Bolt Manufacturing Process: Crafting Quality Hardware Components
The efficiency and reliability of hardware components, such as bolts, are essential for the smooth functioning of various industries. In order to ensure the production of high-quality bolts, it is crucial to understand the manufacturing process involved.
This article aims to explore the bolt manufacturing process, focusing on the methods employed and customization options available for specific industries. By delving into these aspects, readers will gain a comprehensive understanding of how quality hardware components are crafted through precise manufacturing processes.
1.What Are Blots?
Blots are threaded fasteners used to join two or more components together, typically made from metal and characterized by a cylindrical shaft with a head at one end and external threads on the other end. They are widely employed in various industries such as construction, automotive, and manufacturing due to their ability to provide strong and reliable connections.
The cylindrical shaft of a bolt is designed to fit into pre-drilled holes in the components being joined. The head of the bolt provides a surface for applying torque during installation and removal, while the external threads allow for secure attachment when combined with nuts or tapped holes. This design ensures that bolts can withstand significant forces without loosening or breaking under load.
Bolts come in different sizes, shapes, and materials depending on the specific application requirements. Commonly used materials include steel alloys such as carbon steel, stainless steel, and alloy steel. These materials offer high tensile strength, corrosion resistance, and durability necessary for various environments.
Understanding what bolts are made of is crucial to comprehend how they can effectively serve their purpose in different industries. In the following section, we will explore the diverse materials used in manufacturing bolts.
2.What Are Bolts Made Of?
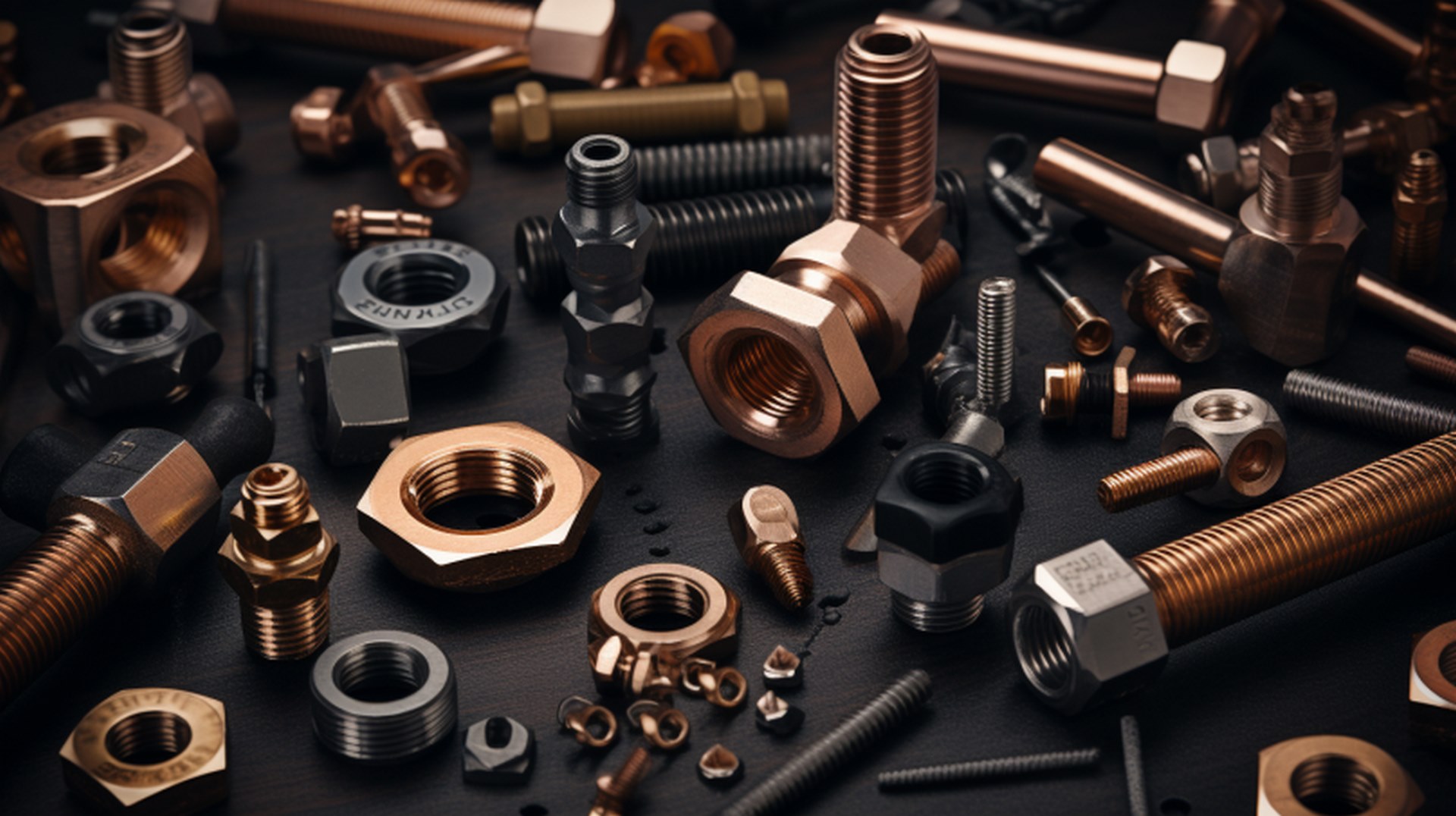
Common Materials Of Blots
Metal alloys, such as steel and stainless steel, are commonly used materials in the production of bolts. These alloys offer a combination of strength, durability, and corrosion resistance that make them ideal for this purpose.
Here are some key points about the materials used in bolt manufacturing:
- Steel: This alloy is widely utilized due to its exceptional strength and toughness. It can withstand high levels of stress without deforming or breaking.
- Stainless steel: With its added chromium content, stainless steel offers excellent resistance to corrosion, making it suitable for applications where bolts may be exposed to moisture or harsh environments.
- Titanium: Known for its lightweight yet robust nature, titanium is often used in industries requiring weight reduction without compromising on strength.
- Brass: This alloy is primarily employed for non-industrial applications such as electrical fittings or decorative purposes due to its attractive golden color and ease of machining.
- Aluminum: Its low density makes aluminum an appealing choice when weight reduction is critical. It also exhibits good resistance against corrosion.
Understanding the materials used in bolt manufacturing leads us to explore the most common method by which these hardware components are crafted.
3.What is the most common bolt manufacturing method?
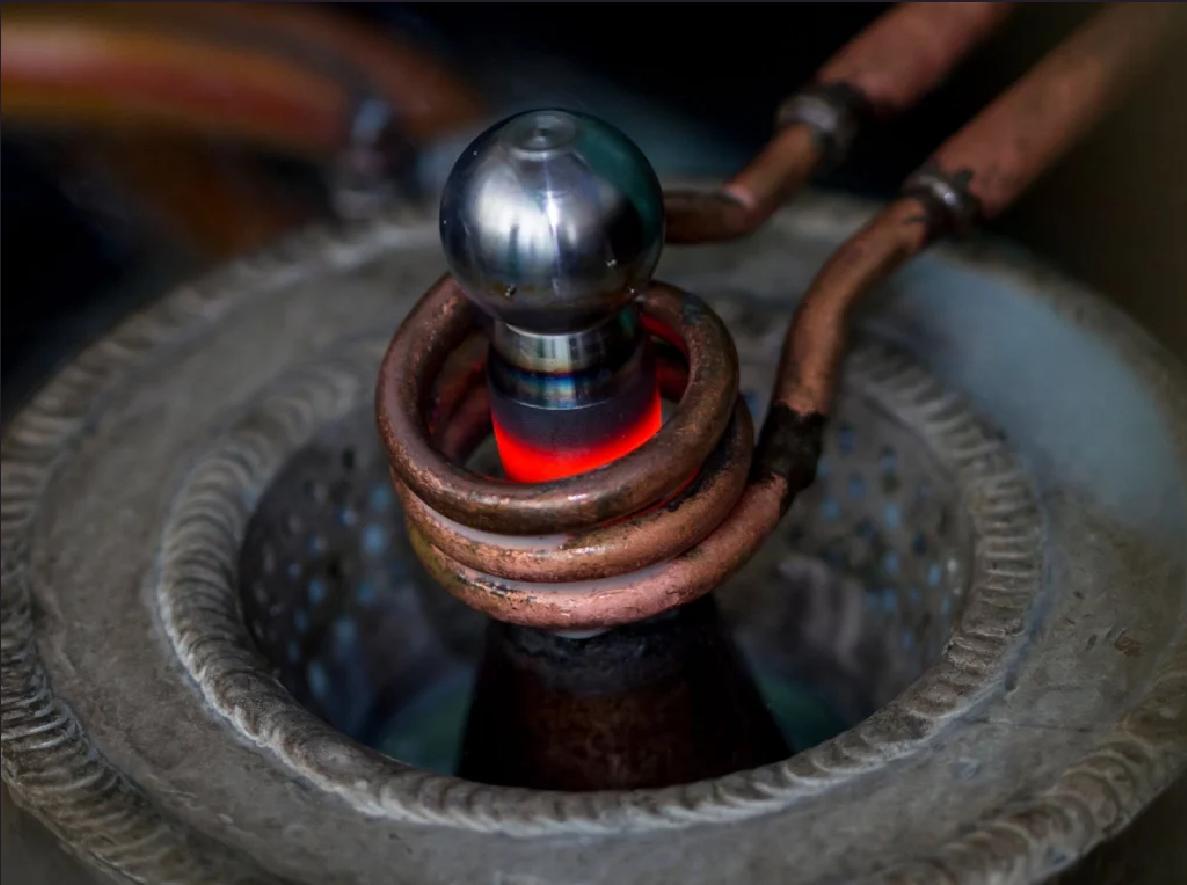
Bolt manufacturing involves several methods and processes, with each method tailored to produce bolts of varying sizes, materials, and specifications. Some common bolt manufacturing methods include:
Cold Heading: This method involves cutting and shaping wire or rod stock into the desired shape while cold-forming it under high pressure. Cold heading is efficient and suitable for producing standard bolts in large quantities.
Hot Forging: Hot forging involves heating a metal bar or rod to a specific temperature and then shaping it using dies and presses. It is used for manufacturing high-strength and specialized bolts, such as those for aerospace and automotive applications.
Thread Rolling: After initial shaping, bolts undergo thread rolling to create precise threads. Thread rolling uses hardened steel dies to deform the bolt's surface, resulting in stronger and more durable threads.
Machining: Machining processes like CNC milling and turning are used to produce custom bolts with complex shapes or non-standard specifications. Machining offers versatility and precision in bolt manufacturing.
Wire Drawing: Wire drawing is used to reduce the diameter of a metal wire or rod to the desired size. This method is commonly used for manufacturing smaller diameter bolts and threaded fasteners.
The choice of manufacturing method depends on factors such as the bolt's size, material, intended application, and required specifications. Custom bolts for specialized industries may require a combination of these methods to meet precise requirements for strength, durability, and performance.
Now that we have explored one prevalent bolt manufacturing technique, let us delve into how bolts are manufactured without using 'step.'
4.How Are Bolts Manufactured?
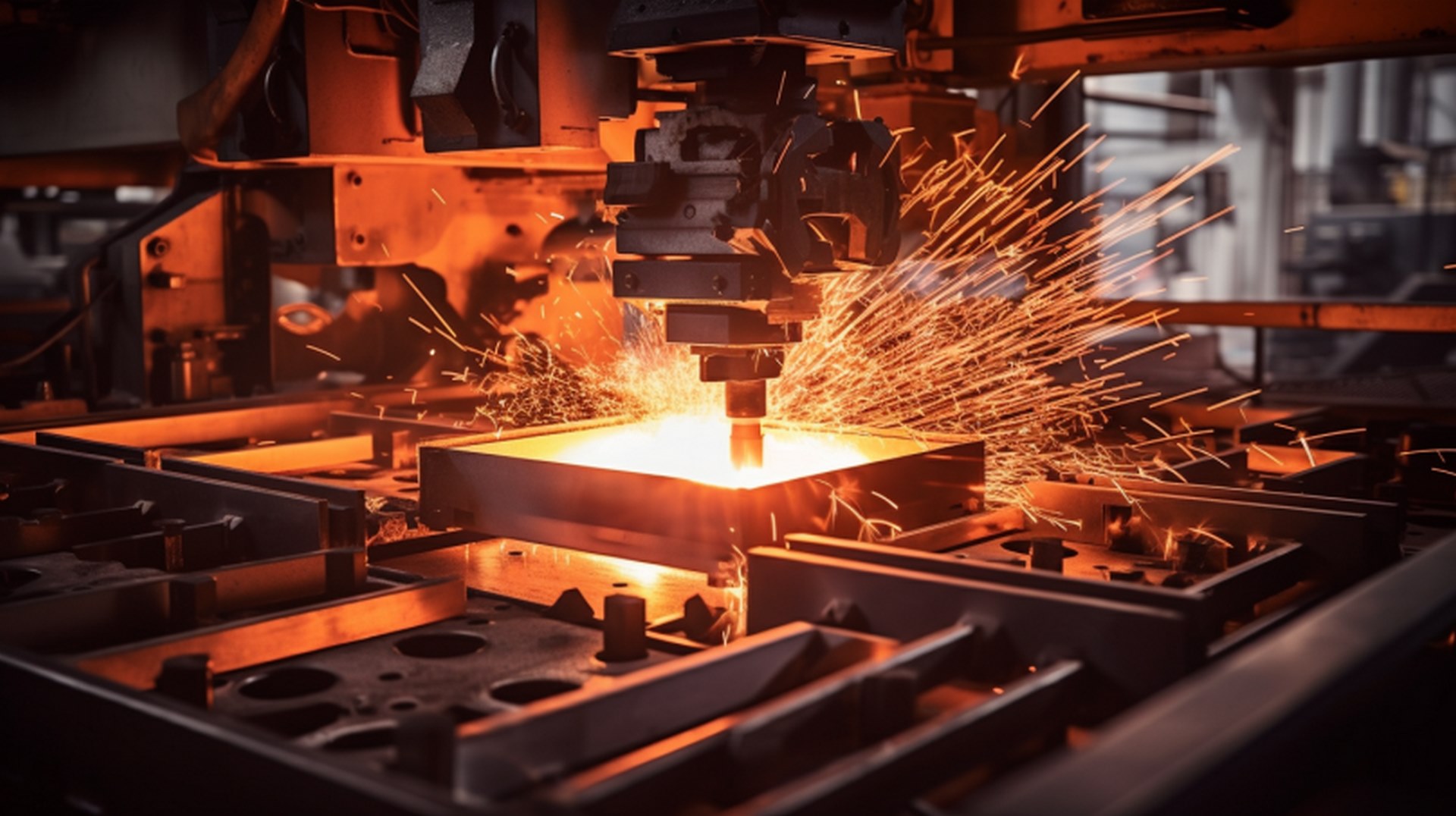
A commonly employed method in the production of bolts involves the shaping and forming of metallic raw materials into desired configurations through a specific manufacturing process. This process typically consists of several steps that are executed with precision to ensure the creation of high-quality hardware components.
The following list provides an overview of these steps:
- Raw material selection: High-quality metals, such as steel or stainless steel, are chosen based on their properties and suitability for bolt production.
- Heating: The selected raw materials are heated to a specific temperature to increase their malleability and facilitate the subsequent forming processes.
- Forming: The heated metal is then shaped into the desired bolt configuration using various methods, including forging or cold heading.
- Threading: After forming, threads are created on the bolt's exterior surface through processes like rolling or cutting.
- Finishing: Finally, bolts undergo finishing operations like heat treatment, cleaning, and coating to enhance their strength, durability, and corrosion resistance.
With an understanding of how bolts are manufactured, we can now explore whether they can be customized for specific industries without compromising quality or functionality.
5.Can Bolts Be Customized for Specific Industries?
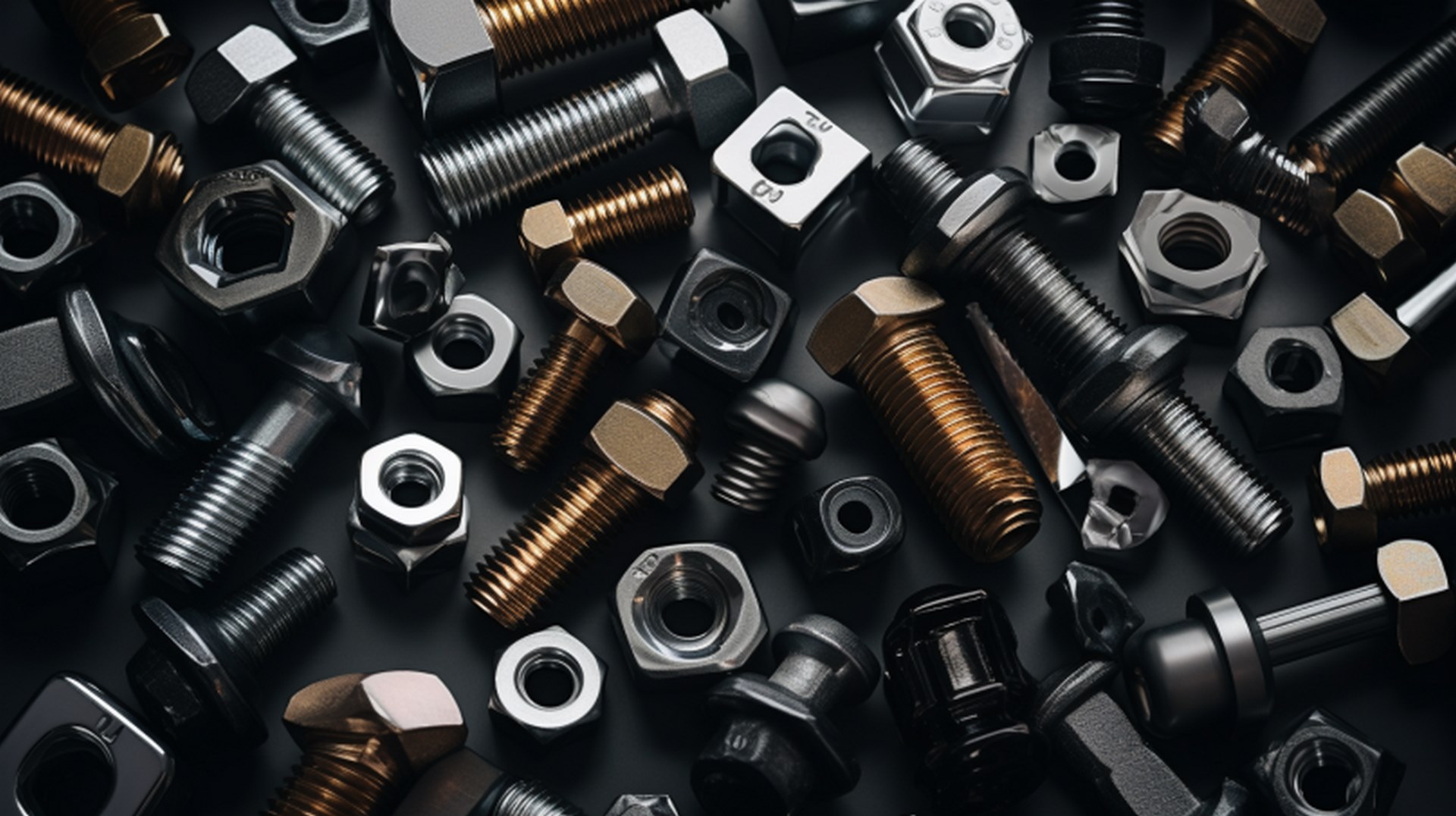
Customization of bolts for specific industries involves tailoring the structural and surface characteristics to meet the unique requirements and demands of various sectors. This process allows bolts to be optimized for specific applications, ensuring that they perform effectively in their intended environments. The customization can include modifications such as altering the material composition, adjusting dimensions, or applying specialized coatings.
In industries where extreme temperatures are present, such as aerospace or oil and gas, bolts may need to withstand high heat or corrosive conditions. In these cases, materials with superior heat resistance or corrosion resistance are utilized. Additionally, bolts used in industries like automotive or construction may require enhanced strength and durability to withstand heavy loads. These factors must be carefully considered when customizing a bolt to ensure it meets the precise needs of the industry it will be employed in.
Transitioning into the subsequent section about 'how are large bolts manufactured,' it is important to understand that once the customization specifications have been determined, manufacturers employ various techniques to produce high-quality hardware components efficiently and accurately.
6.How Are Large Bolts Manufactured?
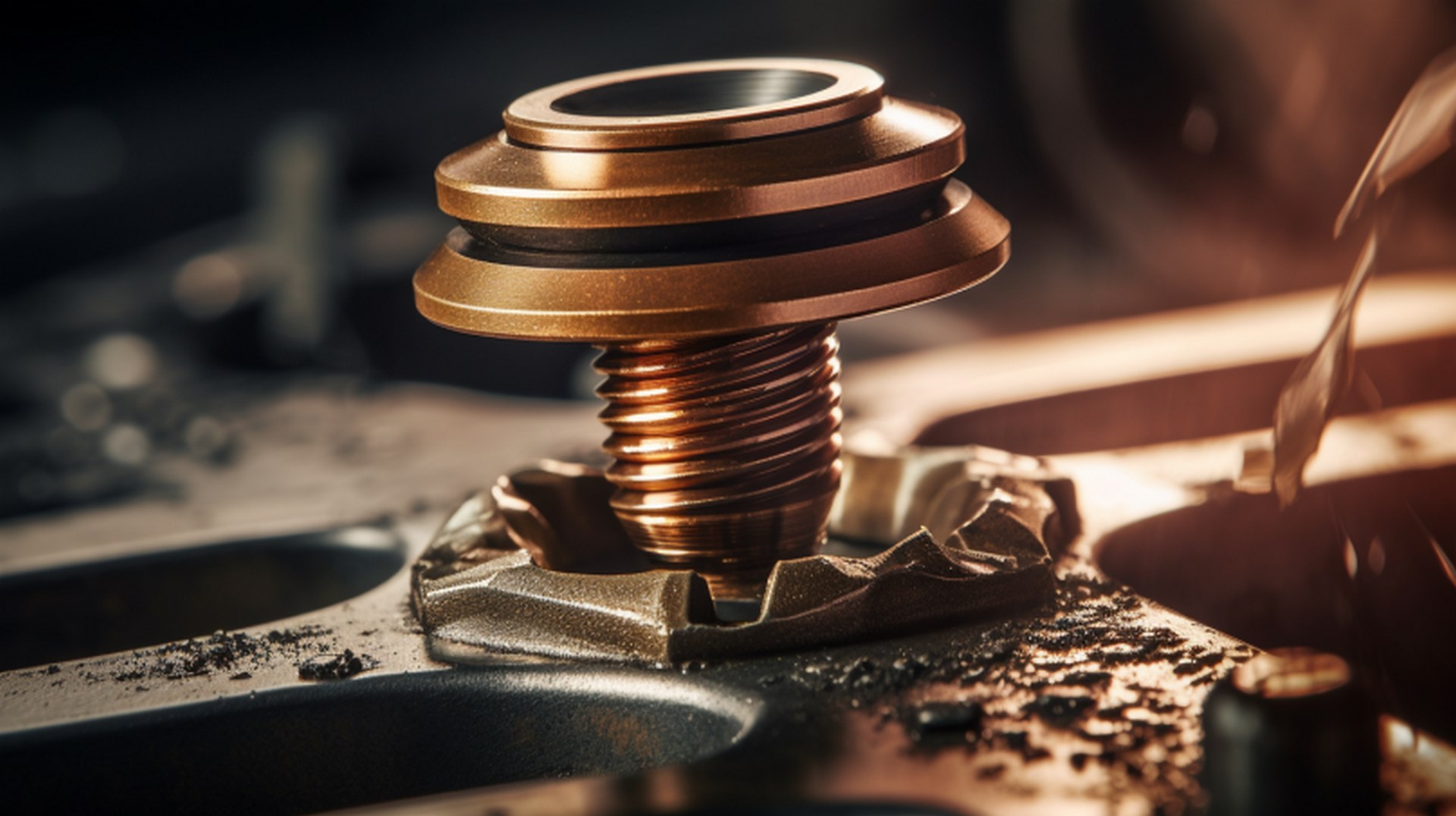
The manufacturing of large bolts, often essential components in heavy industries like construction and mining, involves a meticulous process tailored to their size and specific requirements. It all begins with the careful selection of materials, typically carbon steel, alloy steel, or stainless steel, depending on the application. These materials are then cut into manageable lengths before being heated to an appropriate temperature for shaping. Large bolts are usually formed using methods like hot forging or rolling, with the choice depending on size, material, and specifications. Thread formation is crucial, and it's often achieved through thread rolling, a cold-forming process that ensures the creation of strong, precise threads. Heat treatment follows to enhance mechanical properties, including hardness and strength.
Machining processes like milling, drilling, or turning may be required for precise dimensions, and thorough quality control checks are performed at each stage, including dimensional assessments, hardness testing, and thread inspection. Coatings, such as hot-dip galvanization or zinc plating, are applied to protect against corrosion. The final inspection guarantees that these large bolts meet industry standards and customer specifications before packaging and shipping to their intended destinations.
Understanding how large bolts are manufactured provides insight into the meticulous process involved in producing reliable hardware components. This knowledge sets the stage for exploring which manufacturing production process is used for nut and bolts.
7.Which Manufacturing Production Process Is Used For Nut And Bolts?
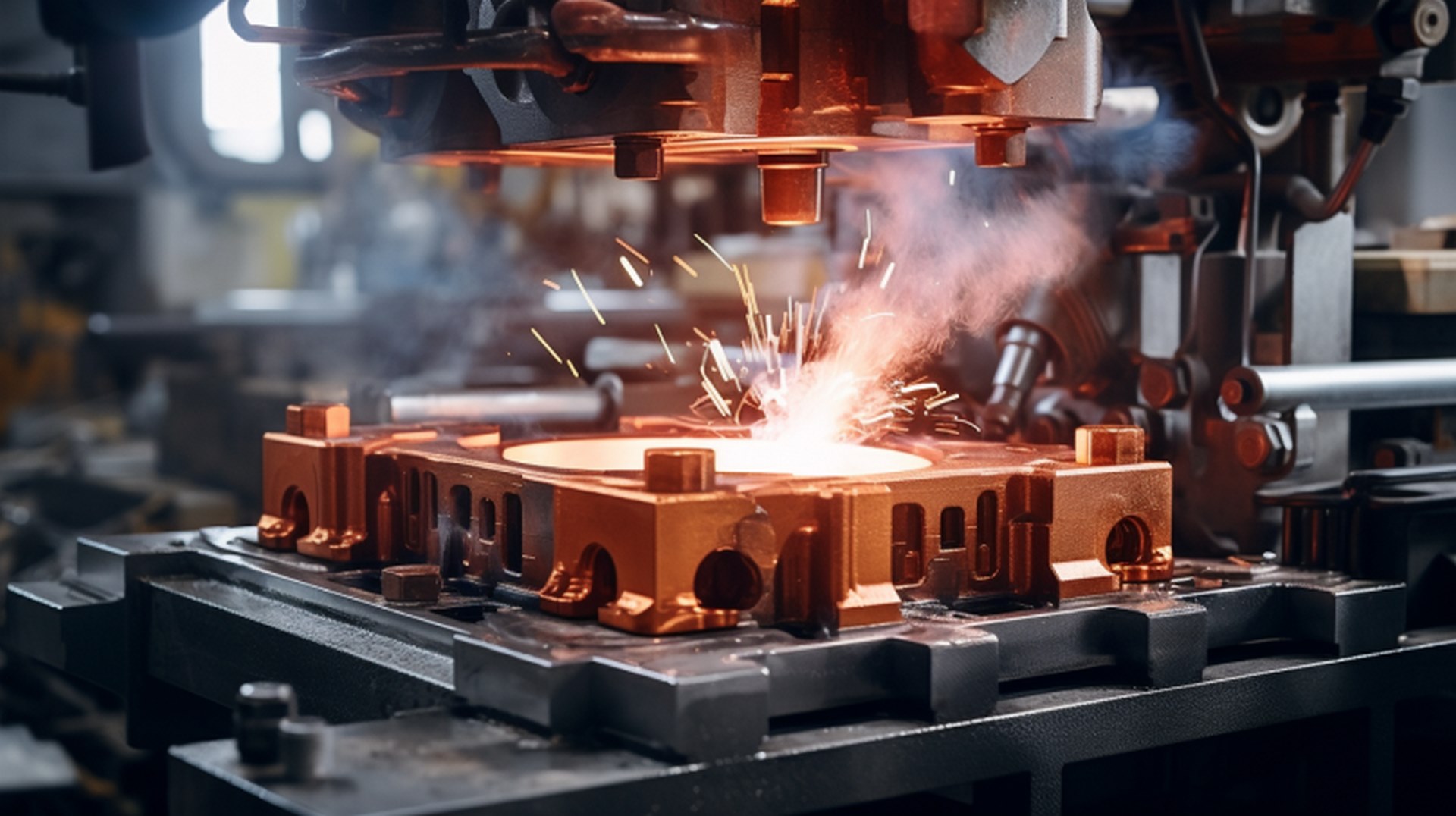
The production of nuts and bolts typically involves a series of carefully planned steps to ensure their accurate dimensions and reliable performance. These steps are part of the manufacturing production process that is used to create these essential hardware components. The specific process may vary depending on factors such as the type of material being used, the intended application, and the desired quality standards.
To give an overview of the manufacturing production process for nuts and bolts, let's consider a simplified representation in a table format:
Stage | Description | Key Activities |
1 | Material Preparation | - Procuring raw materials |
- Inspecting materials for quality | ||
- Cutting or shaping materials | ||
2 | Forming | - Cold or hot forging |
- Extrusion | ||
- Roll threading | ||
3 | Heat Treatment | - Annealing (softening) |
- Tempering (strengthening) | ||
- Quenching (hardening) | ||
4 | Machining | - Turning |
- Milling | ||
- Drilling | ||
5 | Finishing | - Coating or plating for corrosion resistance |
- Polishing or grinding for a smooth surface |
This table provides a glimpse into the various stages involved in nut and bolt manufacturing. Each stage plays a crucial role in ensuring that the final product meets industry standards and customer requirements.
To learn more about our steel bolt manufacturing processes at MikeHardware, we invite you to explore our detailed procedures on our website.
In conclusion, the bolt manufacturing process is a precise and intricate craft that produces quality hardware components.
From understanding what bolts are and their composition to exploring the most common manufacturing method, this article has shed light on the intricacies of bolt production.
The ability to customize bolts for specific industries and manufacture large bolts highlights the adaptability of this process.
By using a meticulous manufacturing production process, nut and bolts are created with precision and durability.
Learn More About Our Steel Bolt Manufacturing Processes at Mikehardware
One can gain further insight into the steel bolt manufacturing processes at MikeHardware by exploring their detailed procedures on their website. MikeHardware is committed to producing high-quality hardware components, and their steel bolt manufacturing processes reflect this dedication.