is a prime choice. Their meticulous attention to detail ensures that each component is not only functional but also perfectly aligns with client expectations.
This dedication to quality and precision underpins their reputation as leaders in the machining of small, complex parts. Contact Avanti Engineering today to discuss your specific needs for precision-engineered small parts and experience their unparalleled service firsthand.
Frequently Asked Questions
How Cost-Effective Is CNC Machining for One-Off Small Part Production?
CNC machining for one-off small part production is moderately cost-effective. Careful cost analysis, material selection, and quality control measures balance speed and accuracy, offering substantial benefits in prototyping and customization despite some drawbacks.
Can CNC Machining Accommodate Biodegradable Material for Small Parts?
CNC machining can indeed accommodate biodegradable materials for small parts, aligning with sustainability goals through precision engineering. This capability allows for environmentally responsible production while maintaining high-quality and precise manufacturing standards.
What Are Typical Lead Times for Small Batch CNC Projects?
Typical lead times for small batch CNC projects vary, influenced by material selection, part complexity, and CNC programming. Production efficiency, speed optimization, and quality control measures also significantly affect the scheduling of deliverables.
Are There Any Size Limitations for Parts in CNC Micro-Machining?
In CNC micro-machining, size constraints hinge on achieving high precision. Despite focusing on miniature components, the complexity and accuracy required often dictate tolerance limits, with dimensions typically ranging down to a few micrometers.
How Does Operator Skill Affect the Outcome of CNC Small Parts?
Operator expertise significantly impacts machining accuracy, tool selection, and quality control, thereby enhancing production efficiency. Skilled operators adeptly manage intricate processes, ensuring high precision and optimal outcomes in CNC small parts manufacturing.
Mikehardware-your trusted Custom Special Screws manufacturer
In conclusion, CNC machining of small parts exemplifies the zenith of precision engineering, providing critical components across various industries.
A noteworthy statistic reveals that the precision machining market is expected to grow by 7% annually, underscoring the increasing reliance on microscale components with high accuracy.
The continuous advancements in technology, coupled with stringent quality control measures, ensure that CNC machining remains indispensable for manufacturing small parts with exacting standards in a rapidly evolving industrial landscape.
At Dongguan Mike Hardware Co., Ltd., precision engineering meets innovation, delivering impeccable CNC product manufacturing solutions. Explore our array of customized fasteners, screws, and coatings, ensuring your projects excel in performance, precision, and quality.
Elevate your engineering prowess with our tailored solutions—Contact us for a free quote of your ideal Special Screw.