Understanding Bolt Grades: A Comprehensive Guide for Custom Metal Hardware Manufacturers
In the landscape of custom metal hardware manufacturing, a comprehensive understanding of bolt grades is an essential aspect that can greatly influence the overall quality, durability, and safety of the final product. Bolt grades, often overlooked, serve as a critical determinant of the strength and resilience of the bolt, thereby directly impacting the robustness of the hardware it is used in.
This brief will explore the nuances of bolt grades, elucidate the importance of these classifications in manufacturing, and shed light on how to identify different bolt grade standards. As we navigate through these complex layers, we shall also decode the markings on bolt grades and illustrate their real-world applications - a journey that is bound to equip you with a deeper, more practical understanding of this fundamental component.
Key Takeaways
- Bolt grades play a critical role in determining the strength, durability, and safety of fastening systems in manufacturing processes.
- Manufacturers need to carefully consider the material selection and tensile strength requirements when choosing bolt grades to ensure optimal performance and longevity.
- International standards such as ASTM and ISO provide guidelines for identifying bolt grades through specific markings on the bolts, facilitating material compatibility and quality control.
- Different industries like automotive, aerospace, construction, and heavy machinery rely on specific bolt grades tailored to their application needs, emphasizing the importance of understanding and selecting the right grade for operational efficiency and safety.
Understanding the Basics of Bolt Grades
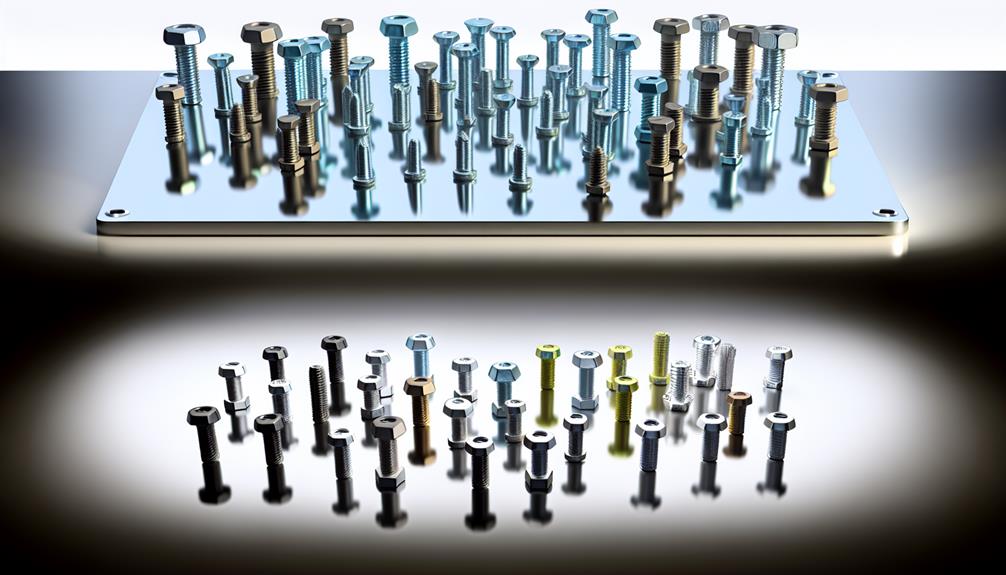
While it may seem trivial to some, understanding the basics of bolt grades is essential for any metal hardware manufacturer aiming for precision and durability in their products. The grade of a bolt reflects its strength, indicating its maximum load capacity. This is a vital factor in choosing the right bolt for a specific application.
Bolt strength is determined by two major factors: the yield strength and the tensile strength. The yield strength refers to the maximum stress that can be applied without causing permanent deformation, while the tensile strength is the maximum load a bolt can bear before breaking. A higher grade bolt will have a higher yield and tensile strength.
Material selection also plays a critical role in bolt grades. Different materials offer varying degrees of strength, hardness, and resistance to corrosion. For instance, stainless steel bolts are known for their corrosion resistance, while alloy steel bolts are noted for their high tensile strength.
Importance of Bolt Grades in Manufacturing
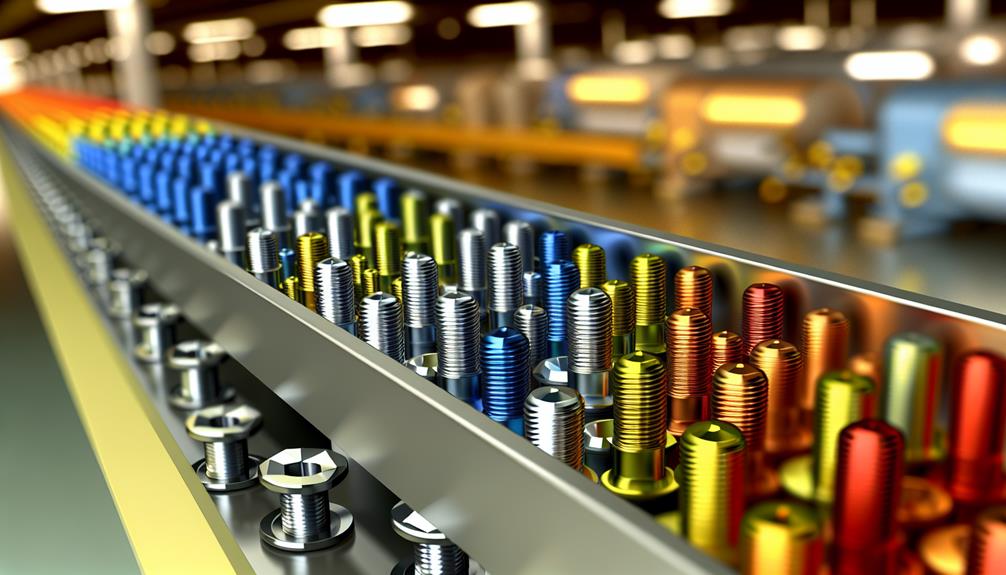
In the realm of manufacturing, the significance of bolt grades cannot be overstated, as they directly influence the durability, safety, and overall performance of the final product. Choosing the right bolt grade is a strategic decision, involving careful consideration of factors such as tensile strength, yield strength, and material compatibility.
The importance of bolt grades is highlighted in two specific areas:
- Bolt Longevity Importance
- The grade of a bolt impacts its lifespan. Higher-grade bolts often exhibit superior resistance to wear and tear, thereby reducing the frequency of replacements and maintenance work.
- This longevity leads to a more reliable and safe end product, whether it be machinery, buildings, or transportation vehicles.
- Manufacturing Cost Implications
- While higher-grade bolts may come at a higher initial cost, their extended lifespan often results in long-term cost savings.
- Lower-grade bolts, though cheaper upfront, may lead to increased costs in the long run due to frequent replacements and the potential for equipment failure.
Identifying Different Bolt Grade Standards
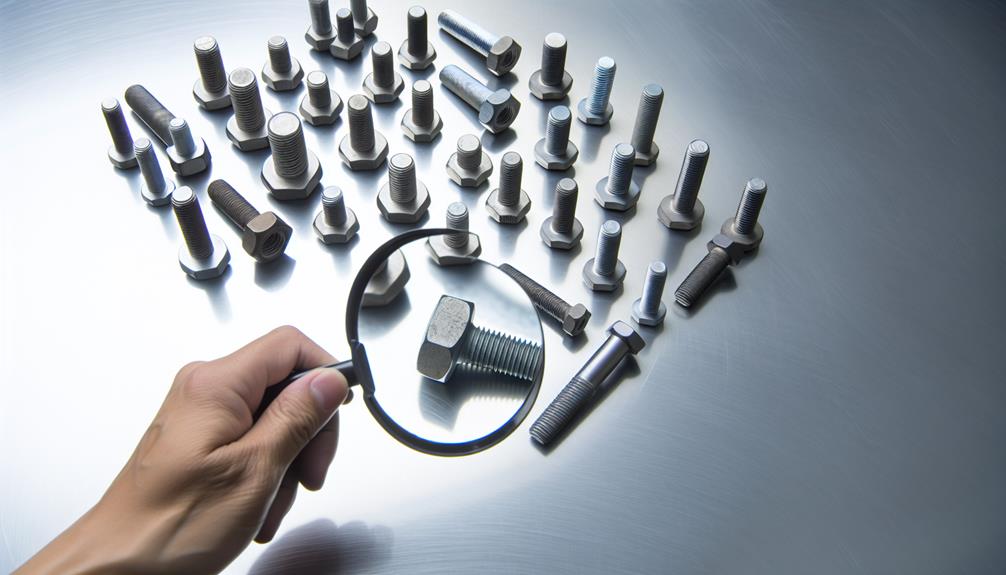
Given the critical role of bolt grades in manufacturing longevity and cost-effectiveness, understanding how to identify different bolt grade standards becomes an essential skill for manufacturers. It is imperative to comprehend how grade variations impact the quality, strength, and durability of bolts, ultimately affecting the manufacturing process and the final product.
International Bolt Standards, such as those set by the American Society for Testing and Materials (ASTM) or the International Organization for Standardization (ISO), provide a uniform measure for identifying bolt grades. These standards encompass parameters including material, mechanical properties, and testing methods, offering manufacturers a reliable reference point for bolt quality.
To identify bolt grades, manufacturers can look for markings on the bolt head. For instance, ASTM grades are usually marked as 'A' followed by a number, while ISO grades may be marked with numbers only. Understanding these markings is crucial for manufacturers, as selecting the wrong bolt grade may compromise the integrity of the product, causing potential safety risks and financial losses.
Decoding Markings on Bolt Grades
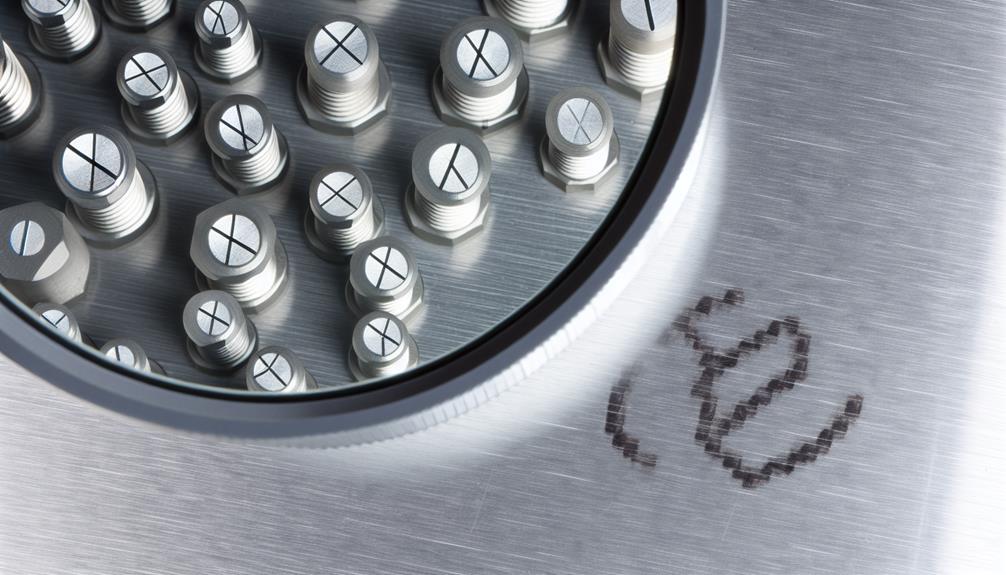
Deciphering the markings on bolt grades is a vital skill that bolsters the manufacturer's ability to ensure the use of appropriate hardware in their products. This marking interpretation can be seen as a form of bolt identification, serving as a key indicator of a bolt's strength, material, and other pertinent attributes.
Understanding these markings is essential for ensuring hardware quality, performance, and safety. Here's a brief breakdown to assist with bolt identification:
- Imperial Grade Bolts:
- Grade 2: No markings
- Grade 5: Three evenly spaced radial lines
- Grade 8: Six evenly spaced radial lines
- Metric Grade Bolts:
- 8.8: Medium carbon steel, quenched and tempered
- 10.9: Alloy steel, quenched and tempered
- 12.9: Alloy steel, quenched and tempered
These markings, while seemingly simple, hold significant meaning and can directly impact the success and safety of your manufacturing operations. Developing a deep understanding and proficiency in marking interpretation can empower your decision-making process, ultimately leading to superior product quality and customer satisfaction.
Real-World Applications of Bolt Grades
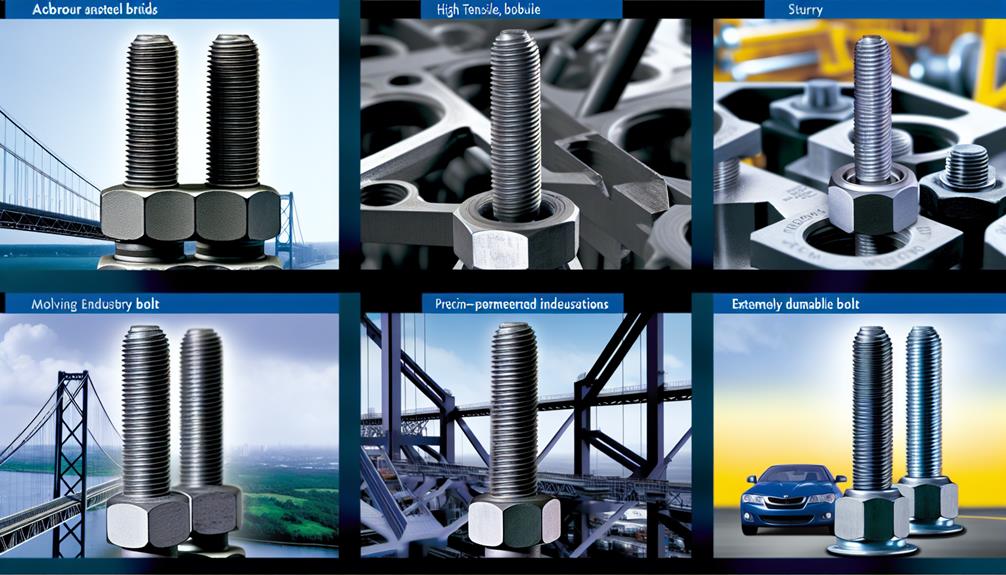
Drawing upon the knowledge of bolt grade identifications, we can now explore their various real-world applications in different manufacturing industries. Bolt grades, a critical determinant of bolt durability, play an indispensable role in a wide range of industrial processes. Concrete examples include the automotive, aerospace, construction, and heavy machinery sectors.
Bolt durability analysis is a crucial step in these industries, as it ensures the selection of the appropriate bolt grade that can withstand the operational stresses involved. For instance, grade 5 bolts may be favored in the automotive industry due to their optimal balance of strength and ductility. On the other hand, for heavy-duty applications such as construction of bridges or skyscrapers, higher-grade bolts (8.8 or 10.9) are typically utilized for their superior strength.
Industrial bolt usage is thus tailored to the specific requirements of each application. Varying conditions such as temperature, pressure, and corrosive environments necessitate the use of different bolt grades to maintain operational efficacy and safety. Therefore, understanding bolt grades and their applications help manufacturers to control product quality, optimize performance, and mitigate the risk of equipment failure.
Frequently Asked Questions
What Are the Common Mistakes Manufacturers Make When Choosing Bolt Grades?
Common mistakes manufacturers make when choosing bolt grades include neglecting bolt durability in favor of cost, and poor material selection resulting in inadequate resistance to wear and tear or environmental conditions.
How Does the Cost Factor Into the Selection of Bolt Grades for Custom Metal Hardware Manufacturers?
The cost significantly impacts bolt grade selection, balancing between bolt durability and material availability. Manufacturers must consider long-term value, not just initial expense, ensuring optimal performance and longevity of the custom metal hardware.
How Does the Manufacturing Process Differ Between Various Bolt Grades?
The manufacturing process for various bolt grades largely depends on material selection and bolt durability requirements. Higher grade bolts often require more complex manufacturing processes to ensure increased strength and longevity.
What Are Some Safety Considerations for Manufacturing and Using Different Bolt Grades?
Safety considerations entail ensuring bolt durability and implementing stringent quality control to prevent failures. Different bolt grades require specific handling, installation methods, and maintenance to avoid accidents and ensure operational safety.
Can Bolt Grades Affect the Sustainability or Environmental Impact of Manufacturing Processes?
Yes, bolt grades can significantly influence the sustainability and environmental impact of manufacturing processes. Grade Impact Analysis and Environmental Adaptability are key metrics for assessing these effects, leading to more responsible production methods.
Mikehardware-your trusted bespoke bolts manufacturer
In conclusion, understanding bolt grades remains paramount for custom metal hardware manufacturers. Differentiating bolt grade standards and decoding their markings ensures optimal use in various applications.
A case in point is the construction industry where high-grade bolts, like Grade 8, are essential for structural integrity. Thus, thorough knowledge of bolt grades significantly contributes to manufacturing quality, safety, and efficiency in real-world applications.
At Dongguan Mike Hardware Co., Ltd., precision engineering meets innovation, delivering impeccable CNC product manufacturing solutions. Explore our array of customized fasteners, screws, and coatings, ensuring your projects excel in performance, precision, and quality.