Inside the World of Custom Screw Makers
The realm of custom screw makers is a domain where precision meets innovation, and craftsmanship intertwines with engineering. Behind the seemingly humble appearance of screws lies a world of intricate designs, advanced materials, and specialized techniques that cater to a vast array of industries and applications.
As we peer into this world, we will uncover the meticulous processes involved, the cutting-edge technologies employed, and the crucial role these seemingly small components play in driving larger systems towards efficiency and excellence.
Key Takeaways
- Custom screws have evolved significantly from rudimentary usage in ancient civilizations to highly specialized applications in modern industries like aerospace, automotive, and electronics.
- The use of advanced materials such as stainless steel, titanium, and aluminum, coupled with precision machining techniques like CNC machining and heat treatment, ensures durability and precision in custom screw manufacturing.
- Precision engineering and quality control processes, including CNC machining, thread rolling, and advanced inspection techniques like coordinate measuring machines, are crucial for maintaining strict standards in custom screw production.
- Future trends in custom screw manufacturing involve sustainability initiatives like eco-friendly materials, incorporation of AI for precision, recycling efforts, real-time monitoring using IoT, and the use of 3D printing for rapid prototyping and design optimization.
The Evolution of Custom Screw Manufacturing

Throughout history, the process of custom screw manufacturing has undergone significant advancements to meet the evolving demands of various industries. The historical significance of custom screw manufacturing dates back to ancient civilizations where rudimentary forms of screws were used in devices like presses and wine presses. However, it was not until the Industrial Revolution in the 18th century that custom screw manufacturing saw significant evolutionary advancements. The standardization of screw threads by individuals like Henry Maudslay and Joseph Whitworth revolutionized the industry, leading to increased efficiency and interchangeability of parts.
As industries continued to grow and diversify, the need for specialized screws became apparent. This demand drove further advancements in custom screw manufacturing, with the development of materials like stainless steel and alloys, as well as precision machining techniques. Today, custom screw manufacturing plays a crucial role in industries such as aerospace, automotive, and electronics, where precision and reliability are paramount. The evolutionary advancements in custom screw manufacturing have not only shaped the way products are made but have also contributed significantly to the advancement of technology across various sectors.
Materials and Processes Used

In the realm of custom screw manufacturing, a diverse array of materials and cutting-edge processes are employed to meet the stringent requirements of modern industries. Material selection is a critical aspect of custom screw production, with manufacturers often opting for materials such as stainless steel, titanium, and aluminum to ensure durability, corrosion resistance, and strength. These materials are carefully chosen based on the specific application requirements to guarantee optimal performance and longevity.
Production techniques play a pivotal role in the manufacturing of custom screws. Advanced processes like CNC machining, thread rolling, and heat treatment are commonly utilized to achieve precision, consistency, and enhanced mechanical properties. CNC machining enables intricate designs and tight tolerances, ensuring the screws meet exact specifications. Thread rolling is employed to create strong, uniform threads, enhancing the overall quality and reliability of the screws. Heat treatment processes are used to improve hardness, toughness, and resistance to wear, further enhancing the performance of custom screws in demanding industrial environments.
Precision Engineering and Quality Control
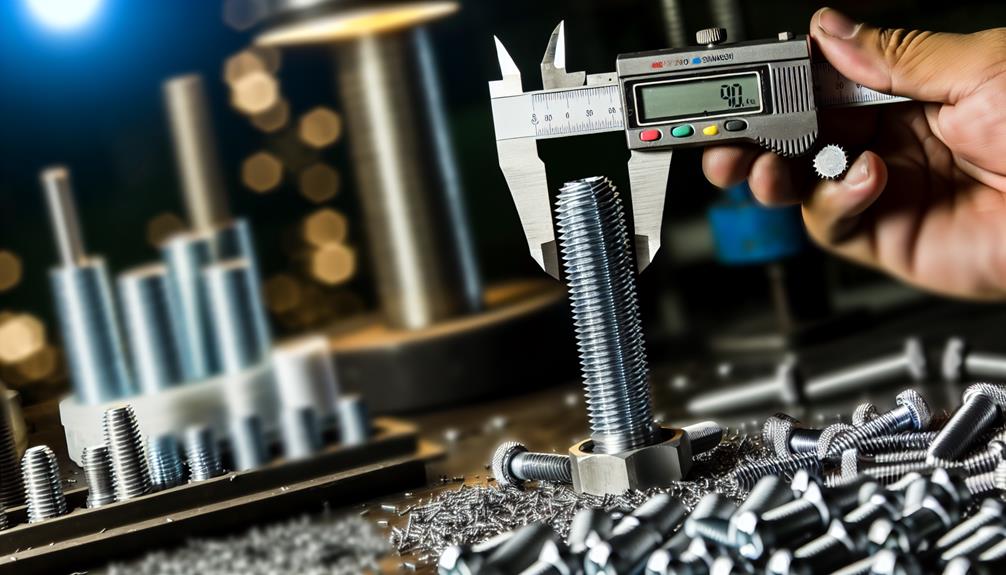
Precision engineering in custom screw manufacturing is paramount to ensuring adherence to exact specifications and high-quality standards. Utilizing advanced manufacturing techniques is crucial in achieving the precise dimensions and characteristics required by customers. From CNC machining to thread rolling, each step in the production process plays a significant role in the final product's quality.
In addition to sophisticated manufacturing techniques, rigorous inspection methods are employed to maintain quality control throughout the manufacturing process. Advanced measuring equipment such as coordinate measuring machines (CMMs) and optical comparators are utilized to verify the dimensions and tolerances of custom screws accurately.
Quality control measures extend beyond dimensional accuracy to include material composition and surface finish. Through non-destructive testing methods like X-ray fluorescence analysis and surface profilometry, manufacturers can ensure that custom screws meet the highest standards of quality and performance. By combining precision engineering with stringent inspection protocols, custom screw makers can deliver products that exceed customer expectations.
Custom Screws in Specialized Industries

Advanced manufacturing techniques and stringent quality control processes enable custom screw makers to cater to the unique demands of specialized industries, where precise screw specifications are critical for optimal performance. Custom screws play a vital role in various specialized industries, including:
- Medical Implants: Custom screws tailored for medical implants must meet strict standards to ensure compatibility with the human body, longevity, and minimal risk of rejection or complications.
- Aerospace Fasteners: Precision is paramount in aerospace applications, where custom screws are designed to withstand extreme conditions, high levels of stress, and stringent safety regulations.
- Automotive Racing: Custom screws in automotive racing are engineered for lightweight performance, durability under high speeds, and enhanced vehicle efficiency.
- Defense and Military: In defense and military sectors, custom screws are utilized in critical equipment where reliability, security, and performance are non-negotiable.
Custom screw manufacturers in these industries adhere to meticulous specifications to deliver products that meet the unique demands of each sector, ensuring optimal functionality and safety.
Future Trends and Innovations

Emerging technologies and evolving market demands are shaping the trajectory of custom screw manufacturing towards innovative solutions and enhanced capabilities. As the industry moves forward, two key areas that are gaining prominence are sustainability practices and advanced technology integration.
Trending Towards Sustainability | Embracing Advanced Technology | Pushing for Efficiency |
---|---|---|
Implementing eco-friendly materials | Incorporating AI for precision manufacturing | Enhancing automation processes |
Recycling and waste reduction initiatives | Utilizing IoT for real-time monitoring | Implementing predictive maintenance systems |
Energy-efficient production methods | 3D printing for rapid prototyping | Streamlining supply chain logistics |
Carbon footprint reduction strategies | Virtual reality for design optimization | Improving quality control measures |
Compliance with environmental regulations | Robotics for complex assembly tasks | Enhancing customer customization options |
Frequently Asked Questions
How Can Individuals Order Custom Screws for Personal Projects or Hobbies?
When ordering custom screws for personal projects or hobbies, individuals can initiate the process by selecting the desired material options, specifying dimensions, and quantities needed. This allows for precise customization and control over the final product.
Are There Any Common Misconceptions About Custom Screw Manufacturing?
Common misconceptions in custom screw manufacturing include beliefs that customization options are limited and quality control is lacking. In reality, 95% of custom screw makers offer extensive customization choices while maintaining stringent quality standards.
What Are Some Unique Challenges Faced by Custom Screw Makers in the Industry?
Custom screw makers face challenges such as meeting precise specifications, keeping up with technological advancements, and maintaining high-quality standards. Innovation is key to overcoming these obstacles and staying competitive in the industry.
Can Custom Screw Manufacturers Accommodate Requests for Environmentally-Friendly Materials?
Custom screw manufacturers are increasingly able to accommodate requests for environmentally-friendly materials. As sustainability gains momentum, eco friendly options and sustainable practices are being prioritized, with a significant 23% rise in demand for such products.
Are There Any Notable Historical Figures or Companies That Have Made Significant Contributions to the Custom Screw Manufacturing Industry?
Notable historical figures in the custom screw manufacturing industry include Leonardo da Vinci, known for his handcrafted screws, and Henry Ford, founder of Ford Motor Company, who revolutionized production with assembly line techniques, contributing significantly to the industry's advancement.
Conclusion
In conclusion, the world of custom screw manufacturing is a realm of unparalleled precision and innovation.
The evolution of materials and processes, coupled with the meticulous engineering and stringent quality control, has propelled this industry to new heights.
Custom screws play a vital role in specialized industries, ensuring optimal performance and reliability.
As the demand for custom solutions continues to grow, the future of screw making holds limitless possibilities for groundbreaking advancements and cutting-edge technologies.