Top Factors to Consider When Sourcing Metal Fasteners for Custom Manufacturing
Imagine you're standing in a bustling factory where the clink of metal fasteners being sorted echoes through the air. You're tasked with choosing the best fasteners for a custom project, and it's crucial you consider not just their strength and durability, but also factors like corrosion resistance and cost-effectiveness. However, the decision doesn't stop there. You'll also need to evaluate the reliability of suppliers and whether they meet stringent industry standards. What might happen if you overlook these essential criteria? Let's explore how these factors interplay to affect your manufacturing success and what pitfalls you might avoid by paying close attention to them.
Key Takeaways
- Evaluate mechanical properties like strength and durability for reliable performance.
- Choose corrosion-resistant finishes suitable for the specific environmental conditions.
- Balance quality with cost, considering both initial and long-term expenses.
- Verify supplier reliability, including timely deliveries and quality certifications.
- Ensure compliance with industry-specific standards and regulations for fasteners.
Material Selection Criteria
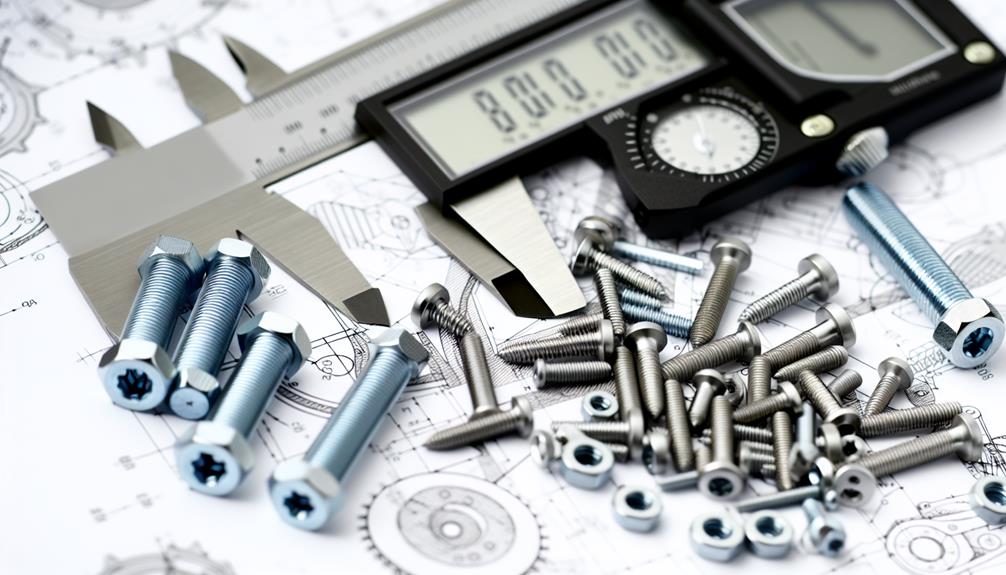
You need to consider several factors when selecting materials for metal fasteners, including strength, corrosion resistance, and cost. As you weigh your options, understanding the different surface finish options is crucial. These finishes not only influence the appearance and performance of your fasteners but also affect their durability in various environments.
You've got choices ranging from electroplating to powder coatings, each providing different levels of protection and aesthetic appeal. Make sure to match the surface finish with the specific needs of your application to ensure longevity and functionality.
Moreover, you can't overlook the environmental impact assessment of your selected materials. It's your responsibility to choose materials that not only meet your performance criteria but also align with environmental sustainability practices. Assess the production and disposal processes of these materials.
Are they recyclable? Do they emit harmful substances during manufacturing? Answering these questions will guide you in making an informed decision that balances functionality with environmental stewardship.
Corrosion Resistance Evaluation
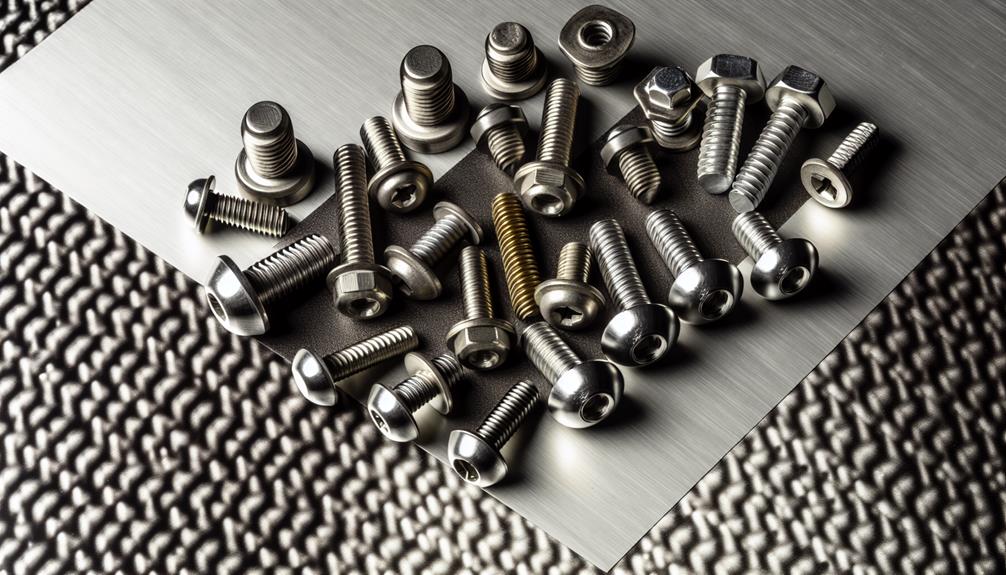
To ensure your metal fasteners last through harsh conditions, it's crucial to evaluate their corrosion resistance. You've got to assess how different surface finishes can enhance this property, especially under the specific environmental conditions your products will face.
Choosing the right surface finish isn't just about aesthetics; it's about survival. For instance, stainless steel fasteners might resist corrosion naturally, but adding a protective coating could extend their lifespan in more aggressive environments. You'll want to consider finishes such as zinc plating, black oxide, or even specialized coatings like Teflon, depending on the specific demands of your application.
You're also dealing with varying environmental conditions, which play a significant role in selecting the perfect fastener. Think about where and how your fasteners will be used. Are they exposed to salty air near the ocean? Will they encounter chemical exposure in industrial settings? Understanding these factors helps you make informed decisions that ensure longevity and functionality.
Mechanical Properties Analysis
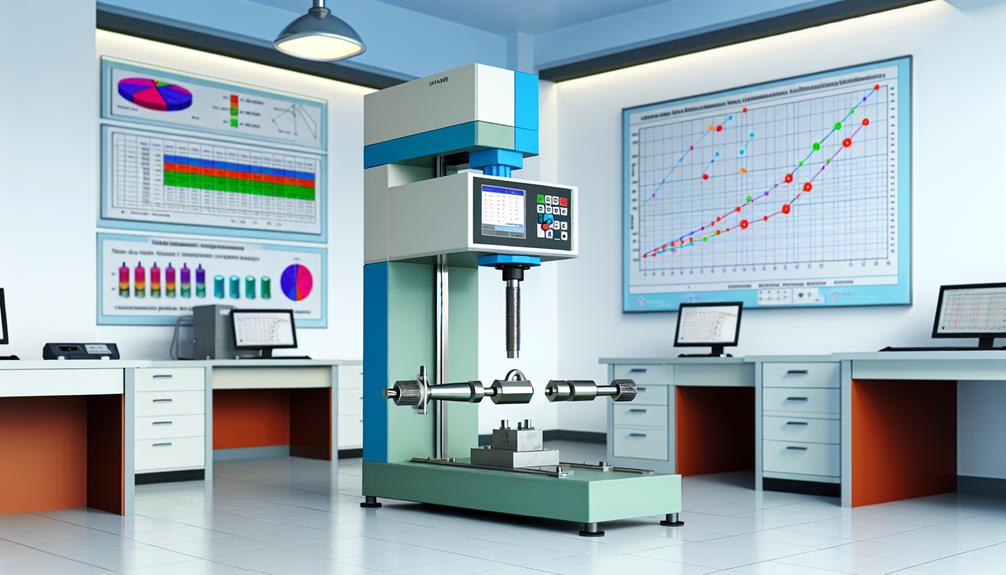
Assessing the mechanical properties of metal fasteners is crucial for determining their suitability in various applications. You need to zero in on several aspects such as heat treatment analysis and stress distribution to ensure the fasteners can withstand the demands of their intended use.
Heat treatment analysis enhances material strength and performance under stress. By understanding how heat treatment affects your fasteners, you'll be better equipped to select ones that won't fail under pressure. Stress distribution, on the other hand, ensures that the load is evenly spread across the fastener, reducing the likelihood of failure due to stress concentrations.
Surface finish assessment is equally essential. A high-quality surface finish not only protects against corrosion but also impacts the fatigue strength of the fastener. It's vital to choose fasteners with a surface finish that compleates their operational environment.
Here's a quick glance at what to check:
Property Evaluated | Why It Matters |
---|---|
Heat Treatment Analysis | Enhances strength and durability |
Stress Distribution | Prevents failure from uneven load |
Surface Finish | Increases corrosion resistance and strength |
Material Strength | Ensures longevity and reliability |
Cost and Budget Considerations
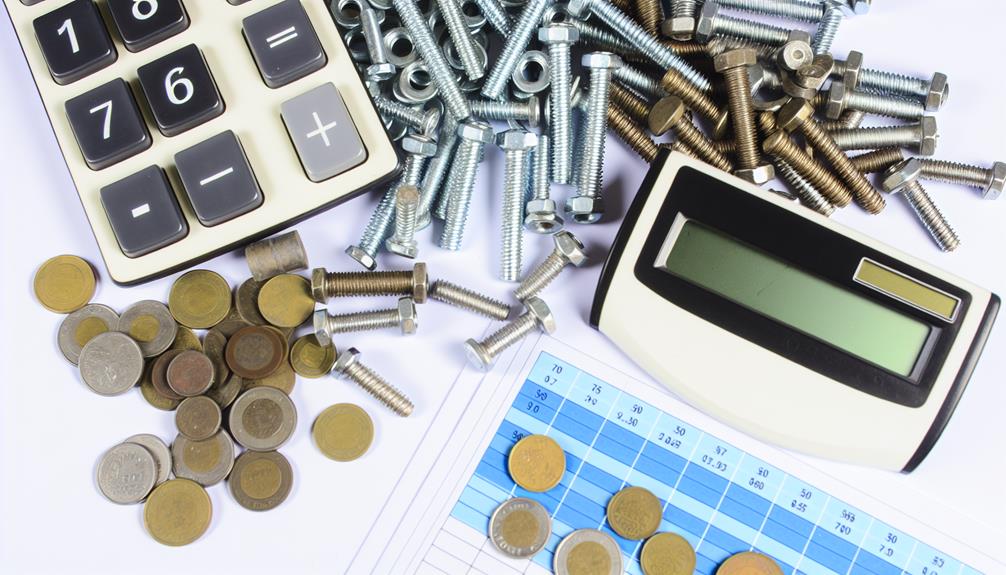
Understanding the cost implications is crucial when selecting metal fasteners for custom manufacturing projects. You need to be in control of every dollar spent, ensuring that your investment aligns with your project's quality and durability expectations.
Start by conducting thorough material cost comparisons. Different metals offer varying benefits, but their costs can impact your overall budget significantly. Stainless steel might offer corrosion resistance but at a higher price point compared to carbon steel, which, although less resistant, is much more cost-effective for indoor applications.
Implementing cost-saving strategies is another way you can take the reins on your budget. Consider buying in bulk if your production scale justifies it. Larger orders often reduce the unit cost significantly, giving you more bang for your buck.
Also, look into long-term contracts with suppliers if you have ongoing needs for metal fasteners. These agreements can lock in pricing and ensure supply continuity, which, in turn, stabilizes your budget over time.
Always balance cost with quality and the specific needs of your project to avoid future expenses related to maintenance or replacement. By staying vigilant and informed, you'll not only manage your costs effectively but also ensure that your project meets all necessary standards and expectations.
Supplier Reliability and Reputation

While managing your budget, it's equally important to evaluate the reliability and reputation of your metal fastener suppliers. You're striving for a partnership that brings not only cost-effectiveness but also trust and consistency to your projects.
Firstly, consider their industry experience. Suppliers with a long-standing presence typically understand market nuances better and can foresee potential challenges, ensuring you're not caught off-guard. Their experience often correlates with reliability, a crucial factor when every component counts. You need a supplier who consistently delivers quality, on time.
Next, delve into customer feedback. What're others saying about their dependability? Look for reviews and testimonials that highlight both strengths and shortcomings. This feedback can provide insight into their production capacity and communication skills. Can they handle your volume needs without compromising quality? Are they responsive and proactive in their communications? These are pivotal in maintaining project timelines and quality standards.
You're in control here, and choosing the right supplier means focusing on these elements to ensure a smooth and efficient workflow. Don't settle for less; your projects deserve a supplier whose reliability and reputation are as solid as the materials they provide.
Customization and Flexibility Options
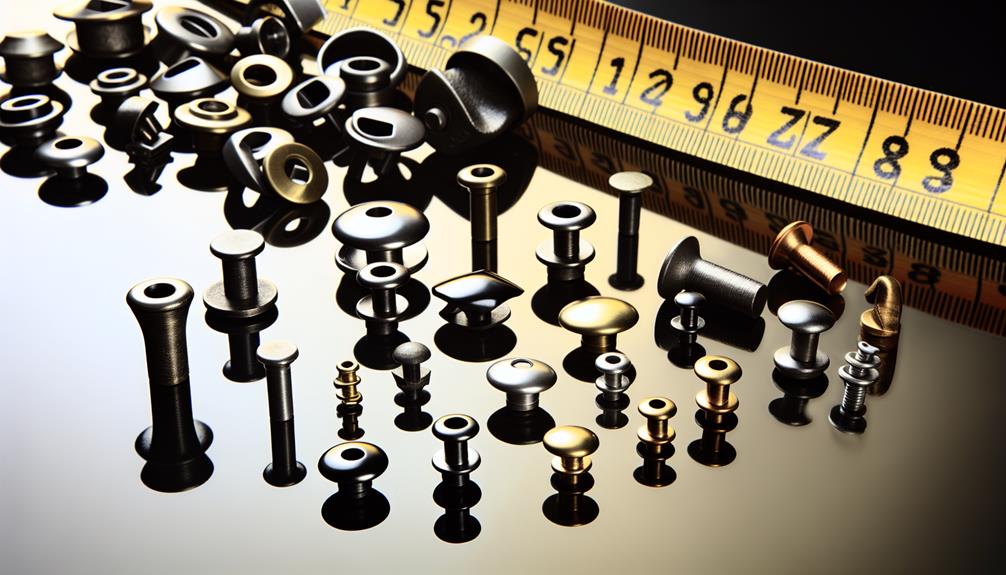
When selecting metal fastener suppliers, consider their ability to offer customization and flexibility tailored to your project's specific needs. You'll want a partner who can adapt to your demands, providing bespoke solutions that fit seamlessly into your manufacturing process. Opting for a supplier that excels in custom design not only ensures a perfect fit but also enhances the functionality and integrity of your final product.
Here are three key aspects to look for:
- Custom Design Capabilities: Ensure the supplier has proven expertise in developing custom fasteners. They should be able to match your exact specifications, whether you need unique sizes, shapes, or materials.
- Flexible Production Runs: Whether you need a small batch for prototypes or large-scale production, the right supplier should be able to handle your requirements without a hitch. Flexibility in order quantities ensures you don't overinvest or run short.
- Rapid Prototyping Services: Speed is crucial when bringing a new product to market. A supplier with rapid prototyping services can quickly turn your concepts into tangible products, allowing for faster testing and iteration.
Certification and Quality Standards
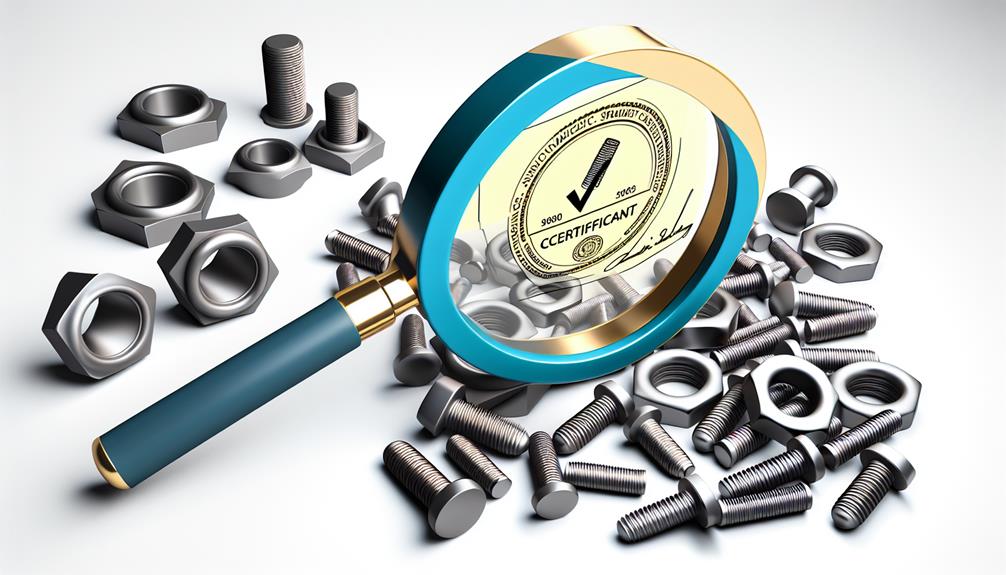
Beyond customization and flexibility, you should also verify that your metal fastener supplier meets rigorous certification and quality standards. Ensuring your supplier adheres to stringent industry standards and compliance requirements is crucial for maintaining control over the quality of your end products. This vigilance safeguards your projects against the risks of subpar components that could compromise your operations.
Start by requesting your supplier's certifications. These documents are your first line of defense, proving they've met specific standards like ISO 9001, which focuses on quality management systems and operational efficiency. Don't just take their word for it; look for third-party validation that these certifications are current and relevant to the types of fasteners you need.
You must also understand the specific compliance requirements relevant to your industry. Whether it's automotive, aerospace, or construction, each sector has its unique set of standards that your fasteners must meet. This could range from tensile strength to corrosion resistance. By ensuring compliance, you're not just following regulations; you're also delivering assurance to your customers that your products are reliable and of high quality.
Lead Time and Delivery Schedules
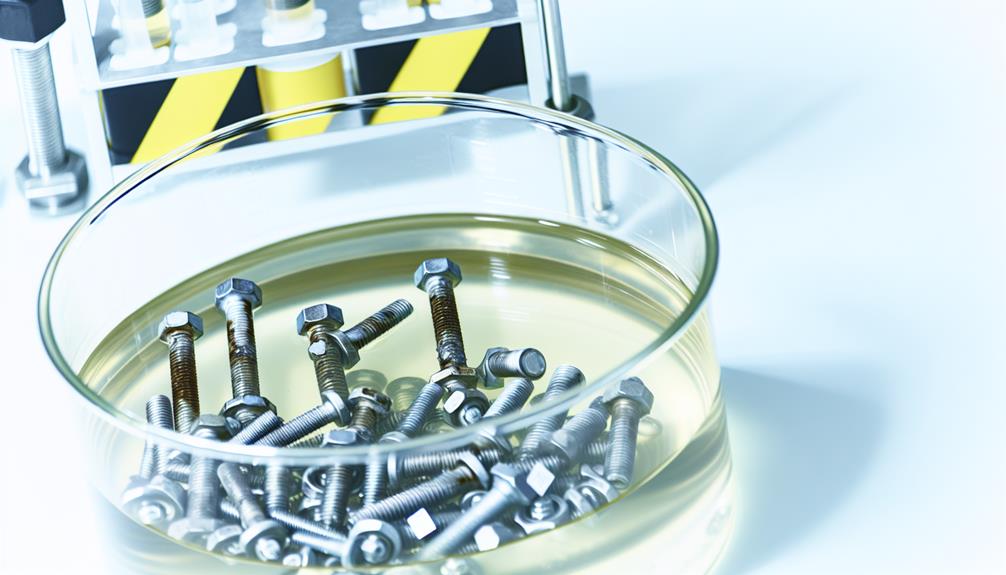
You should also consider the lead times and delivery schedules of your metal fastener suppliers to ensure they align with your project timelines. Delays can derail your entire project, costing you time and money, so it's crucial to choose suppliers who can deliver on time, every time.
Assess their production capacity and inventory management systems to gauge how well they can meet your demands. Efficient inventory management means that suppliers are less likely to run out of stock and can handle your orders quickly, even during peak demand. On the other hand, a robust production capacity ensures they can scale up operations to meet increased needs without significant delays.
Here are three critical aspects you need to keep an eye on:
- Supplier Reliability: Ensure the supplier has a proven track record of meeting delivery times.
- Flexibility in Scheduling: Look for suppliers who can adjust their schedules to fit sudden changes in your project needs.
- Communication and Updates: Opt for suppliers who provide regular updates on your order status and any potential delays.
Frequently Asked Questions
How Do Metal Fasteners Impact Overall Product Weight?
Metal fasteners affect your product's weight distribution and material selection, influencing both product performance and design flexibility. You'll find managing these aspects offers greater control over the final weight and functionality.
Are There Eco-Friendly Alternatives to Traditional Metal Fasteners?
Yes, you can opt for eco-friendly alternatives using sustainable materials like bamboo or recycled metals. These options let you maintain control over your environmental impact while ensuring product reliability.
Can Metal Fasteners Be Recycled or Reused?
Yes, you can recycle or reuse metal fasteners, giving you control over waste and costs. Recycling practices vary, so check local capabilities to ensure you're maximizing the potential for reuse and sustainability.
How Do Temperature Fluctuations Affect Metal Fastener Integrity?
Temperature fluctuations can weaken your metal fasteners by altering their material composition and reducing corrosion resistance. You'll want to choose materials adept at handling these changes to maintain control over fastener integrity.
What Are the Latest Innovations in Metal Fastener Technology?
You'll find that the latest innovations in metal fastener technology include smart fasteners and nanotechnology applications, offering enhanced control and reliability in your projects. These advancements ensure superior performance and adaptability.
Mikehardware-your trusted custom Metal Fasteners manufacturer
In conclusion, did you know that over 30% of equipment failures are linked to the improper selection of fasteners? It's vital to choose wisely. Consider the material, corrosion resistance, and mechanical properties that fit your budget.
Ensure your supplier is reliable, offers customization, and adheres to quality standards. Don't overlook the importance of lead times to keep your project on schedule.
Selecting the right fasteners isn't just a detail—it's a cornerstone of successful manufacturing.
At Dongguan Mike Hardware Co., Ltd., precision engineering meets innovation, delivering impeccable CNC product manufacturing solutions. Explore our array of customized fasteners, screws, and coatings, ensuring your projects excel in performance, precision, and quality.