Custom Screw: Types of Set Screw
Set screws, a small yet crucial component in the realm of fastening mechanisms, play a significant role in various applications. From securing pulleys on shafts to locking components in place, set screws offer a versatile solution for many engineering challenges.
However, not all set screws are created equal, as different types cater to specific needs and requirements. Understanding the nuances of these various set screw types can make a substantial difference in the efficiency and effectiveness of your projects.
Key Takeaways
- Set screws come in various types such as flat point, domed point, cone point, cup point, and extended point, each with specific advantages and applications.
- Different socket types like square socket, external hex, external square, and Bristol spline offer unique features for secure fastening and torque transmission.
- Set screws play a crucial role in applications like automotive assembly, electronic devices, precision machinery, medical equipment, and aerospace, ensuring stability, precise alignment, and reliability.
- Proper installation and maintenance of set screws are essential to prevent corrosion, maintain tension, prevent damage, and ensure long-lasting performance of equipment.
1. What Is a Set Screw?
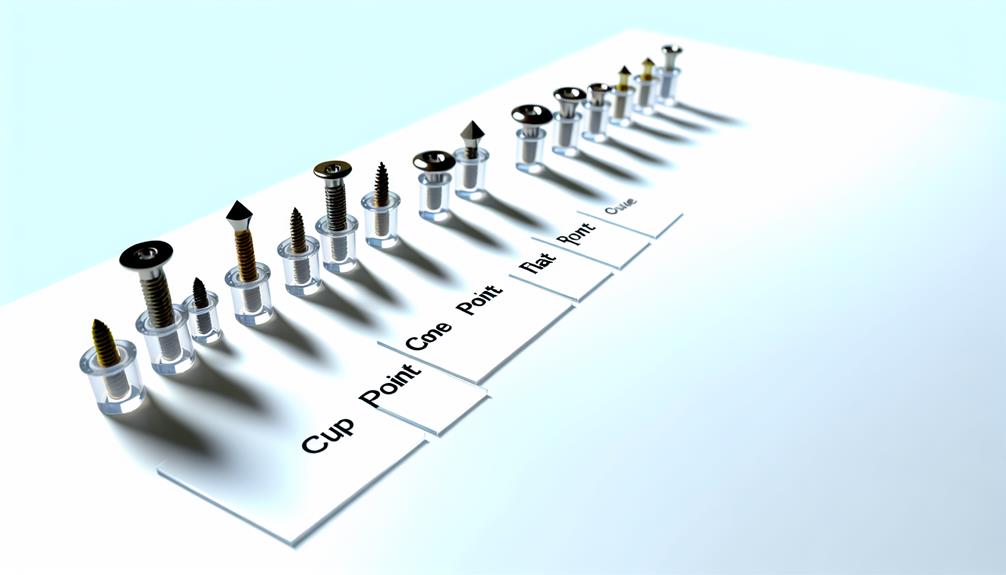
Set screws, also known as setscrews, socket set screws, or grub screws, are threaded fasteners primarily utilized for securely affixing components in place. One advantage of using set screws is their ability to hold parts together without the need for a nut, making them ideal for applications where space is limited. However, a disadvantage is that they can easily strip the threads of softer materials if over-tightened.
When it comes to installation tips, ensure that the set screw is aligned properly with the threaded hole to prevent any misalignment issues. Regular maintenance techniques include checking for any signs of wear or corrosion to prevent loosening over time.
Set screws are available in various materials such as stainless steel, alloy steel, and brass, allowing for customization based on the specific application requirements. Customization options also extend to different tip designs, including flat-ended and cone-point set screws, catering to a wide range of fastening needs.
2. How do set screws work?
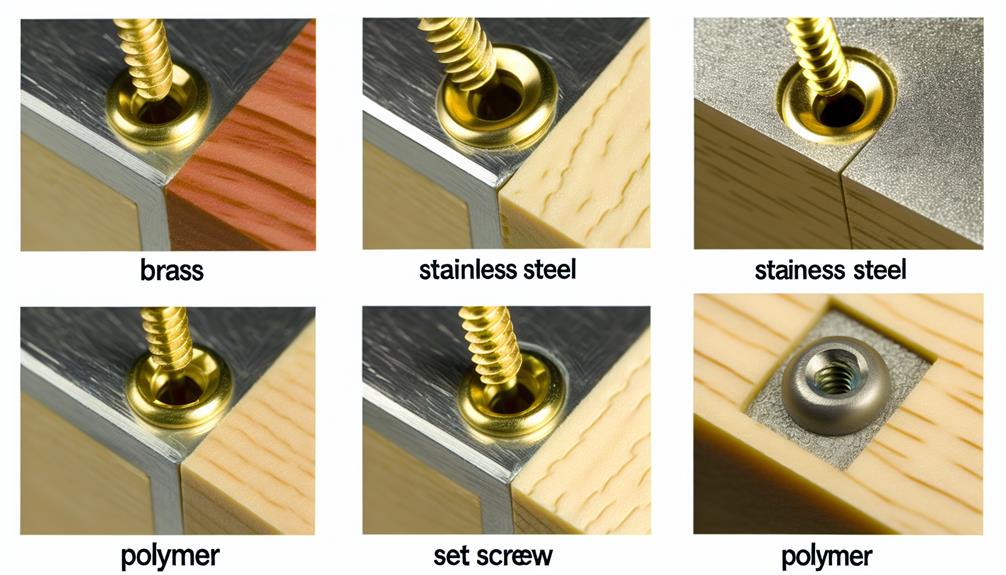
Utilizing threaded fastening technology, set screws function by exerting pressure against a surface to securely affix components in place. Understanding how set screws work involves considering several crucial factors:
- Torque Requirements: Set screws require a specific amount of torque to ensure proper fastening without damaging the components. It is essential to follow manufacturer guidelines to prevent under or over-tightening.
- Material Compatibility: Choosing the right set screw material is vital to prevent issues like galvanic corrosion. Match the set screw material with the components it will be fastening for optimal compatibility.
- Thread Engagement: Sufficient thread engagement is necessary for the set screw to hold securely. Ensuring that the set screw fully engages with the threaded hole is crucial for stability.
- Removal Process: When it's time to disassemble components, the removal process of set screws should be straightforward and not cause damage. Using the correct tools and techniques is key to a smooth disassembly process.
- Anti-Corrosion Properties: Set screws with anti-corrosion properties can prolong their lifespan and prevent seizing, especially in harsh environments. Choosing set screws with suitable coatings or materials can enhance their resistance to corrosion.
3. What are set screws used for
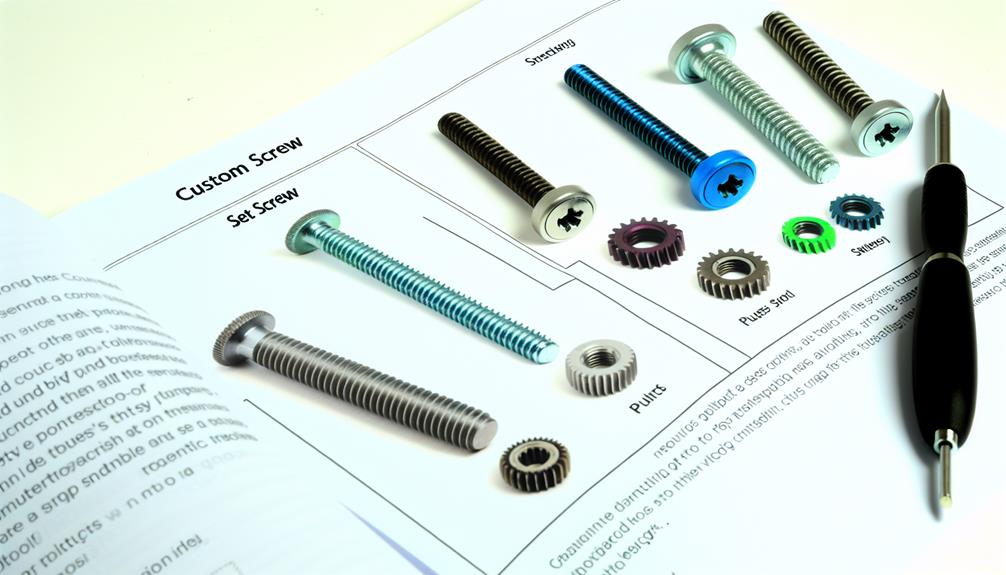
Set screws find wide application in various industries such as automotive assembly, electronic devices, precision machinery, medical equipment, and aerospace. These small but crucial components play a significant role in securely fastening different parts together in these industries.
From ensuring the alignment of components in precision machinery to providing stability in aerospace applications, set screws contribute to the functionality and reliability of diverse equipment and devices.
Automotive Assembly
Within automotive assembly, these small but critical components provide secure fastening solutions for various parts and components, ensuring structural integrity and reliability. Set screws play a crucial role in automotive applications due to their ability to withstand high torque and vibrations.
Key considerations for using set screws in automotive assembly include:
- Custom Finishes: Set screws can be customized with specific coatings or finishes to enhance their appearance or provide extra protection.
- Torque Specifications: Ensuring that set screws are tightened to the correct torque specifications is essential to prevent loosening or over-tightening.
- Thread Compatibility: Selecting set screws with the right thread type and size is crucial for proper alignment and secure fastening.
- Corrosion Resistance: Set screws with corrosion-resistant materials or coatings are vital to withstand harsh automotive environments.
Proper installation techniques are crucial to maximize the effectiveness of set screws in automotive assembly.
Electronic Devices
In modern electronic devices, set screws serve as essential fastening components that ensure the stability and secure assembly of intricate parts and components. Their precise design and application are crucial for device compatibility, enabling seamless integration within circuits.
Set screws play a vital role in precise component placement, guaranteeing optimal functionality and performance. By securely fastening components, they help minimize signal interference, ensuring reliable communication within the device.
Moreover, set screws contribute to efficient power consumption by maintaining the structural integrity of the device, reducing energy loss due to loose connections. In electronic devices, the strategic use of set screws is imperative for achieving reliability, stability, and optimal performance.
Precision Machinery
Precision machinery relies on the meticulous application of set screws to ensure the precise alignment and secure fastening of intricate components, building upon the critical role these fastening components play in electronic devices. Set screws are vital in the realm of precision machinery due to their ability to uphold high tolerance levels and facilitate the assembly of custom-fabricated parts.
In the domain of micro machining, set screws act as the linchpin, holding together minuscule yet crucial elements with steadfast reliability. Quality control in precision machinery heavily depends on the correct usage of set screws, ensuring that precision components are securely fastened to guarantee seamless operation.
Overall, the application of set screws in precision machinery underscores the importance of attention to detail and meticulous execution.
Key Aspects:
- Precision components
- High tolerance
- Custom fabrication
- Micro machining
Medical Equipment
Set screws serve a crucial role in the assembly and functionality of various medical equipment, contributing to the precise alignment and secure fastening of critical components.
In the realm of healthcare technology, these screws are utilized in surgical tools, hospital equipment, and medical devices. Set screws ensure that instruments used in the operating room are securely held together, preventing any potential mishaps during critical procedures.
Whether it's securing components in medical devices or holding together intricate surgical tools, the reliability and precision of set screws are paramount in maintaining the integrity and functionality of medical equipment.
The use of set screws in medical applications underscores the importance of meticulous engineering and quality control in the healthcare industry.
Aerospace Applications
Set screws play a crucial role in aerospace applications, contributing to the secure fastening and alignment of essential components in aircraft and spacecraft. When it comes to aerospace applications, the use of set screws requires meticulous attention to detail and adherence to stringent standards. Key aspects to consider include:
- Material Selection: Choosing materials that offer high strength-to-weight ratios and corrosion resistance is paramount.
- Design Considerations: Precision in design is crucial to ensure proper fit and function within the aerospace system.
- Performance Testing: Rigorous testing procedures are necessary to verify the reliability and durability of set screws in extreme aerospace conditions.
- Quality Assurance: Strict quality control measures must be in place to maintain the integrity of set screws and prevent failures.
- Regulatory Compliance: Compliance with industry regulations and standards is essential to guarantee the safety and performance of aerospace components.
Industrial Robotics
In the realm of industrial robotics, set screws serve as critical components that facilitate the secure attachment and alignment of various mechanical parts within robotic systems. Robot efficiency is greatly enhanced through the use of set screws, ensuring that components remain securely fastened during operation, ultimately contributing to improved overall performance.
Automation benefits are maximized as set screws aid in the precise assembly of robotic arms, joints, and other moving parts, enabling smooth and accurate movements. Programming advancements in robotics are supported by the reliability and stability that set screws provide, allowing for intricate and synchronized movements.
Precision engineering in industrial robotics relies on set screws for the meticulous alignment of components, ensuring seamless operation. These industrial applications underscore the indispensable role of set screws in optimizing robotic systems.
Telecommunications Infrastructure
Within the realm of telecommunications infrastructure, the meticulous alignment and secure fastening of critical components are essential for ensuring the seamless operation and optimal performance of various systems. Set screws play a vital role in this sector, particularly in the installation and maintenance of components such as fiber optic connections, network cables, wireless towers, and other equipment crucial for maintaining signal strength and efficient data transmission. Set screws provide stability and precision, ensuring that these components remain securely in place, thereby reducing the risk of signal loss or interruption. Their ability to firmly hold components in position is instrumental in maintaining the integrity of telecommunications networks, ultimately contributing to reliable and uninterrupted data transmission.
Key Uses of Set Screws in Telecommunications Infrastructure:
- Securing fiber optic connections.
- Fastening network cables.
- Anchoring wireless towers.
- Maintaining signal strength for optimal data transmission.
4. Types of Set Screws
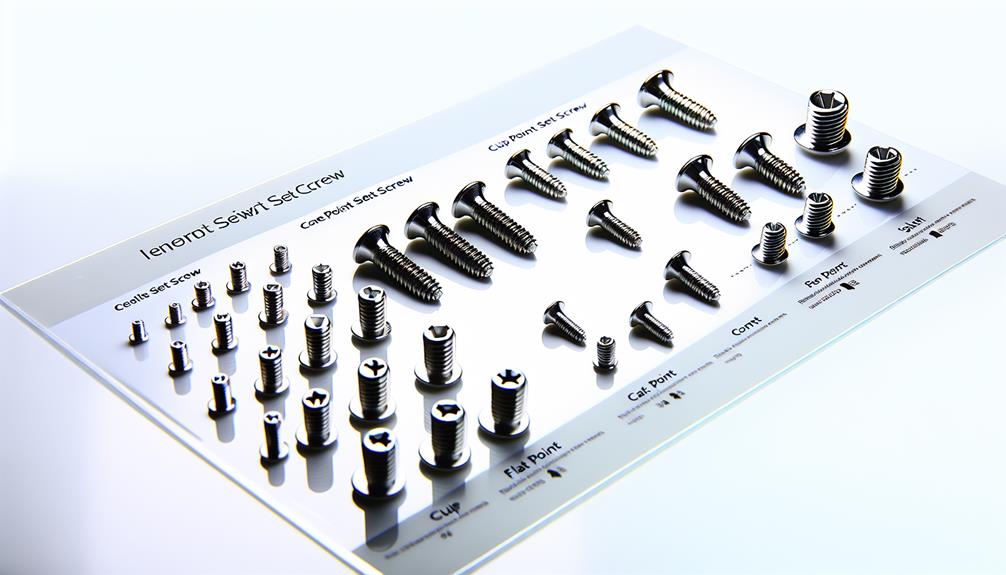
The different types of set screws can be categorized based on their point types, drive types (head-types), and specific set screw types. Understanding these variations is crucial for selecting the appropriate set screw for different applications.
Each type of set screw offers unique features and benefits that cater to specific needs in various industries.
4.1 Point types of Set Screws
Point types of set screws offer unique features tailored to specific applications.
Flat point set screws provide a flush surface against the mating part, ideal for frequent adjustments.
Cone point set screws, with their sharp ends, offer high holding power by penetrating deeply into the material they mate with.
Flat point
Among the various types of set screws available, the flat point set screw offers a specific design feature that distinguishes it from other point types.
- Point selection: Flat point for flush surface alignment.
- Thread engagement: Ensures secure fastening.
- Torque resistance: Resists loosening under load.
- Material compatibility: Suitable for softer materials.
Domed point
In contrast to the flat point set screw's flush surface alignment feature, the domed point set screw offers a rounded tip design that serves a distinct purpose in fastening applications. This type is particularly beneficial in precision machining, industrial automation, mechanical engineering, and custom fabrication. Domed point set screws are essential fastening solutions due to their ability to distribute pressure evenly, making them ideal for various industrial applications.
Cone point
Cone point set screws are known for their sharp, tapered tip that facilitates secure fastening in various applications requiring precise alignment.
- Cone point advantages, disadvantages
- Advantages: Provides strong grip
- Disadvantages: May damage softer materials
- Cone point dimensions, specifications
- Tapered tip angle: Typically around 118 degrees
- Cone point installation tips
- Ensure proper alignment before tightening
- Cone point material compatibility
- Ideal for harder materials like metal
Cup point
The cup point set screw features a rounded tip designed to create a firm hold on the mating surface. Cup point advantages include excellent resistance to loosening and vibration.
However, its disadvantages include potentially marring the surface. Common applications for cup point set screws are in gear assemblies and shaft collars.
These screws are typically made from alloy steel or stainless steel. Proper installation techniques involve ensuring the cup point makes full contact with the surface for optimal grip.
Extended point (pilot point, dog point)
Extended point set screws, also known as pilot point or dog point set screws, feature a specialized tip design aimed at specific applications requiring precise alignment and secure fastening.
- Point Variations: Different styles cater to various needs.
- Threaded Design: Ensures strong grip within a tapped hole.
- Installation Process: Requires careful alignment for effective use.
- Material Compatibility: Suitable for use with a range of materials.
These screws offer precise control and enhanced fastening capabilities.
Knurled cup point
Featuring a textured surface for enhanced grip, the knurled cup point set screw is designed to provide secure fastening in various applications.
With its knurled grip and custom design, this set screw offers enhanced stability through its unique texture.
Its increased durability and specialized finish ensure improved grip through precision engineering, making it ideal for custom applications that require versatile solutions.
4.2 Drive types (Head-Types) of Set Screws
The drive types, or head-types, of set screws play a crucial role in their application and performance. From the traditional straight slot for flathead screwdrivers to the more modern hex socket and square socket options, each drive type offers unique advantages in terms of torque, slippage resistance, and security. Understanding the characteristics of each drive type is essential for selecting the most suitable set screw for a particular fastening task.
Straight slot
Among the various drive types of set screws, the straight slot design remains a fundamental and widely used option in various applications.
- Slot dimensions: Standardized slots for compatibility.
- Material compatibility: Suitable for a wide range of materials.
- Torque requirements: Moderate torque for secure fastening.
- Installation techniques: Requires precise alignment for optimal performance.
Hex socket
In contrast to the straight slot design, the hex socket drive type of set screws offers a more secure fastening solution with its hexagonal socket for increased torque application. The hex socket set screws come in various socket sizes, catering to different torque requirements. They are compatible with a wide range of materials, have specific thread pitches, and can feature different surface finishes for enhanced performance.
Feature | Description |
---|---|
Socket sizes | Various sizes available |
Torque requirements | Depend on socket size |
Material compatibility | Compatible with many materials |
Thread pitch | Specific to each screw |
Surface finish | Can vary for different needs |
Square socket
Within the realm of set screws, the square socket drive type stands out as a distinctive option for efficient and reliable fastening solutions.
- Square Socket Advantages: Provides a strong grip.
- Socket Compatibility: Fits well with corresponding square keys.
- Socket Dimensions: Available in various sizes to suit different screw dimensions.
- Socket Material Options: Can be made from steel, stainless steel, or other materials for durability.
External hex
External hex drive type is a commonly utilized form of set screw for secure fastening applications. It requires a hex key for tightening, with wrench size determined by the screw's dimensions. Tightening torque must align with specifications to prevent damage.
Thread pitch influences the screw's grip strength, while the surface finish can impact corrosion resistance. Understanding these factors is crucial for effective implementation of external hex set screws.
External square
Utilizing a unique design, the external square drive type of set screw offers a distinct method for secure fastening in various applications.
- Internal thread
- Torque resistance
- Square head
- Thread engagement
This drive type ensures reliable fastening due to its internal thread, excellent torque resistance, square head for easy gripping, and optimal thread engagement, all while providing corrosion resistance for long-lasting durability.
Bristol spline
The Bristol spline drive type of set screw presents a specialized option for secure fastening, offering unique advantages in various applications. Its spline design provides enhanced torque transmission compared to other drive types, ensuring reliable fastening in demanding environments.
Common applications include aerospace and automotive industries. However, the manufacturing processes for spline set screws can be more complex, leading to higher production costs compared to traditional set screws.
4.3 Set screw types
The variety of set screw types offers versatility in fastening applications.
From the simplicity of Plain Cup Screws to the specialized designs like Dog Point Set Screws, each type serves specific purposes.
Understanding these variations is essential for selecting the most suitable set screw for different mechanical needs.
Plain Cup Screws
A highly effective type of set screw commonly used for preventing components from loosening is the cup point set screw. This design provides excellent vibration resistance and leaves a distinct ring dentation mark on the surface it secures.
For optimal performance, consider custom finishes, proper surface preparation, and selecting the right material options. Additionally, adhere to specific torque requirements during installation for optimal functionality.
Knurled Cup Screws
Among the various types of set screws, the knurled cup screw stands out for its serrated ridge design that enhances surface grip and minimizes loosening caused by vibrations.
Ideal for joinery applications, these screws offer excellent vibration resistance, but they may cause surface damage.
Their installation accessibility is convenient, but they cannot be reused due to the deflection of the knurl's cutting edges when tightened.
Material hardness is crucial for their effectiveness.
Flat Set Screws
Flat set screws provide a distinct advantage over knurled cup screws by enabling even distribution of compression force with minimal penetration on the target surface, making them suitable for applications where precise adjustments and gentle holding power are essential.
- Surface contact
- Compression force
- Thin walls
- Soft materials
Oval Set Screws
Oval set screws are particularly suited for applications that require frequent adjustments while minimizing surface damage at the contact site. The oval point design of these set screws helps to distribute pressure over a small contact area, allowing for slight adjustments without the risk of loosening the screw. This makes oval set screws ideal for situations where precise control and regular modifications are necessary.
By minimizing surface damage at the contact site, these set screws help maintain the integrity of the materials being fastened. Whether in machinery, electronics, or other equipment, oval set screws provide a reliable solution for applications that demand flexibility and precision in adjustment mechanisms.
Best For: Those in need of frequent adjustments in applications where minimizing surface damage is crucial.
Pros:
- Enables slight adjustments without loosening the screw
- Minimizes surface damage at the contact site
- Ideal for applications requiring regular modifications
Cons:
- May not be suitable for applications that require a larger contact area.
Dog Point Set Screws and Half-Dog Point Set Screws
In the realm of set screw variations, the Dog Point Set Screws and their counterparts, the Half-Dog Point Set Screws, offer distinct functionalities and applications within mechanical assemblies.
- Torque Requirements: Dog point set screws typically require higher torque due to their extended tips, while half-dog point set screws need less torque for installation.
- Material Compatibility: Both types are compatible with a wide range of materials, but half-dog point set screws are more suitable for softer materials.
- Installation Process: Dog point set screws are commonly used to secure rotating components, while half-dog point set screws are ideal for permanent settings.
- Removal Techniques: Dog point set screws are easier to remove due to their tubular tip design, while half-dog point set screws may require more effort.
Soft-Tipped Set Screws
Soft-tipped set screws provide a unique solution for applications requiring gentle contact with delicate surfaces or materials. When using soft-tipped set screws, consider the specific soft-tipped applications to ensure proper installation. It is essential to verify material compatibility to prevent damage.
Advantages include reduced risk of surface marring, but disadvantages may include lower torque capacity. Regular maintenance checks are necessary to ensure continued effectiveness.
Ball-Point Set Screws
Ball-Point set screws offer a specialized design feature that enhances precision and reliability in various mechanical applications.
- Ball point advantages, disadvantages
- Advantages include reduced surface damage.
- Disadvantages may include potential for misalignment.
- Ball point installation tips
- Ensure proper alignment.
- Use appropriate tools for installation.
- Ball point material compatibility
- Ideal for softer materials.
- Ball point maintenance techniques
- Regularly check for wear.
- Replace if necessary.
Nylon Tip Set Screw
A Nylon Tip Set Screw is a specialized fastening component designed to provide gentle yet secure gripping without causing damage to the surface it is applied to. This type of set screw offers advantages such as material compatibility, installation technique, torque requirements, specific tip design, thread engagement, and surface finish. Additionally, Nylon Tip Set Screws exhibit chemical resistance, heat tolerance, optimal friction coefficient, and wear resistance.
Feature | Description | Benefit |
---|---|---|
Material Compatibility | Compatible with various materials | Prevents surface damage |
Torque Requirements | Specific torque needed for installation | Ensures secure fastening |
Tip Design | Nylon tip for gentle gripping | Prevents surface abrasion |
Thread Engagement | Strong engagement with threaded surface | Enhances stability |
Surface Finish | Smooth finish to prevent marring | Maintains surface integrity |
Cone Point Set Screw
Precision is a defining characteristic of the Cone Point Set Screw, a fastening component known for its specialized tip design.
Key Features of the Cone Point Set Screw:
- Precision machining ensures accurate dimensions.
- Optimal thread engagement for secure fastening.
- High torque resistance for reliable performance.
- Enhanced material compatibility for diverse applications.
Engineers and professionals value the Cone Point Set Screw for its precise installation technique and robust grip.
5. How to Select a Set Screw Point Type

When selecting a set screw point type, it is crucial to consider factors such as:
- Material hardness
- Application requirements
- Surface damage prevention
- Vibration resistance
- Installation accessibility
These aspects play a key role in determining the most suitable point type for the specific fastening task at hand. By carefully evaluating these considerations, one can ensure optimal performance and longevity of the set screw in its intended application.
Understand Application Requirements
Selecting the appropriate set screw point type is crucial in meeting the specific application requirements for fastening components securely. When understanding application requirements, consider factors like material compatibility and installation accessibility.
Vibration resistance and cost evaluation are essential to ensure long-term stability. Assess surface damage and explore different point types to prevent any adverse effects on the components. Consult suppliers for guidance on material hardness and to guarantee the right choice.
Review the availability of the set screw types and seek clarification on any FAQs to make an informed decision. Taking these steps will help in selecting the most suitable set screw point type for your application needs.
Assess Material Hardness
Assessing material hardness plays a critical role in determining the appropriate set screw point type for optimal fastening performance. When choosing the right set screw for your application, it is essential to consider the hardness of the materials being joined. Matching the hardness of the set screw point to that of the material it will engage with ensures proper material compatibility and prevents issues such as thread stripping or deformation.
Additionally, understanding the torque requirements of the application is crucial in selecting the ideal set screw point type to achieve the necessary clamping force without damaging the components. Proper thread engagement and surface finish are also influenced by the material hardness, further emphasizing the importance of assessing hardness in set screw selection.
Consider Surface Damage
Surface damage prevention is a key factor in determining the most suitable set screw point type for effective fastening. When considering the potential for surface damage, it is essential to focus on various aspects to ensure the longevity and efficiency of the fastening application.
To select the appropriate set screw point type, consider the following:
- Surface protection, material compatibility: Ensure the set screw material is compatible with the surface it will be in contact with to prevent any chemical reactions or wear.
- Corrosion prevention, impact resistance: Choose a point type that offers corrosion resistance and can withstand impacts to maintain the integrity of the surface.
- Coating options, durability assessment: Evaluate different coating options to enhance durability and assess their effectiveness in preventing surface damage.
- Thread engagement, torque requirements: Determine the optimal thread engagement and torque needed to secure the set screw without causing surface damage.
Evaluate Vibration Resistance
When considering the effectiveness of a set screw point type, evaluating its vibration resistance is crucial for ensuring secure fastening in dynamic environments. Corrosion resistance is vital to prevent degradation over time, while material compatibility ensures the screw can withstand the operating conditions.
Adhering to specified torque specifications is essential to maintain the screw's integrity under vibration. Additionally, proper thread engagement is key to enhancing resistance to vibrational forces.
Lastly, using the correct installation tooling is crucial for securely fastening the set screw and maximizing its vibration resistance. By carefully considering these factors, you can select a set screw point type that offers optimal performance in high-vibration settings.
Review Installation Accessibility
To ensure ease of installation and accessibility when selecting a set screw point type, careful consideration of the screw's design and compatibility with the application is essential. When reviewing installation accessibility, the following factors should be taken into account:
- Accessibility Analysis: Conduct a thorough assessment of the installation environment to identify any potential barriers.
- Installation Challenges: Anticipate and address any difficulties that may arise during the installation process.
- Space Constraints: Ensure that the set screw point type chosen can fit within the available space without causing interference.
- Ergonomic Considerations: Prioritize set screw designs that are ergonomically friendly for users, facilitating ease of use and maintenance.
Consult with Manufacturers or Suppliers
For expert guidance on choosing the most suitable set screw point type for your specific application, consulting with reputable set screw manufacturers or suppliers is highly recommended. These professionals can provide valuable insights into custom options, material recommendations, and technical specifications tailored to your needs.
Whether your project involves special applications or requires specific installation tips, manufacturers or suppliers can offer expertise to ensure optimal performance. By collaborating with experts in the field, you can make informed decisions that align with your requirements and preferences.
Their industry knowledge and experience can help you navigate the wide range of set screw point types available, guiding you towards the most effective solution for your particular situation.
Consider Cost and Availability
Considering the cost and availability of different set screw point types is essential in making an informed decision, especially after consulting with manufacturers or suppliers for expert advice on selecting the most suitable option. When evaluating set screw point types, it is crucial to prioritize cost effectiveness, material selection, customization options, lead time, and quality assurance.
To ensure control over the decision-making process, here are key points to focus on:
- Cost Effectiveness: Determine the overall cost of the set screw, including maintenance expenses.
- Material Selection: Choose a material that aligns with the specific requirements of the application.
- Customization Options: Assess the flexibility for customization based on unique needs.
- Lead Time and Quality Assurance: Consider the production lead time and verify the quality standards for long-term reliability.
Frequently Asked Questions
What Is the Difference Between a Set Screw and a Regular Screw?
A set screw differs from a regular screw by its specific use in fastening components together through thread engagement. It offers advantages such as enhanced material compatibility, anti-vibration properties, and may require specialized installation tools due to its design. Surface finish also plays a role in its effectiveness.
Can Set Screws Be Used in Outdoor or Corrosive Environments?
Set screws can withstand outdoor or corrosive environments with features like rust resistance, waterproof coatings, corrosion protection, and material compatibility. Their design ensures outdoor durability, making them suitable for various applications in challenging conditions.
Are Set Screws Reusable or One-Time Use Only?
Set screws are typically reusable if not damaged during installation. Proper installation techniques, such as applying the right amount of torque, can ensure reusability. Set screws made from durable materials like stainless steel are ideal for various applications, offering advantages like secure fastening.
What Is the Maximum Torque That Can Be Applied to a Set Screw?
The maximum torque that can be applied to a set screw depends on factors such as material strength, thread engagement, and torque capacity. It is crucial to consider application requirements to determine the appropriate torque for optimal performance.
Can Set Screws Be Used in High Temperature Applications?
Set screws can be used in high temperature applications with careful material selection, considering heat resistance, proper installation tips to avoid loosening, surface treatment for improved performance, and accounting for thermal expansion to maintain secure fastening.
Mikehardware-your trusted Custom Screw manufacturer
In conclusion, set screws are versatile fasteners that play a crucial role in various applications by securely holding components together.
With different types of set screws available, selecting the right point type is essential for optimal performance. Whether it's a cup point, cone point, flat point, or knurled point, each type has its unique advantages depending on the specific use case.
Understanding the different types of set screws can help ensure successful fastening solutions in various industries.
At Dongguan Mike Hardware Co., Ltd., precision engineering meets innovation, delivering impeccable CNC product manufacturing solutions. Explore our array of customized fasteners, screws, and coatings, ensuring your projects excel in performance, precision, and quality.
Elevate your engineering prowess with our tailored solutions—Contact us for a free quote of your ideal Set Screw.