Custom Screws: Details You Should Know
Are you curious about the benefits of using custom screws? Look no further.
This article dives into the details you should know about these specialized fasteners. From learning about reliable custom screw manufacturers to exploring various types and product specifications, we've got you covered.
Discover industry standards, applications across different sectors, and insights into screw manufacturing.
With Mikehardware's exceptional screw machining capabilities and related manufacturing services, this article is a must-read for anyone seeking knowledge on custom screws.
Key Takeaways
- Custom screws provide a precise fit and compatibility with product components, improving overall performance and durability.
- Custom screws offer design flexibility, allowing for unique design needs and enhanced aesthetics with visually appealing finishes.
- Dongguan Mike Hardware Co., Ltd. is a reputable custom screw manufacturer with industry expertise, cutting-edge facilities, and comprehensive one-stop production solutions.
- Custom screws have various applications in industries such as electronics, woodworking, construction, automotive, and medical, catering to specific needs in each sector.
1.The Benefits of Using Custom Screws
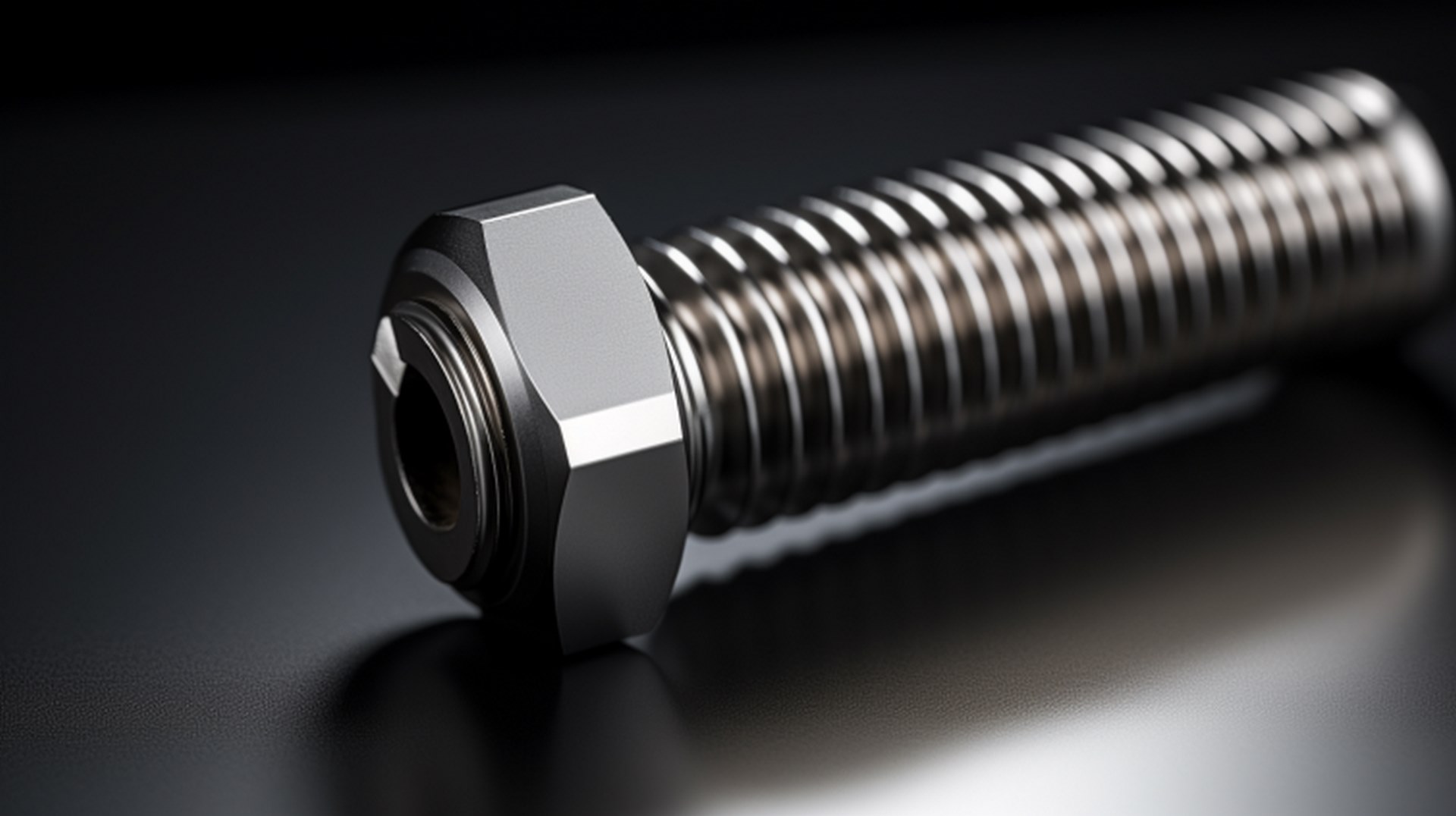
The benefits of using custom screws include a precise fit, design flexibility, improved aesthetics, enhanced performance and durability, streamlined assembly process, and intellectual property protection.
Custom screws provide a precise fit and compatibility with product components, ensuring a perfect match for specific design requirements. This eliminates the risk of loose connections or assembly errors, enhancing the overall quality and performance of the product.
Designers also enjoy unparalleled design flexibility with custom screws. They can be tailored to meet unique design needs in terms of material choice, length, diameter, or thread type. This allows designers to optimize screw designs for specific applications and enhance functionality and reliability.
Furthermore, custom screws contribute to improved aesthetics by offering designers the freedom to choose finishes that complement the overall design of the product. By selecting visually appealing screw finishes such as stainless steel or brass, designers can make their products more attractive to consumers.
In addition to aesthetics, custom screws can improve performance and durability by being engineered with appropriate materials like titanium or hardened steel that can withstand heavy loads or resist corrosion.
Custom screws also streamline the assembly process through innovative features like captive washers or integrated locking mechanisms that reduce time and effort required for assembly. Moreover, they play a crucial role in protecting intellectual property by using unique designs that prevent unauthorized access or reverse engineering.
To take advantage of these benefits in product design processes requires collaboration with reliable custom screw manufacturers who possess advanced manufacturing capabilities…
2.Custom Screw Manufacturer
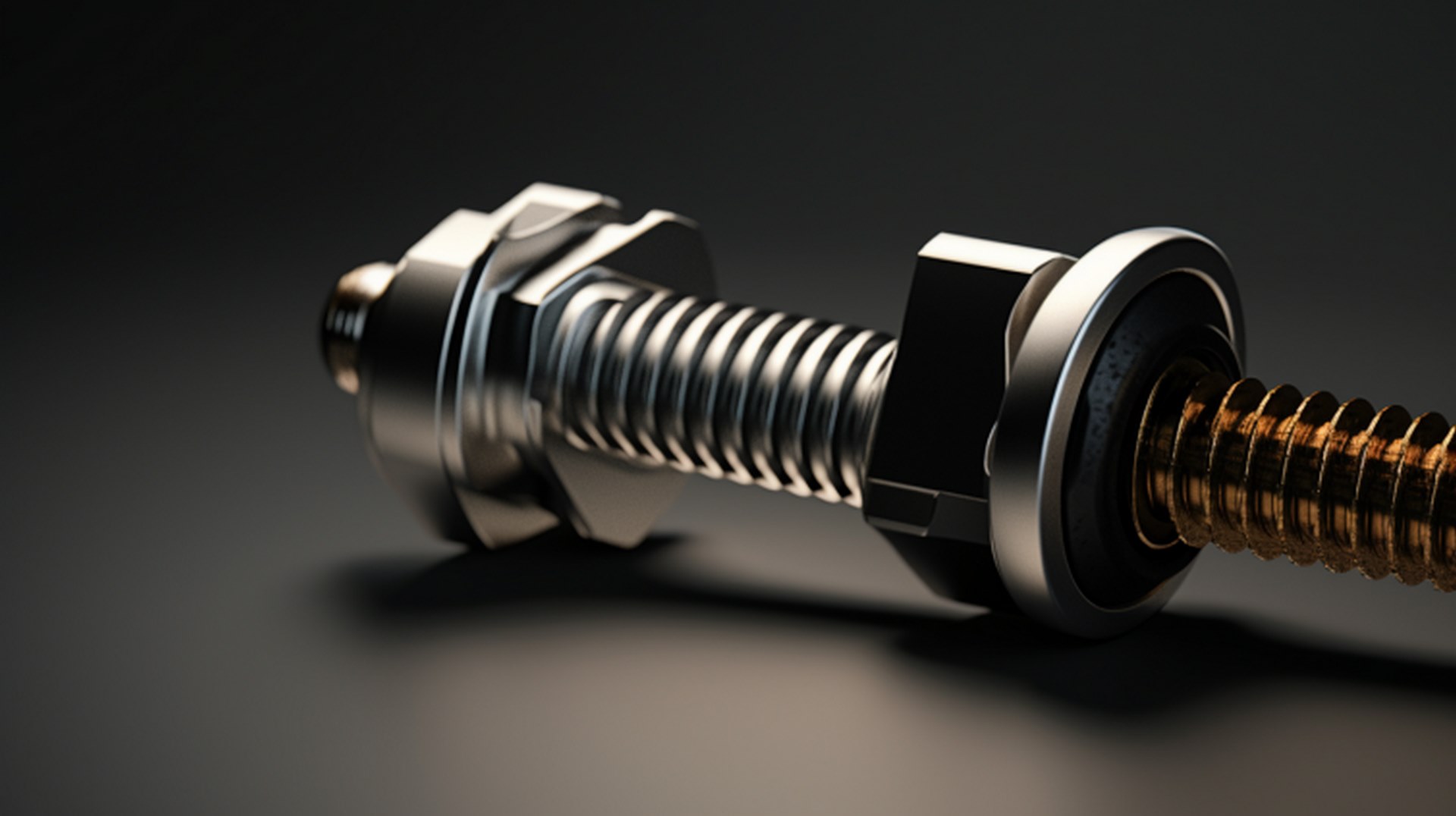
When looking for a custom screw manufacturer, consider Dongguan Mike Hardware Co., Ltd. With over a decade of experience and a team of skilled professionals, they offer comprehensive one-stop production solutions for CNC product manufacturing.
Here are three reasons why you should choose Dongguan Mike Hardware:
- Industry Expertise: Backed by 15 experienced mold designers and advanced 2D and 3D technology, they provide personalized project follow-up with an impressive 98% product completion rate. Their mold manufacturing team offers tailored support and quick mold openings in just 2-7 days, ensuring cost savings without compromising quality.
- Cutting-Edge Facilities: Dongguan Mike Hardware's state-of-the-art facility is home to more than 350 proficient operators, ensuring seamless execution of projects. They specialize in offering one-stop fastener solutions, including special coating fasteners, standard material fasteners, special application fasteners, and CNC/machining parts.
- Commitment to Excellence: Dongguan Mike Hardware is known for their unwavering commitment to excellence. They prioritize precision, efficiency, and professionalism in all aspects of CNC product manufacturing.
Now that you know why Dongguan Mike Hardware is the ideal custom screw manufacturer, let's explore the different types of custom screws they offer.
3.Types of Custom Screws

When it comes to custom screws, there are several different types to consider. Some of these include the micro screw, wooden screw, slotted screw, concrete screw, and thumb screw.
Each type has its own unique characteristics and uses in various applications.
In this discussion, we will explore these key points in more detail to better understand the differences and benefits of each type of custom screw.
Micro Screw
Don't overlook the benefits of using a micro screw for your specific project needs. These tiny screws have become increasingly popular due to their versatility and precision. Here are three reasons why you should consider using a micro screw:
- Size: Micro screws are incredibly small, typically ranging from 1mm to 3mm in diameter. This makes them perfect for projects that require delicate and intricate work, such as electronics or jewelry making.
- Strength: Despite their size, micro screws are surprisingly strong and durable. They can securely fasten materials together without compromising the integrity of the project.
- Accessibility: Micro screws are widely available and come in various lengths, thread types, and head styles. This means you can easily find the right screw to meet your specific requirements.
Wooden Screw
If you're looking for a traditional and reliable option, consider using a wooden screw for your woodworking projects. Wooden screws have been used for centuries and offer several advantages over other types of screws. They are easy to work with, as they can be easily cut and shaped to fit specific needs. Additionally, wooden screws provide excellent grip and holding power due to the natural properties of wood.
Wooden screws are versatile and can be used in various woodworking applications, from furniture making to cabinetry. Transitioning into the next section about slotted screws, it's important to note that they also have a long history of usage in woodworking projects.
Slotted Screw
Slotted screws are commonly used in woodworking projects because they allow for easy adjustment and tightening. They have a single groove running across the top of the screw head, which can be easily turned using a flat-bladed screwdriver.
Here are three reasons why slotted screws are popular in woodworking:
- Easy identification: Slotted screws are recognizable due to their distinctive slot shape, making them readily identifiable among other types of screws.
- Versatility: These screws come in various sizes and lengths, making them suitable for different woodworking applications.
- Reusability: Slotted screws can be easily removed and reused multiple times without compromising their performance or integrity.
Concrete Screw
When working with concrete, it's important to choose the right type of fastener for the job. Concrete screws are specifically designed to securely attach objects to concrete surfaces. These screws have a unique thread pattern that provides excellent grip in the hard material. They also feature a hardened steel construction, ensuring durability and strength.
Concrete screws can be easily installed using a power drill or impact driver, making them convenient for both professional contractors and DIY enthusiasts.
Now, let's move on to another type of custom screw: the thumb screw. Unlike traditional screws that require tools for tightening or loosening, thumb screws have a specially-designed head that can be tightened or loosened by hand with just your thumb and fingers, providing quick and easy adjustments in various applications.
Thumb Screw
To adjust a thumb screw, simply use your thumb and fingers to tighten or loosen it by hand. Thumb screws are designed to be easily adjusted without the need for tools, making them convenient for quick adjustments or temporary fixes.
Here are three key points about thumb screws:
- Versatility: Thumb screws come in various sizes and styles, allowing them to be used in a wide range of applications. From securing panels or covers on electronic devices to adjusting settings on machinery, they offer flexibility.
- Grip: The design of thumb screws typically includes ridges or knurling on the head, providing a better grip when turning by hand. This ensures that users can easily apply enough force to tighten or loosen the screw as needed.
- Quick Release: Some thumb screws have a quick-release feature that allows for rapid removal without fully unscrewing the entire screw. This makes them ideal for situations where frequent access is required.
It's important to note that while thumb screws are convenient for manual adjustments, machine screws provide more secure fastening solutions using tools such as wrenches or screwdrivers.
Machine Screw
Machine screws are typically used in applications where a more secure fastening method is required, such as construction or machinery. These screws have a uniform diameter and are threaded along the entire length of their shafts. They require pre-tapped holes or nuts to hold them in place securely.
Machine screws come in various sizes, lengths, and materials to accommodate different needs. However, for certain situations where tapping a hole beforehand may not be feasible or efficient, self-tapping screws offer a convenient alternative. These innovative screws have specially designed threads that allow them to create their own mating threads when driven into a material without the need for pre-drilled holes or nuts.
This makes self-tapping screws ideal for quick installations and repairs in various industries.
Self-tapping Screw
Self-tapping screws are commonly used in applications where pre-drilled holes or nuts may not be feasible or efficient. These versatile fasteners have a unique design that allows them to create their own threads as they are driven into a material, eliminating the need for tapping or drilling beforehand.
Here are three key reasons why self-tapping screws are favored in various industries:
- Time and cost-efficient: Self-tapping screws eliminate the need for additional tools or steps, saving time and reducing production costs.
- Versatility: They can be used with different materials like metal, wood, plastic, and even drywall.
- Strong hold: The self-threading action creates a secure bond between the screw and the material, ensuring a strong and durable connection.
With these benefits in mind, it's important to consider specific product specifications when choosing self-tapping screws for your project requirements.
Related Article: Custom Screw: Types of Set Screw
4.Product Specifications
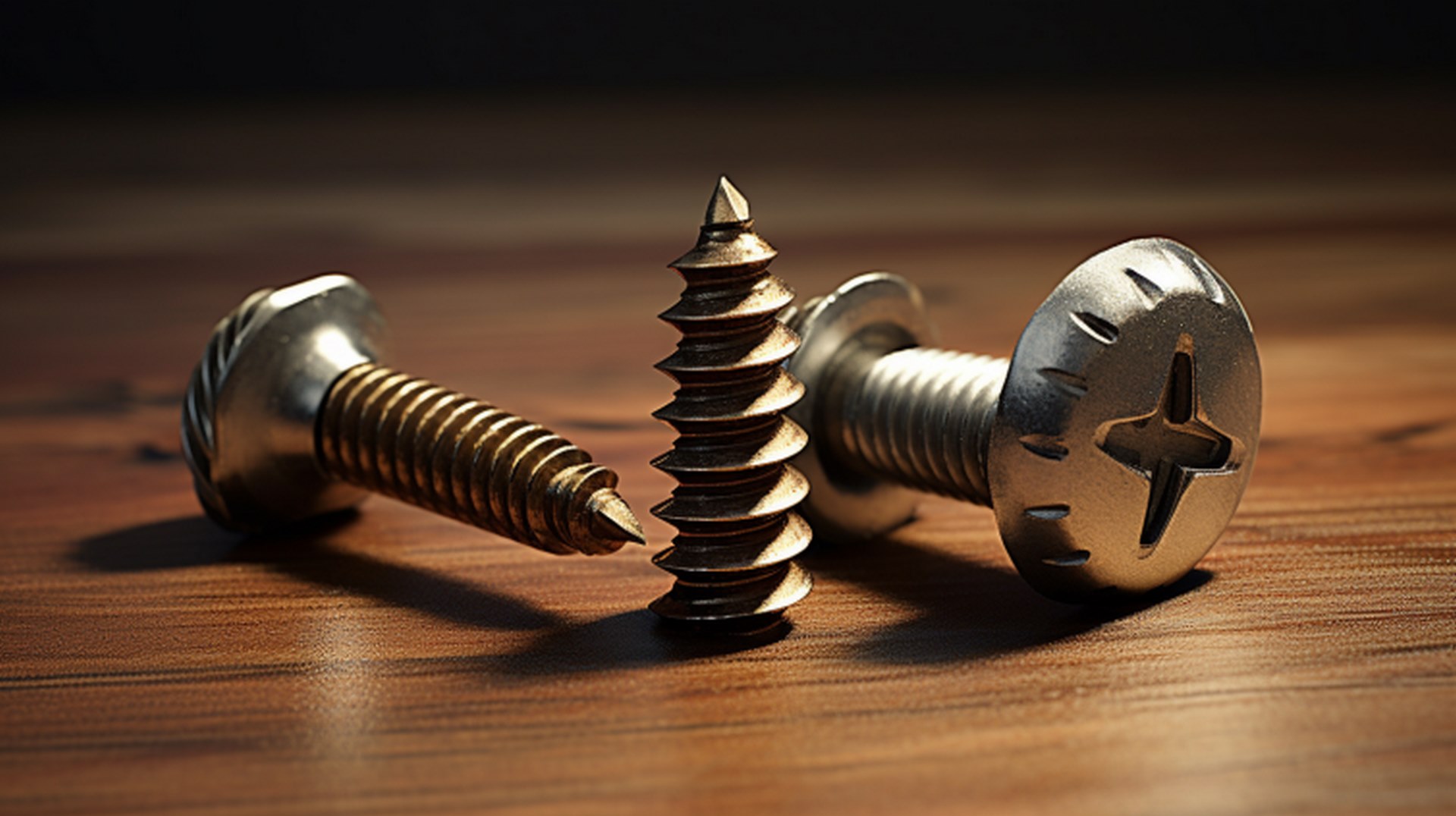
When it comes to product specifications for custom screws, there are several key points to consider.
First and foremost, the screw head style plays a crucial role in determining its functionality and compatibility with different applications.
Additionally, the quality of materials used in manufacturing the screws greatly impacts their durability and performance.
Alongside this, finishes can provide added protection against corrosion or enhance the aesthetic appeal of the screws.
Furthermore, size is an important factor to take into account as it determines how well the screw fits into a specific application.
To help users easily navigate through these specifications, a table summarizing all the necessary details can be provided for quick reference.
Screw Head Styles
If you're looking for custom screws, one thing you should know is the different styles of screw heads. Understanding these styles will help you choose the right screw for your specific needs.
Here are three common screw head styles:
- Flathead: Also known as slotted screws, these have a single straight slot on top for a flathead screwdriver. They are easy to use but can slip out of the slot easily.
- Phillips: These screws have a cross-shaped indentation on top and require a Phillips screwdriver. They provide better torque transfer and are less likely to slip compared to flathead screws.
- Hex: Hex head screws have six-sided heads that require an Allen wrench or hex key for installation. They offer increased stability and can handle higher torque applications.
Understanding the different screw head styles allows you to select the most appropriate option for your project's requirements.
Related Article: Flat Socket Head Screws: Key Considerations for Custom Manufacturing
Quality Materials
After understanding the different screw head styles, it is crucial to consider the quality materials used in custom screws. The choice of material greatly impacts the overall performance and durability of the screws.
Manufacturers often use various types of metals like stainless steel, brass, or aluminum for their custom screws. Stainless steel is a popular option due to its corrosion resistance and strength. Brass offers excellent electrical conductivity and is commonly used in electronic applications. Aluminum is lightweight and ideal for applications that require reduced weight.
Each material has its own unique properties that make it suitable for specific uses. By selecting the right material, customers can ensure that their custom screws will meet their desired requirements.
Finishes
Let's explore the different finishes used on custom screws to enhance their appearance and provide added protection.
Custom screws can be finished in various ways to suit different applications and aesthetic preferences. Here are three common finishes used on custom screws:
- Zinc Plating: This finish involves coating the screw with a layer of zinc, which provides excellent corrosion resistance. It also gives the screw a shiny appearance.
- Black Oxide: This finish creates a dark, matte black surface on the screw. It not only enhances the visual appeal but also provides some degree of corrosion resistance.
- Passivation: This finish is commonly used for stainless steel screws. It removes any impurities from the surface and forms a protective oxide layer that prevents rusting.
Size
After considering the different finishes available for custom screws, it's important to think about the size of the screws you need. Size plays a crucial role in ensuring that the screws fit perfectly into your project. Custom screws can come in various sizes, ranging from tiny ones used for delicate electronics to large ones for heavy-duty construction projects.
It is essential to carefully measure and determine the appropriate size of screws required for your specific application. This will ensure optimal functionality and structural integrity. To make this process easier, many manufacturers provide a table for product specifications. This table outlines all the necessary details, such as screw length, diameter, thread pitch, and head type.
5. Industry Standards
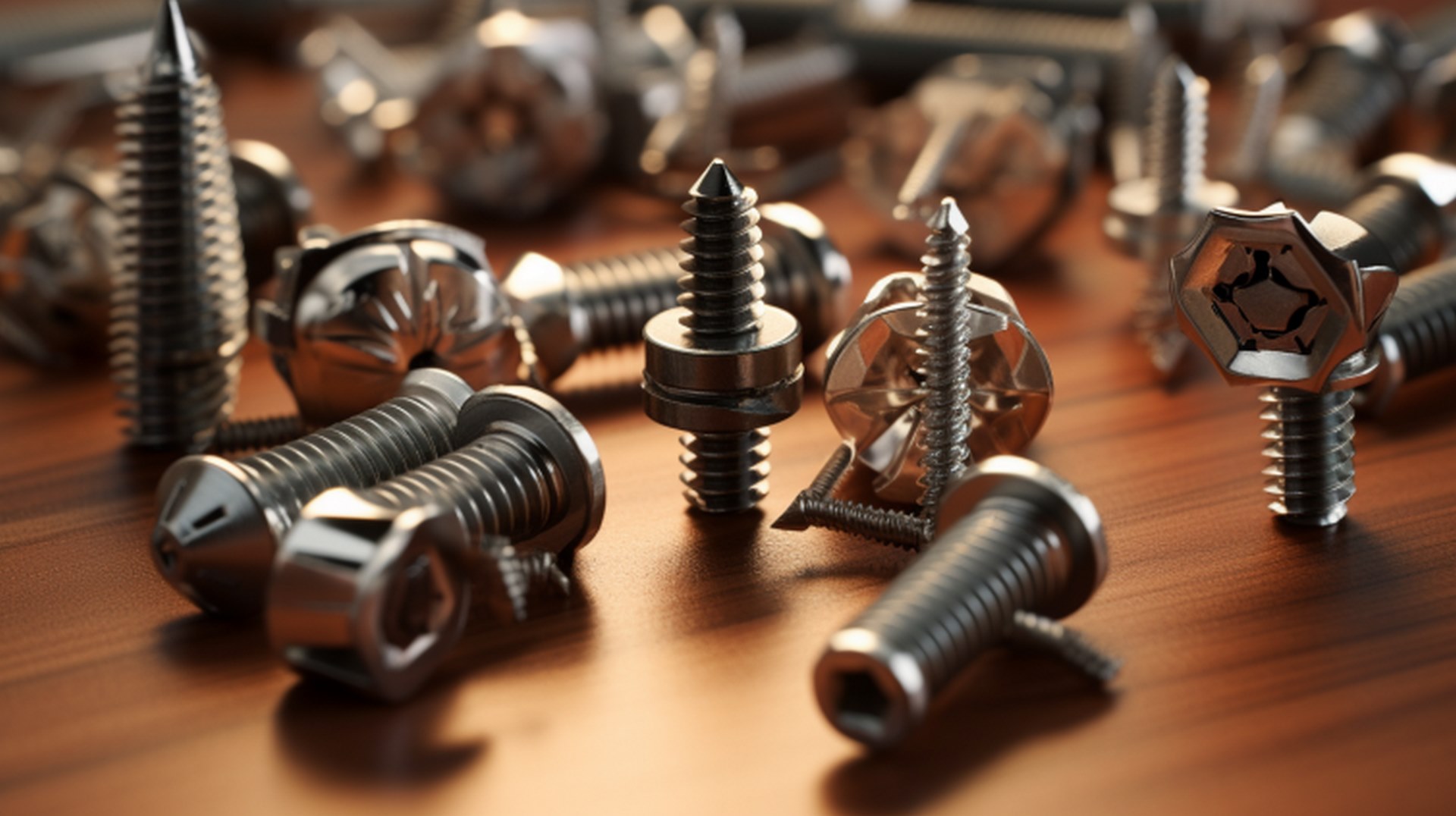
There's a reason why industry standards for custom screws are so important. These standards ensure that the screws meet specific requirements and are compatible with various applications across different industries. Custom screws play a crucial role in many sectors, from aerospace and automotive to electronics and construction.
In the aerospace industry, custom screws must withstand extreme conditions, such as high temperatures and vibrations. They need to be lightweight but also durable enough to handle the stress placed upon them during flight.
Automotive manufacturers rely on custom screws for assembling components like engines, transmissions, and chassis systems. These screws need to be reliable, efficient, and able to withstand constant movement.
The electronics industry requires custom screws that are small yet precise. They are used in devices like smartphones, laptops, and cameras where space is limited but accuracy is crucial.
Construction companies use custom screws for various applications such as securing beams or fastening materials together.
As we can see, different industries have unique requirements when it comes to custom screws. Understanding these needs allows manufacturers to produce specialized products that meet specific industry standards while ensuring optimum performance in their respective applications.
6. Industries & Applications
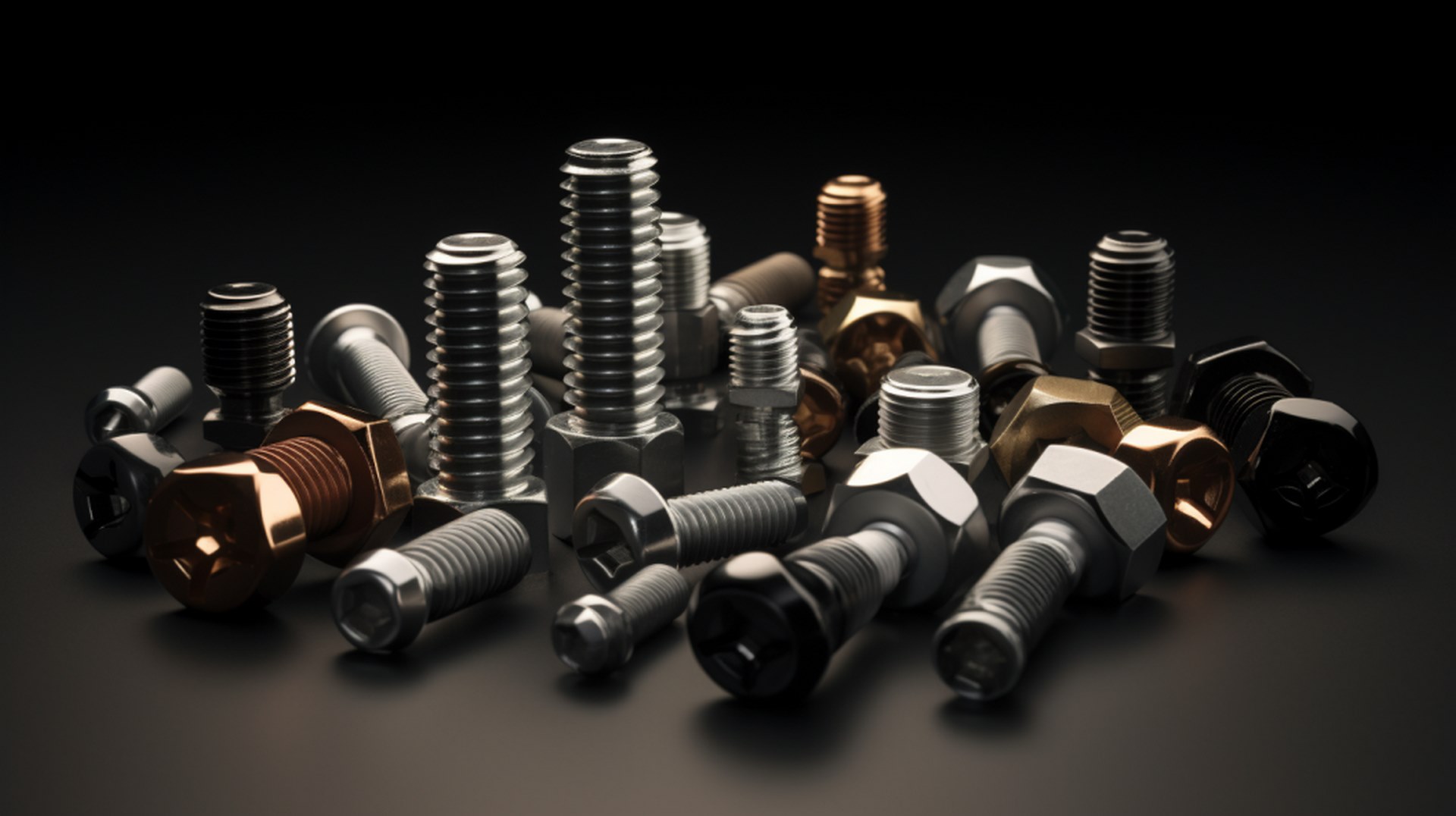
In various industries, custom screws are essential for specific applications and play a significant role in ensuring optimum performance. These specialized screws are designed to meet the unique requirements of different industries and applications, providing the necessary strength, durability, and functionality needed for specific tasks.
Here are three key industries where custom screws are widely used:
- Automotive industry: Custom screws find extensive use in car manufacturing processes, where they secure various components such as engines, chassis parts, interior trim panels, and electrical systems. These screws are engineered to withstand high levels of vibration and provide reliable fastening solutions.
- Aerospace industry: In the aerospace sector, precision is paramount. Custom screws are used to assemble aircraft structures, engines, landing gears, and avionics equipment. They must meet strict quality standards and be able to withstand extreme temperature variations while maintaining their integrity.
- Medical industry: Custom screws play a vital role in medical devices and implants. They are used to secure orthopedic implants like plates or prosthetic joints during surgeries or dental procedures like implant placements. These screws need to be biocompatible, corrosion-resistant, and capable of providing long-lasting stability.
It is important to understand how these custom screws are produced with precision engineering techniques that ensure their high quality and reliability without compromising on performance or safety.
Related Article: Trim Screws VS Nails
7. Screw Manufacturing
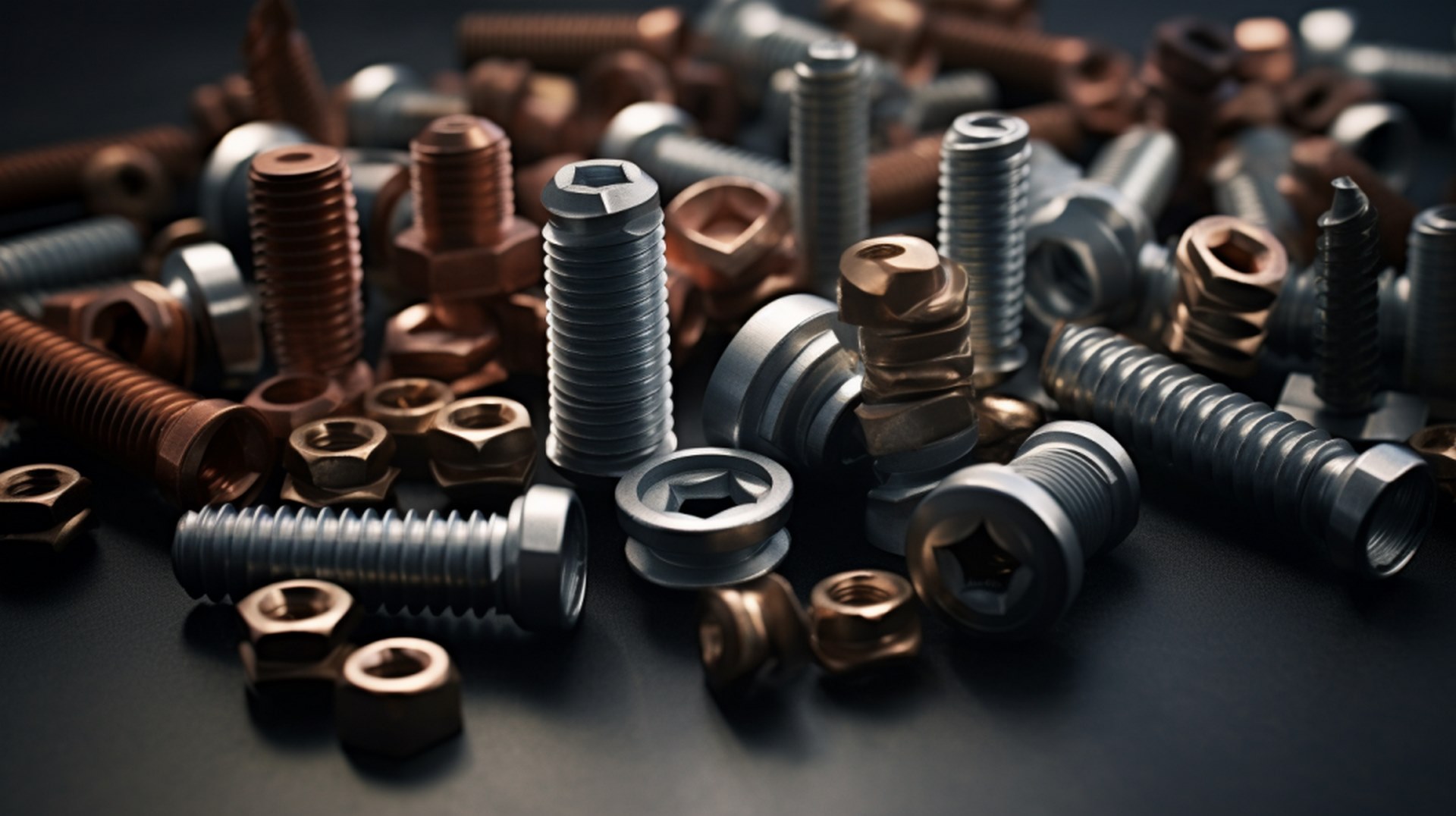
To understand the process of screw manufacturing, you'll need to be aware of the various steps involved in creating these essential components.
It all begins with the selection of materials. Depending on the specific requirements and applications, screws can be made from a variety of metals such as stainless steel, brass, or aluminum.
Once the material is chosen, it goes through a series of machining processes. This includes cutting and shaping the material into the desired shape and size.
Afterward, threads are added to the screw using thread rolling or cutting techniques. This step is crucial as it determines how well the screw will fit into its corresponding nut or hole.
The next stage involves heat treatment to increase the strength and durability of the screw.
Finally, quality control measures are taken to ensure that each screw meets specific standards and requirements. This may involve testing for strength, dimensional accuracy, surface finish, and corrosion resistance.
Now that you have an understanding of screw manufacturing processes, let's delve into mikehardware's screw machining capabilities.
8. Mikehardware Screw Machining Capabilities
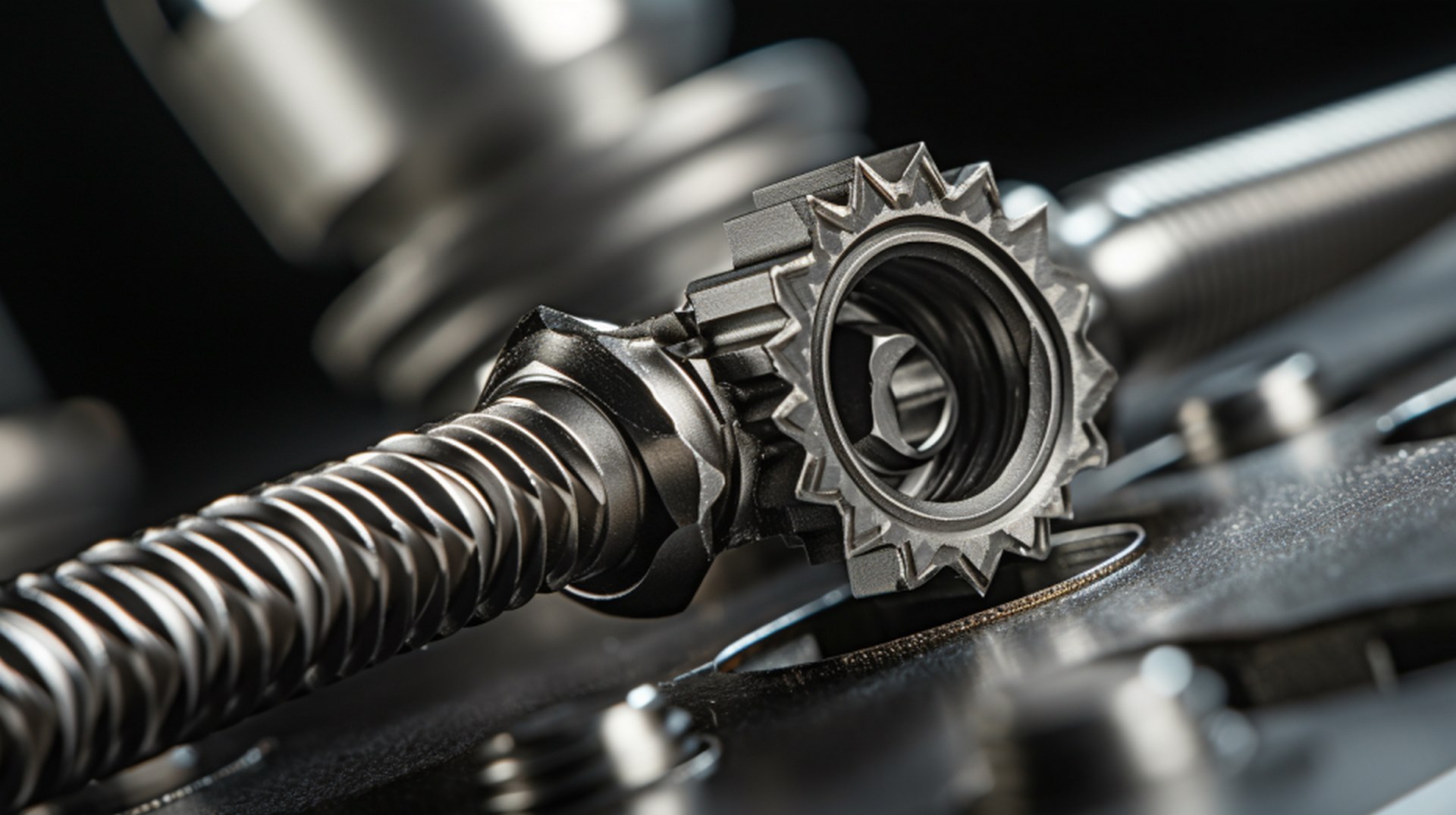
Mikehardware offers a wide range of screw machining capabilities to meet various customer needs.
With their state-of-the-art equipment and skilled machinists, they are able to produce high-quality screws with precision and efficiency.
From standard screws to custom designs, Mikehardware has the expertise and resources to deliver reliable products that meet industry standards.
Screw Manufacturing Capabilities | CNC Machining, Metal Processing, Metal Forming, Welding & Joining, Handling & Logistics, Air & Compressor Systems |
Quality Material | Brass, Silicon Brass, Steel, Low & Medium Carbon, Stainless Steel, Other Specialty Materials |
Industries | Motion Control/Instrumentation, Medical, Dental, Defense, Electronic, Automotive, Sporting Goods, Consumer Goods |
From their exceptional Screw Machining capabilities to related manufacturing services like CNC turning and milling, Mikehardware provides comprehensive solutions for all your custom screw manufacturing needs.
9. Related Manufacturing Services
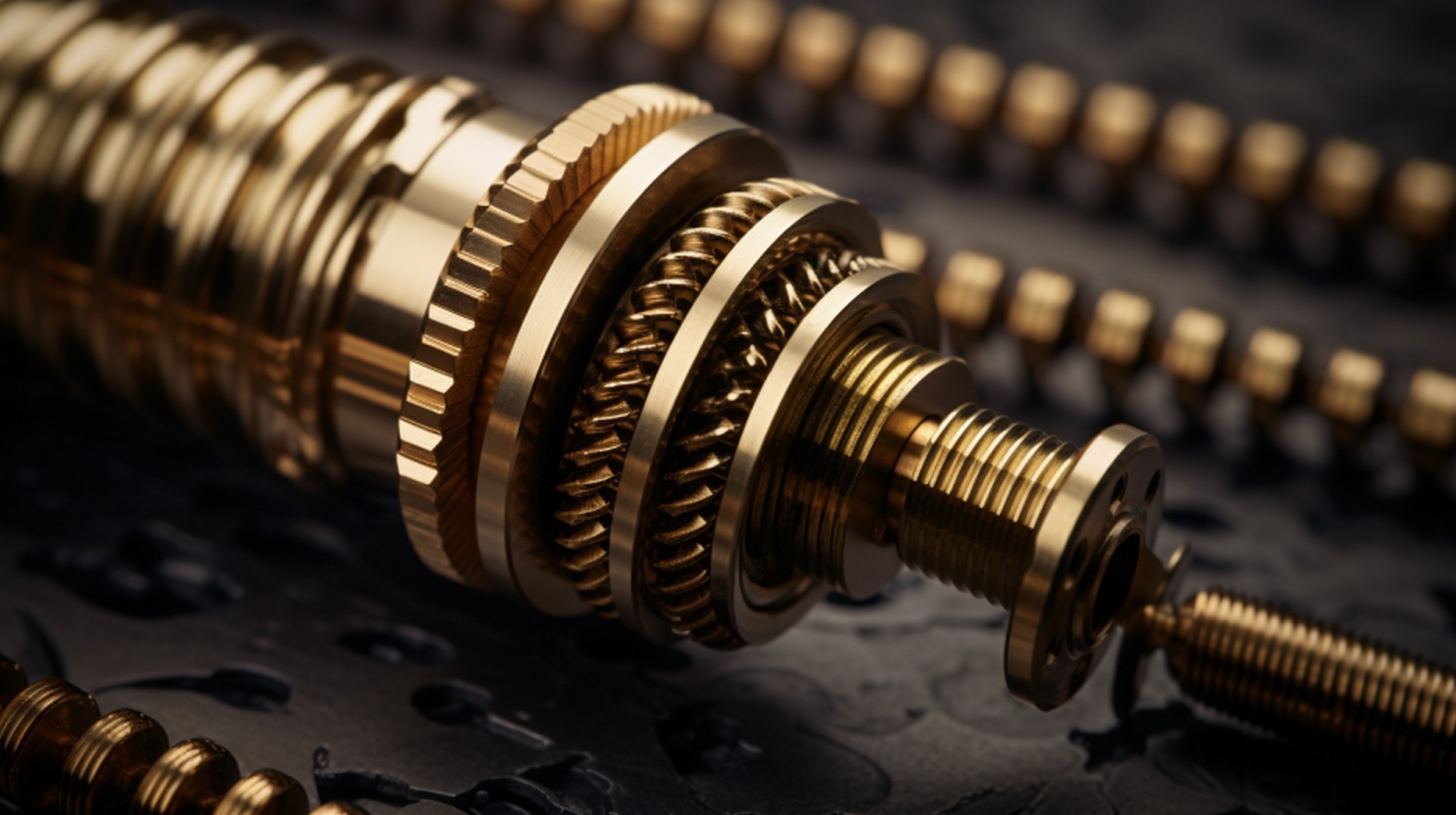
When it comes to related manufacturing services, you'll find a range of options available for custom screws. These services go beyond just the production of screws and offer additional solutions that cater to specific needs.
One option is screw finishing services, which involve adding coatings or finishes to the screws to enhance their performance and durability. This can include processes such as plating, painting, or heat treating.
Another service commonly offered is screw design assistance. Manufacturers have expertise in designing screws that meet specific requirements and can provide valuable input on factors such as material selection, thread design, and head style. This ensures that the custom screws are optimized for their intended application.
Additionally, some manufacturers offer secondary operations like threading or slotting services. These operations allow for further customization of the screws to fit unique assembly needs.
Furthermore, many manufacturing companies provide prototyping services for custom screws. This allows customers to test and evaluate different designs before proceeding with full-scale production.
Overall, these related manufacturing services give customers a comprehensive solution when it comes to custom screws. Whether it's finishing, design assistance, secondary operations, or prototyping - manufacturers offer a wide range of options to meet diverse requirements.
Related Article: Custom Screws And Bolts
Mikehardware-your trusted Custom Screw manufacturer
In conclusion, custom screws offer numerous benefits for various industries and applications. With the help of a reliable custom screw manufacturer like Mikehardware, businesses can ensure precise product specifications and adherence to industry standards.
The manufacturing capabilities of Mikehardware Screw Machining are top-notch, providing high-quality custom screws that meet specific requirements. Just like a well-oiled machine, custom screws from Mikehardware fit seamlessly into any project, making them an essential tool in the world of manufacturing.
At Dongguan Mike Hardware Co., Ltd., precision engineering meets innovation, delivering impeccable CNC product manufacturing solutions. Explore our array of customized fasteners, screws, and coatings, ensuring your projects excel in performance, precision, and quality.